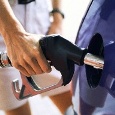
Functionality At Your Fingertips
Today's gas detectors still detect dangerous environments, but their IH features are something to behold.
- By Bill Smith
- Sep 11, 2007
IN the world of gas detection, one fact stands out above all else: Gas monitors are made to protect and preserve your life. And while serving as a life-saving device, they can be considered a multi-purpose tool in many other ways, as well. For example, they can be used to monitor a confined space prior to entry to ensure the area is safe for anyone entering the space. They can be used to discover gas leaks in processes and plant operations. They can be used to measure the explosive nature in an area or enclosed space. Or they can be used to detect unexpected, invisible gases in atmospheres that are not consistently monitored.
From single and multi-gas portable detectors carried or worn by workers to elaborate fixed gas monitors mounted in potentially dangerous atmospheres, the devices have a vast number of uses. Gas monitors are used by a multitude of workers, such as manufacturing operators, refinery personnel, miners, first responders, law enforcement, health and safety professionals, industrial hygienists, and many others.
The general understanding of the function of a gas monitor by a non-professional is that it is used to warn personnel of potentially dangerous situations, such as exposure to harmful gas or oxygen-deficient or enriched environments. There also numerous toxic and flammable gases that most monitors can protect against--gases such as carbon monoxide, hydrogen sulfide, ammonia, and chlorine dioxide, just to name a few.
The harmful gases may be the result of off-gassing in a manufacturing process, the build-up of carbon monoxide as a result of incomplete machine combustion, or even the displacement of oxygen created by harmful gases created in any gas-producing process.
Perhaps one of the most important features of a gas monitor, however, is its industrial hygiene capability. Again, the layman might think the gas monitor is utilized primarily for general safety purposes; while general safety is covered with the proper use of a monitor by trained personnel, monitors with the industrial hygiene features go beyond general safety.
Industrial hygiene as defined by OSHA in its "Informational Booklet on Industrial Hygiene" as the science of anticipating, recognizing, evaluating, and controlling workplace conditions that may cause workers' injury or illness. The injuries and illnesses can include, but are not limited to, poisoning from toxic gases, burns or internal organ damage as a result of undetected and ignited flammable gas explosions, or even death.
How does a gas monitor protect from illness or death? The most obvious answer to this question is simple. When referring to the OSHA definition, a properly used monitor that simply recognizes the hazard speaks for itself. If you know the hazard is present, you can evacuate the area and take precautions to eliminate the hazard. However, utilizing sensor technology such as catalytic diffusion sensors, electrochemical, and photoionization or infrared sensors, gas monitors can not only seek out potentially dangerous environments, but also provide valuable information to document your events or the times of atmospheric contamination when used for hygiene purposes.
Furthermore, the digital readout technology on today's gas monitors allows the user of the monitor to distinguish the hazard, detectable to the parts per million (ppm) level, and warns the user the environment is unsafe, allowing the user to stay within the OSHA-recommended guidelines for gas exposure.
Detection of a dangerous environment and understanding of the dangers present are key elements to allowing the gas monitor's user to stay safe and take measures to purge the atmosphere to ensure the danger is gone.
How do the IH functions of a gas monitor take the monitoring of your work atmosphere and the protection of the monitor's user to even greater heights? Let's look at some key industrial hygiene features of gas monitors.
Datalogging
Many of today's monitors come equipped with a datalogger, which is a device containing a microprocessor that gathers and stores pertinent atmospheric and time-based information that is electronically extrapolated from a hygiene-equipped instrument. Once collected and filed on a microchip, the instrument can be connected to a computer or other printing device for later reference and printouts.
What type of information do dataloggers track to ensure proper hygiene in a workspace? Two of most important bits of information recorded in a datalogger relating specifically to hygiene are STELs and TWAs.
Short Term Exposure Limit (STEL)
STEL is the average of a gas concentration that a worker has been exposed to during a specified time period. If this exposure exceeds the predetermined limits, the worker must remove him or herself from the hazard for a period of at least one hour before re-entry. STEL values may be exceeded only four times during a normal work shift of eight hours.
Time Weighted Average (TWA)
TWA is the average amount of gas a worker has been exposed to during a specified time period. This time is usually defined as eight hours to represent a normal work day. If a predetermined TWA value is exceeded, a worker may not re-enter the space for the balance of the work day.
STELs and TWAs are calculated by the datalogger's microprocessor and follow strict guidelines established by the American Conference of Governmental Industrial Hygienists. These guidelines list the maximum concentration of a substance to which a worker may be exposed without ill affects during a normal eight-hour, five-day week. Dataloggers allow you to monitor and know the STEL and TWA readings, which ensures good IH practices.
Also captured with datalogging capable gas monitors are individual gas readings. Having these readings documented and filed can play an important role in better understanding the hazards present in a particular process or work area. The documentation also serves as a trail of exposure in case you have an accident.
Datalogger-equipped monitors also can document the user identification and site identification of a particular monitor. This ensures proper documentation of the "who" and "where" of the monitor's use.
Maintenance Management Made Easy
Maintenance of your gas monitor, or calibration/bump testing, is an important part of using your monitor for hygiene purposes. OSHA mandates in 29 CFR 1910.146 (the permit-required confined space standard) that the only way to safely detect a hazardous atmosphere is with a "Calibrated direct reading instrument."
Docking systems or stations for gas detector maintenance often provide single-button calibration options to help users meet the OSHA requirements. Workers no longer have to calibrate their monitors manually, saving time and taking the human error element out of the equation.
Docking systems can automatically record and store the valuable bump and calibration records, thus keeping a record of all hygiene information recorded. Datalogging information is logged and stored through the event logging mode, and the information is recorded when a gas incident or event occurs.
The use of a docking system ensures that your monitor is properly charged when not in use. Keeping the monitor fully charged means it will work the next time it is needed and virtually eliminates downtime from insufficiently charged monitors.
Automation and technology built into docking systems also provides a means for diagnosing potential problems with your monitor, such as low or marginal sensor life, date of the last calibration, and the number of days until the next calibration is due. This allows you to be prepared to replace a failing sensor and to know when you need to calibrate your instrument to be certain it is operating at peak performance.
Using Centralized Databases
Another advancement in the IH functionality of gas monitors involves the use of docking systems and two-way wireless and/or Ethernet connectivity to link up to 100 stand-alone instrument docking stations from remote locations anywhere in a facility. This allows information from each station or site to be relayed back to one central database, allowing for total, centralized, instrument management.
From the centralized location, all pertinent hygiene information can be viewed, analyzed, and responded to, allowing more time for personnel to focus on their core business objectives rather than gas monitor maintenance. Some manufacturers of monitors will analyze the data for you and can issue reports on the health of your monitor or fleet of monitors, allowing even more time to focus on your business and not your monitor program.
As you can see, gas monitors used with IH capability can afford you more than just general protection from unseen gas hazards. They can save your life and help you to gain a formidable understanding of your processes and problems while providing the valuable information you need to mitigate problems.
This article originally appeared in the September 2007 issue of Occupational Health & Safety.