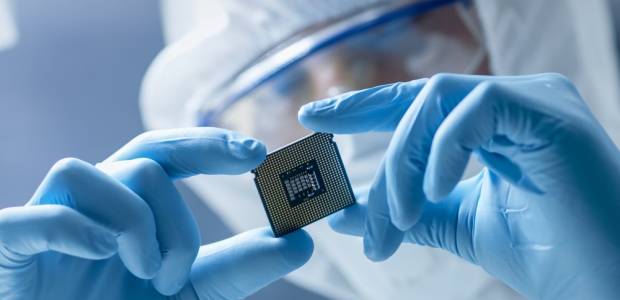
New NIOSH Documents Out on Nanotechnology Workplace Design
Four new documents offers tips on the design and use of exposure controls for nanomaterial production, post processing, and use. They are posters that pose questions employers and workers should consider before starting work with a nanomaterial and list options to reduce exposures to nanomaterials based on the physical form.
NIOSH has posted four new documents addressing the design of nanotechnology workplaces so that the workers' exposures to nanomaterials while conducting common processes and tasks will be controlled.
Engineered nanomaterials are intentionally produced to have at least one primary dimension less than 100 nanometers (nm), and they are used in areas that include medicine, electronics, biomaterials, and consumer products. The workers at sites using or making engineered nanomaterials may inhale nanoparticles on a daily basis, posing a potential respiratory hazard.
"Researching, developing, and utilizing these nano properties is at the heart of new technology, just as worker safety is at the heart of what we do at NIOSH," NIOSH Director Dr. John Howard said. "The information contained in these new workplace design solution documents provide employers with strategic steps towards making sure their employees stay safe while handling nanomaterials."
The four documents provide recommendations on minimizing exposures during:
- handling and weighing of nanomaterials when scooping, pouring, and dumping
- harvesting nanomaterials and cleaning out reactors after materials are produced
- processing nanomaterials after production
- working with nanomaterials of different forms, including dry powders or liquids
Each document offers tips on the design and use of exposure controls for nanomaterial production, post processing, and use. They are posters that pose questions employers and workers should consider before starting work with a nanomaterial and list options to reduce exposures to nanomaterials based on the physical form. The posters can be displayed in a lab or work environment.