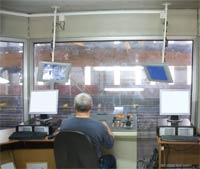
Reviving Your Program
Watch for needless or wasted motion, processes and procedures that can be improved, and equipment being used improperly or in need of upgrade.
- By Stephen V. Magyar, Jr., MBA, CSP
- Jul 01, 2008
The objective of any ergonomics program is to
ensure that work areas and/or jobs that produce
musculoskeletal injuries are identified, evaluated,
and made more “worker friendly.” The procedures
for selecting work areas and/or jobs for review
are not new; however, they are precise and do produce
results—fewer injuries, fewer employee complaints, and
productivity improvements. Employee involvement and
empowerment in the discovery and solution processes
are essential elements to the success of a program.
The initial step in establishing a program is determining
work areas and/or jobs to be targeted for evaluation.
Consider several factors in the selection process:
• Work areas where new equipment and/or modified
procedures are introduced
• Areas where there is poor work flow and/or frequent
congestion or downtime
• Work areas with a history of ergonomic related injuries
(back, wrist, elbow, etc.)
• Repetitive motion jobs (packaging, labeling, computer
applications, and other tasks requiring frequent
repetitive limb motions)
• Work areas where there is frequent property
damage and/or equipment downtime caused by equipment
operators
• Work areas where environmental conditions, such
as light, heat, noise, dust, and more, are contributing to a
lack of productivity and/or injuries
Evaluations should focus on individual jobs or workstations
to ensure all aspects of the work process are considered.
Avoid taking a “big picture look” at the entire
work area, because this often produces no meaningful information.
Give particular attention to “evaporative work
practices” that occur when adjustments to the regular
work routine are necessary. Such adjustments are always
worker initiated as the consequence of a failed procedure.
Without a specific objective, it is impossible to conduct
an effective evaluation.
Work Area Observation
The observation process requires the ability to identify
needless or wasted motion, processes and procedures
that can be improved, tools or other equipment being
used improperly or in need of upgrade, poor or unsafe
work practices, and overall worker attitude. The process
is time consuming because it seeks to draw conclusions
about the causes of ergonomic deficiencies.
Use checklists or other means to assist in tabulating
your findings and developing work profiles. The critical
element is determining why work is being performed in
the manner that you observed. The basic steps in the observation
process should be sequenced as follows:
• Select the work area to be observed.
• Focus on a single job or group of similar jobs being
performed within the work area.
• Take time to observe all aspects of the work being
performed.
• Identify job steps or routines that can be improved.
• Pay specific attention to housekeeping conditions
and to materials and/or equipment that may seem out
of place.
• Discuss findings with the individual worker(s)
without divulging conclusions.
Ask questions and obtain answers; workers should
identify areas where improvements and changes are
needed. Be certain to discuss all out-of-place items, which
are usually at the root cause of evaporative unsafe acts
(i.e., chance taking).
The worker always has a reason for performing his or
her way. Workers are responsible for doing the work, they
are the most susceptible to injury, and their opinions and
ideas are critical to the development of effective ergonomic
solutions. Minor changes such as new hand
tools, proper job instruction, and workstation modification
usually can correct ergonomic problems and reduce
injury exposure. Involving workers in the discovery
process creates ownership and ensures ergonomic
changes will be accepted when implemented.
One on One or Team Approach?
You can accomplish worker involvement one on one immediately
after each observation or through the development
of Ergonomic Review Teams. The value of the
one on one approach is confined to the immediate situation;
teams can be used as a training opportunity that
can sensitize workers to ergonomic issues and create additional
ergonomic “eyes and ears” in the work area.
When the latter alternative is selected, team members
must have full management support. Effective training
must be provided, worker empowerment must be encouraged,
teams must develop and present recommendations
to management, and management must be receptive
to change.
Management must identify areas for evaluation before
teams are chosen. Use the previously outlined methods
for selection and review job descriptions, injury
records and trends, worker’s comp costs, absentee rates,
and other pertinent criteria. It may help to consult with
your insurance provider. Develop a formal training agenda
with specific objectives.
A typical training agenda might include critical discussions
and methods for evaluating the following
work issues:
General work flow and congestion: Can the flow be
improved?
Hand tools: Are they adequate? Are workers properly
trained in their use?
Work procedures: Do they force workers into “evaporative
acts”?
Man/machine relationships: Are work adjustments
made to accommodate machinery? Do workers have the
ability to control their work routine?
Repetitive motion tasks: Are all steps required to
complete the work?
Materials being used: Are all materials needed? Are
they safe?
Environmental controls: Is the work area too noisy?
Too hot? Is the lighting adequate?
Obviously, there are many additional considerations.
They should always be related to the work areas targeted
for evaluation.
Review Teams Procedures
Training sessions should be sufficient in duration
(usually, 60 minutes) to allow for active discussion
from all team members. The team leader should be a
management member, and discussions should be limited
to the session’s subject. Consider using insurance
providers, equipment sales personnel, and subject experts
for these sessions. Encourage workers to participate
and to provide opinions and recommendations.
The team leader should document all suggestions.
Choose team members based on the work areas for
evaluation; the most vocal (pro or con), most knowledgeable,
most popular, or any other criterion should be
considered for inclusion. Team members must be advised
of the team’s purpose, the training schedule, all objectives
and requirements, and their eventual role in the
ergonomic evaluation process. The process of determining
what is best in the workplace is difficult to accomplish
without meaningful worker involvement and a strong
management commitment to the team’s purpose: developing
“ergonomically sensitive workers” who can identify
ineffective man/machine and process/procedure mismatches;
establishing communication opportunities that
encourage frequent discussion of ergonomic issues with
supervisors; and allowing meaningful suggestions to be
made that will prevent downtime, material damage,
and/or injury before the incidents occur.
Periodic progress reports must be made so team
members are aware of ergonomic changes resulting from
their recommendations. Using work area managers during
discussion periods is most helpful. Have a team
member present recommendations that require significant
capital investment or workstation modifications to
management during the final session and outline specific
details of the impact of ergonomic improvements on
productivity and anticipated costs. Management support
functions (purchasing, engineering, production planning,
etc.) should help in developing the presentation,
but team members must take the lead in preparing and
presenting final conclusions to management for approval.
Participants must also believe management will
follow through on proposed recommendations.
The training concludes when the final report is made.
Team members must be advised on a scheduled basis of
progress in implementing their recommendations to ensure
their continued interest. To maintain workers’ focus
and motivation, encourage new ideas and establish and
monitor revised work standards.
There should always be an open door policy for reporting
ergonomic suggestions when the training concludes
and the team is disbanded. Additional teams
should be developed as needed to evaluate work
flow/workstation design and to ensure the continued development
of an ergonomically sensitive workforce.
Finally, always remember that ergonomics is best
practiced when workers understand and participate in
the development of objectives and when management is
responsive to recommendations.
This article originally appeared in the July 2008 issue of Occupational Health & Safety.