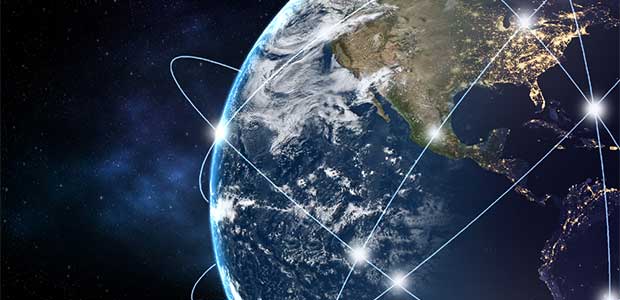
Implementing an Enterprise-Wide Ergonomics Process
Practical steps to take to improve consistency across locations and reduce workload for your ergonomics site leaders.
- By Rick Barker, Rachel Zoky
- Sep 01, 2019
Successfully launching and maintaining an ergonomics process across multiple countries can be challenging, especially when your sites aren’t large enough to warrant a person dedicated to ergonomics. In all but the largest manufacturing sites, ergonomics is one of many hats that a person must wear. This requires the enterprise ergonomics process owner to create systems that reduce the burden on site leaders.
There are some practical steps you can take to improve consistency across locations and reduce the workload for your ergonomics site leaders. Some of the key challenges when it comes to large-scale ergonomics processes include:
- choosing reportable metrics that are applicable to different plant sizes and production constraints
- embedding the ergonomics process into the daily operations of distant facilities
- establishing consistent processes for including ergonomics in new product and equipment design
- sharing solution ideas and problem-solving efforts across sites
Tracking Success Across Diverse Sites
Comparing injury data from multiple locations in different countries is challenging because the criteria for classifying an injury as work-related can vary considerably among them. You can partially address this challenge by establishing specific injury definitions for all locations to use; however, this may result in duplication of effort and underreporting. Sometimes, even the most accurate injury data is still a lagging metric. Tracking risk scores and risk reduction, rather than injury reduction, allows for consistent measures that aren’t affected by local regulations. By using the same musculoskeletal disorder (MSD) risk assessment methodology across all locations and tracking the risk reduction at each site, you can have a meaningful, consistent measure of success.
The goals for individual sites should allow for variation based on the baseline risk, or starting point, for each location. Some product types have more inherent MSD risk than others, and some processes that require manually intensive operations are strategically sourced to regions with lower labor costs. However, manually intensive tasks will generally have higher MSD risk levels, so a single, enterprise-level goal regarding MSD risk reduction may not be appropriate for all sites. For long-term success, work directly with each site to establish a challenging, yet reasonable, goal for that site. Using the same measure for each location but updating the goal according to the size, resources, and baseline situation of each site creates a more attainable goal structure. Ensuring the goals for each location are achievable maximizes the motivation to work toward those goals.
Embedding the Ergonomics Process into Daily Operations
Fully embedding ergonomics into daily operations is the “holy grail” for many ergonomics practitioners. Geographic distances and language barriers often add to the challenge, but this doesn’t have to be the case. Several tactics can help you embed the process in diverse locations:
Have a clear plan. A clear plan conveys the roles, responsibilities, and expectations for everyone in the organization. An enterprise-level plan must often strike a balance between providing enough direction to drive consistent action and allowing sufficient flexibility to enable individual sites to accomplish the overall goals within the constraints of local regulations and facility size.
Choose strong regional or local champions. Selecting the right person to own ergonomics at both the regional and site levels is critical. Most regional and site champions are adding ergonomics to the large set of responsibilities they already have, so ergonomics won’t be their primary job. It is a common mistake to think that EHS needs to lead in every region. Effective ergonomics champions are also commonly found in engineering, facilities, maintenance, operations, and other job functions. The most important skills for a regional champion to have are being effective at implementing changes and possessing the language skills to communicate with other regional champions. The specific knowledge and skills relating to ergonomics can be easily learned.
Provide consistent messaging across languages. This is one of the strengths of e-learning. The same message can be conveyed to people in a variety of languages. E-learning also provides a resource that can be referenced and reviewed at any time, whenever a situation requires clarification.
Incorporating Ergonomics into the Design Process
Don’t overlook the importance of design guidelines for ergonomics. Selecting, purchasing, or building equipment that is appropriate for the end user is the most cost-effective and efficient way to reduce MSD risk. Clear design guidelines are the key to completing this task successfully. Keep in mind that people in different parts of the world aren’t all the same size; design guidelines should account for these regional differences. The most effective ergonomics processes have design guidelines for each major region of the world. Effective processes also include plans in case the production location changes or expands, and they incorporate enough adjustability to accommodate all regions where the equipment could foreseeably be installed.
Simply having new design guidelines for ergonomics typically isn’t enough; you also must find the hidden places where old guidelines may exist, and you’ll need to embed the new guidelines directly into the appropriate design and purchasing processes. Design guidelines different from the most current ones for ergonomics have often been added into a wide variety of internal documents without prior review by the ergonomics process owner. They can exist in EHS checklists, lean workstation guidelines, purchasing specifications, packaging criteria, and engineering files. Different divisions and regions may also have collected their own unique information in the past. Uncovering all these locations with their own guidelines requires conversations with stakeholders in each function and region. This also requires learning about, and participating in, the different processes, particularly the new product and equipment development process.
To be effective, design guidelines for ergonomics must be used at the appropriate times. This is why it is important to understand the new product development process and the corresponding processes for the design and purchase of equipment accompanying the new product. When use of the guidelines is introduced too early in the process, the decisions that impact ergonomics aren’t being made and the guidelines can easily be overlooked. If the guidelines are introduced too late in the process, important decisions have already been made that would impact the cost and feasibility of changing to meet the design guidelines. Note that different aspects of the guidelines are often appropriate at different stages in the process. Reviewing the right guidelines during the optimal stages of the design process will result in the most cost-effective and efficient decisions for ergonomics.
Sharing Solution Ideas and Challenges
Many organizations produce the same or very similar products in multiple locations, resulting in similar ergonomics challenges across these different sites. If an effective process already exists identifying and improving these shared issues, the best option is to include ergonomics in the existing process. Unfortunately, effective cross-location problem-solving processes for any issues are less common and effective than is generally desired. If your organization does not already have an effective process for sharing these issues among sites, establish a process specifically for ergonomics.
First, create a database that contains both root cause descriptions and information regarding effective countermeasures. Ideally, this database should also include the name of the person leading each job improvement effort so that people from other locations can make direct contact.
Next, create a forum for routinely sharing this information. Conference calls remain the best way to start this sharing process. Once the sharing process and use of the database information become standard practice, the frequency of regular conference calls can be reduced. Remember to share not just the solutions but the specific challenges. In some cases, other sites may have an undocumented improvement for an issue already in place. Most of the time, the challenge exists in all locations and combining ideas to solve the shared problem results in more effective solutions.
Share your database of information with new product development teams. If the manufacturing sites have already solved a problem, incorporate those solutions into new design ideas. Because of technical and financial limitations, some hazards can only be addressed during the design stage. Therefore, it is particularly important to address those issues that couldn’t be resolved by manufacturing in the design stage of the next product iteration.
Summary
Successfully implementing an enterprise-wide ergonomics process in multiple countries requires solid planning, good project management, and the right tools to support the process. Two key aspects of planning are selecting effective regional champions and creating a consistent overall plan that is flexible enough to accommodate variations in region and facility size. Good project management starts with establishing regular, consistent communication with and among sites. This requires having the right tools to support the process, including multilingual training materials, design guidelines specific to the regions of operation, and a database that tracks root cause information and effective solutions across locations.
This article originally appeared in the September 2019 issue of Occupational Health & Safety.