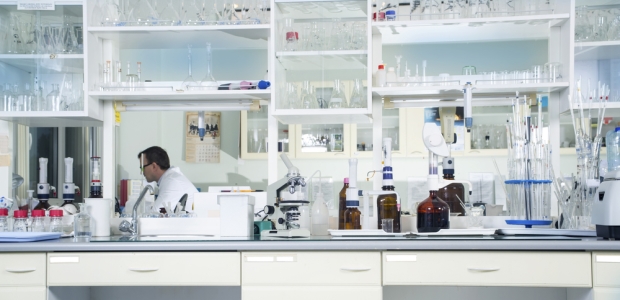
Implementing the OSHA Lab Standard
OSHA recommends basing a lab's control strategies on the hierarchy of controls.
- By Jerry Laws
- Aug 01, 2017
OSHA issued its Occupational Exposure to Hazardous Chemicals in Laboratories standard1 (29 CFR 1910.1450) in 1990. Known as the Laboratory Standard, it was developed to address workplaces where relatively small quantities of hazardous chemicals are used on a non-production basis, according to the agency, which explains that not all laboratories are covered by the standard. Most quality control laboratories are not covered by it.
The standard requires that employers designate a Chemical Hygiene Officer for their laboratories that are covered by it, have a written Chemical Hygiene Plan, and actively verify that it remains effective. The plan must address workers' training, chemical exposure monitoring where that is appropriate, medical consultation when exposure occurs, criteria for the use of PPE, engineering controls, and also special precautions for particularly hazardous substances. The Chemical Hygiene Officer is responsible for implementation of the plan and for monitoring work processes and procuring chemicals; this employee must be qualified to provide technical guidance on plan implementation.
The following two definitions are taken directly from the standard:
Chemical Hygiene Officer means an employee who is designated by the employer, and who is qualified by training or experience, to provide technical guidance in the development and implementation of the provisions of the Chemical Hygiene Plan. This definition is not intended to place limitations on the position description or job classification that the designated individual shall hold within the employer’s organizational structure.
Chemical Hygiene Plan means a written program developed and implemented by the employer which sets forth procedures, equipment, personal protective equipment and work practices that (i) are capable of protecting employees from the health hazards presented by hazardous chemicals used in that particular workplace and (ii) meets the requirements of paragraph (e) of this section.
Control Strategies and PPE
Safety professionals across all industries will be familiar with the hierarchy of controls, upon which OSHA recommends basing a laboratory's control strategies. From most effective to least, it lists engineering controls; administrative controls and work practices; and personal protective equipment, all of which may be used in combination to protect workers. Engineering controls for laboratories may include fume hoods and biological safety cabinets, while administrative controls could include modified work schedules to reduce the duration of potential exposures. PPE options include faceshields and goggles, gloves, respiratory protection, and lab coats.
Key concerns as addressed in the standard are common to laboratories: eye and skin hazards from chemical exposures, respiratory hazards, spills, and leaks. Fire hazards are another potential concern, as are radioactive and musculoskeletal hazards, according to OSHA. Best practices include ensuring that lab workers wear goggles, lab coats, and gloves for protection against chemical splash, are trained and prepared for cleaning up spilled chemicals and broken glass, know where the eyewash and emergency drench shower stations are and also know how to use them properly, and are prohibited from eating or drinking in the lab.
As explained in an OSHA document2 intended for supervisors, principal investigators, and managers who have the primary responsibility for maintaining laboratories under their supervision, the Laboratory Standard consists of five major elements:
- Hazard identification
- Chemical Hygiene Plan
- Information and training
- Exposure monitoring
- Medical consultation and examinations
And this information must be included in each Chemical Hygiene Plan, according to OSHA:
- Standard Operating Procedures (SOPs): These cover prudent practices that must be followed when working with chemicals in a lab, including both general and laboratory-specific procedures for handling hazardous chemicals.
- Criteria for exposure control measures: Criteria the employer uses to determine and implement control measures to reduce exposures to hazardous chemicals are to be addressed, including engineering controls, the use of PPE, and hygiene practices.
- Adequacy and proper functioning of fume hoods and other protective equipment: The plan should detail the measures that must be taken to ensure adequate performance of protective equipment.
- Information and training: The employer must inform and train workers on the hazards of chemicals in their work areas.
- Requirement of prior approval of lab procedures: The circumstances under which certain lab procedures or activities require approval from the employer or employer’s designee before work begins.
- Medical consultations and examinations: It lists details on medical consultation and examination to take place when exposure to a hazardous chemical has or may have taken place.
- Particularly hazardous substances: The plan covers additional worker protections for any work with particularly hazardous substances, such as carcinogens, reproductive toxins, and substances with a high degree of acute toxicity.
Appendix A
Appendix A3 of the Laboratory Standard includes a wealth of information. It covers—for the more than 500,000 workers who work in laboratories in the United States, according to OSHA—everything from a safety culture to ventilation to chemical storage, chemical handling and chemical inventory, waste management, recordkeeping, nanomaterials, compressed gases, highly toxic and explosive or reactive chemicals/materials, and also emergency preparedness and emergency response.
A risk assessment should be conducted before work with any hazardous chemical begins for the first time, and the worker(s) should read all Safety Data Sheet and label information for that chemical beforehand, it says. Trained laboratory workers also should ensure that proper engineering controls, such as ventilation, and PPE are in place. As for chemical inventory, it simply states that "Prudent management of chemicals in any laboratory is greatly facilitated by keeping an accurate inventory of the chemicals stored" and that "Unneeded items should be discarded or returned to the storeroom."
The brief section on transporting chemicals list these three admonitions:
(a) Secondary containment devices should be used when transporting chemicals.
(b) When transporting chemicals outside of the laboratory or between stockrooms and laboratories, the transport container should be break-resistant.
(c) High-traffic areas should be avoided.
Several other OSHA standards also may apply to laboratory operations. These include the Hazard Communication standard, the Bloodborne Pathogens standard, the Personal Protective Equipment standard, the Eye and Face Protection standard, the Hand Protection standard, the Respiratory Protection standard, and even the Control of Hazardous Energy (Lockout/Tagout) standard. OSHA points out in the document that its standards on electrical safety (29 CFR 1910 Subpart S-Electrical); portable fire extinguishers (29 CFR 1910.157); walking-working surfaces also may apply.
This article originally appeared in the August 2017 issue of Occupational Health & Safety.