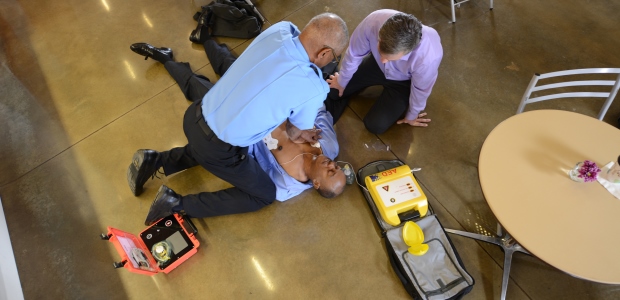
Working Against Time: Nine Steps to Implementing a Successful AED Program
Setting up an AED program takes planning but is not difficult. Here are the key steps to implementing one within the workplace.
- By Jeff A. Woodin
- Jun 01, 2016
Picture this: You're picking a pallet off the loading dock, and suddenly another worker drops to the ground. Would you know what to do?
This scene might seem far-fetched, but it's not. Sudden cardiac arrest is a leading cause of death in the United States, claiming more than 350,000 lives annually. Of these, 70 percent happen at a home and less than 12 percent of EMS-treated adults survive. The Occupational Safety and Health Administration narrows it down further. OSHA reports that 15 percent of workplace fatalities—more than 400 per year—are caused by sudden cardiac arrest. By having an AED available and an average time to defibrillation of five minutes, OSHA estimates that an additional 160 lives could have been saved—a 40 percent increase.
Safety and health experts agree it's not hard. The keys to survival lie in the hands of bystanders who can immediately start CPR and operate an automated external defibrillator (AED). This is buttressed by a study in the journal Resuscitation that showed bystander AED use, coupled with CPR, nearly doubled the number of patients who survived to be discharged from the hospital than just doing CPR alone.
This past March, two Chicago police officers stationed at Midway Airport heard a call for help and raced inside a Harry Caray's restaurant to aid a collapsed man. Officer Michael Ephraim began CPR and, minutes later, Officer Walter Bland relieved him. A third officer, Sherida Shepher, brought an AED from the nearby food court and a fourth officer, John Munoz, attached AED pads to the man's chest. By then, the man's heart was beating, and the device signaled that it did not need to be activated.
Two of the officers, each with nearly three decades on the force, had received CPR and AED training for the first time just three weeks earlier. Midway and O'Hare Airports require that all of their officers complete courses in CPR and AED use taught by a training center using American Heart Association guidelines. In fact, more than 3,000 people who work at these two airports have been trained since 1999. That's lucky for the Midway traveler, who became one of 84 lives saved since the airports began requiring CPR and AED training in 1999.
Setting up an AED program takes planning but is not difficult. Here are the key steps to implementing one within the workplace.
1.Get medical oversight. The U.S. Food and Drug Administration may require a physician’s prescription to purchase an AED. The role of the physician varies depending on the size and other characteristics of the program, but general responsibilities typically include signing off on or making recommendations on training plans, policies, and procedures; evaluating data recorded on an AED during a medical emergency; and helping assess each use of an AED as a way to recommend improvements.
2. Work with local EMS. Every AED program should be integrated with the local EMS system because these will most likely be the first medical professionals on the scene. In fact, most states require this step in addition to reporting follow-up data to the local EMS after any use of the AED.
3. Choose an AED. AEDs are designed to be simple and easy to use, and one being considered for purchase should be approved by the FDA. While we do not recommend one device over another, manufacturers offer AEDs that are suitable for a company's or organization's program.
4. Contact technical support. It's important to ensure that technical support is available when the AED device requires it. Before you decide on a manufacturer and model, call the manufacturer's technical support number to test the response. Is a representative available to help you right away? Are you on hold for a long time? Does your call go to voice mail? Preparation and small details count when a life is at stake.
5. Make sure program support is available. Some AED manufacturers provide help with program implementation, such as placement of the device, medical authorization, registration, and training. Additionally, there are services that will monitor AEDs to ensure that they are well maintained and operational when needed. This includes everything from checking battery life to ensuring that the pads are in good working order. Review your capabilities and determine whether services like these might be an efficient alternative to having a staff member take on this responsibility.
6. Place AEDs in visible and accessible locations. For each minute that defibrillation is delayed, survival decreases by 10 percent. At the 10-minute mark, survival is dismal. Effective AED programs are designed to deliver a shock to a victim within three to five minutes after the person collapses. The three-minute response time can serve as a guideline to determine how many AEDs are needed and in what locations. Chicago's O'Hare and Midway Airports, for example, place AEDs so that anyone can respond within one minute to someone who has experienced cardiac arrest. It's not just in terminals, either. More than 20 AEDs are installed at airport work sites not accessible to the public, such as airport maintenance complexes, remote buildings, and radio facilities.
7. Develop a training plan. Although an AED requires only that the user turn it on and follow the audio instructions when prompted, training increases the comfort and confidence level of responders. It's also part of OSHA’s best practices guidelines for employers. Organizations such as ours offer inclusive first aid/CPR/AED courses in both classroom settings and blended learning formats that mix online and in-classroom training. Programs should also consider refresher training. O'Hare and Midway Airports conduct quarterly drills to maintain proficiency.
8. Raise awareness of the AED program. It should go without saying that once an AED program is implemented, employees ought to know about it. Many employers use internal newsletters, posters, magnets, signage, or other means to promote their AED program and identify where the devices are located. By continually raising awareness of the program, organizations reinforce a commitment to safety among employees.
9. Implement an ongoing maintenance routine. It is important to do regular inspections of the AEDs to ensure they are in working order, accompanied by a written checklist that assesses the readiness of the AEDs and supplies. The manufacturer also will suggest more detailed inspection recommendations that may include software updates or upgrades.
Although officers responded to the emergency at Midway Airport, it easily could have been a baggage handler, a concession operator, or an electrician. Dr. Robert W. Neumar, M.D., Ph.D., who is a professor and chair of the Department of Emergency Medicine for the University of Michigan Health System, points out that AEDs are designed so that bystanders can use them easily and effectively in an emergency. "Make sure your employees aren't scared to use it. In cardiac arrest, every minute counts," Neumar said.
This article originally appeared in the June 2016 issue of Occupational Health & Safety.