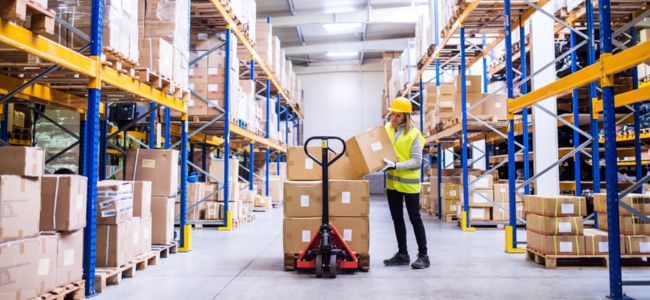
Safety Measures in Warehouses and Fulfillment Centers
Let’s look at a few best practices for protecting workers.
- By Will Schneider
- Jun 26, 2023
In the bustling hubs of logistics and supply chains—warehouses and fulfillment centers—maintaining worker safety is an unequivocal priority. While navigating the labyrinthine aisles stacked with goods, maneuvering heavy machinery and meeting the relentless demands of a round-the-clock industry, workers operate in environments rife with potential hazards.
Consequently, implementing effective safety measures is not just a regulatory necessity, but a moral imperative for these organizations. According to the U.S. Bureau of Labor Statistics, employers reported 2.6 million workplace injuries in 2021. The majority of those were in:
- health care and social assistance
- retail trade
- manufacturing
- transportation and warehousing.
This article aims to delve into the innovative strategies and best practices being adopted across the industry to protect its invaluable human assets, all while ensuring operational efficiency and productivity.
The Role of Technology in Safety Training
Technology has become a crucial aspect of safety training for workers, particularly in warehouses and fulfillment centers. With the rapid advancement of technology, virtual reality (VR) and augmented reality (AR) have emerged as powerful tools to transform traditional training methods.
By submerging workers in simulated dangerous scenarios, and teaching them how to handle these, the technologies provide a safe and controlled environment for learning the essential safety protocols.
This practical, hands-on approach enhances retention and ensures workers are better prepared for real-world scenarios. For instance, a leading logistics company successfully implemented VR technology for safety training. The results showed a 100 percent reduction in lost time due to injury, a 32 percent reduction in reported near misses and higher incident reporting rates, which means they understood how to report incidents.
The Importance of Data-Driven Risk Assessment
Following technology-driven safety training, next up is predictive analytics, a game-changer in proactively assessing and managing safety risks. In the era of big data, reactive measures are simply not enough. Forward-thinking organizations are leveraging predictive analytics to identify potential safety risks before they become tangible hazards.
This data-driven approach involves analyzing vast pools of data, ranging from historical incident reports and near-miss data to workers' behavioral patterns related to safety practices. The results have been notable. For instance, Amazon showcased a plan to cut worker injuries by 50 percent by 2025. They declared they plan to invest $300 million in worker safety — which shows how much companies can save by investing in workplace safety.
Some of the technologies that Amazon Executive Chairman and Founder Jeff Bezos announced were algorithms that can rotate employees through jobs and sensors that can measure risk exposure to MSDs.
The Significance of Mental Health in Worker Safety
With the constant growth of e-commerce and the increasing demand for efficient supply chain management, warehousing and fulfillment operations are becoming crucial for businesses across various industries. In fact, projections indicate that the logistic market is expected to experience a compound annual growth rate (CAGR) of 11.0 percent from 2022 to 2030, highlighting the significant role this industry plays in global trade.
As more companies recognize the benefits of outsourcing their storage, distribution and other logistic management needs, the pressure on warehouse logistics companies and fulfillment centers continues to rise.
This trend amplifies the already intense nature of these environments, necessitating a greater focus on the mental well-being of the workforce. Amidst the fast-paced nature of the industry and the mounting demands, it is imperative that we address the mental health aspects as an integral part of overall worker safety.
The strain these environments can place on mental health is real. Employees juggle physical demands alongside intricate tasks requiring precision and alertness. Add in the fluctuating shifts, and it's clear how stress and fatigue may sneak in—posing considerable threats to safety. Mistakes in such settings can lead to severe accidents, and these mistakes can often be traced back to stress and fatigue.
Moreover, the effects of stress on safety aren't just direct, like a distracted worker causing an accident. They're also indirect, affecting morale and focus, making employees less engaged, more prone to overlook safety protocols or more likely to miss potential hazards.
So, let's shed light on this: mental health isn't a separate issue; it's woven into the fabric of overall worker safety. Our challenge is to recognize this and prioritize mental well-being alongside physical safety measures. In doing so, we'll be tackling worker safety from a more holistic and effective perspective.
How Mental Health Resources Contribute to Safety
Given the clear link between mental health and safety, progressive organizations are taking strides to mitigate stressors and provide support for employees' mental well-being. Employee Assistance Programs (EAPs), on-site counselors and wellness initiatives are becoming increasingly common resources within these settings.
EAPs, for example, provide services such as counseling, legal advice and financial planning, helping employees navigate personal challenges that could adversely impact their mental health. Similarly, on-site counselors can provide immediate psychological support, while wellness initiatives can promote healthier lifestyles.
It's worth noting that businesses offering mental health support systems tend to experience a reduction in injury rates. This underscores the significance of caring for the mental health of workers as part of ensuring a safe and healthy work environment.
A study published by BMC Public Health showed that there is a big correlation between work-related stress and sick leave. The study found that high work-related stress quadrupled the chances of getting sick leave.
The takeaway? Companies that incorporate health promotion programs may see a reduction in sick leave, workers' comp claims and disability management. Mental health resources play a big role in enhancing the safety and well-being of those in warehouse and fulfillment center jobs.
Cultivating a Safety Culture
As we've established the significance of mental health resources, it's essential to understand that their effective implementation is intrinsically linked with cultivating a robust safety culture. This culture is characterized by shared values, practices and behaviors that prioritize safety.
A strong safety culture is pivotal in any organization's safety framework, including warehouses and fulfillment centers. It ensures safety measures are not just transactional checklists but are ingrained in everyday behavior. It promotes transparency, encourages reporting safety incidents and near-misses and fosters a learning environment rather than a blame culture.
In such environments, safety is not just seen as a management responsibility but as a shared responsibility of all employees. German company TÜV Rheinland managed to achieve an average accident reduction of up to 50 percent through their sustainable safety culture. Thus, cultivating a strong safety culture can also have a profound impact on maintaining high safety standards in warehouses and fulfillment centers.
The Role of Workspace Design in Safety
While the role of culture and behavior is undeniable, the physical design of the workspace also plays a crucial part in safeguarding the workforce in warehouses and fulfillment centers. A well-designed workspace can not only boost productivity but also significantly reduce the risk of accidents.
Factors such as:
- adequate lighting
- clear marking of paths
- and appropriate placement of storage units
can help prevent common incidents like slips, trips and falls.
Additionally, adequate spacing between workstations can help minimize collisions or accidents related to moving equipment.
The National Institute for Occupational Safety and Health, as a part of their national initiative called Prevention through Design, recommends the prevention of occupational illnesses via carefully planned workspace design.
The outlined goals can be achieved through the following approaches:
- Eliminating hazards and managing risks for workers at the source or as early as possible
- Incorporating design, redesign and retrofitting practices for both new and existing work premises, structures, tools, facilities, equipment, machinery, products, substances, work processes and work organization
- Improving the work environment by integrating preventive methods into all designs that have an impact on workers and others present on the premises.
Ergonomics: An Essential Aspect of Safety
The concept of ergonomics has become a cornerstone in the realm of workplace safety. It involves tailoring the design of the work environment to align with the capabilities and limitations of the workers, optimizing both worker well-being and overall performance.
In the context of warehouses and fulfillment centers, ergonomics might involve appropriate lifting techniques, adjustable workstations, the use of assistive devices and scheduled breaks to reduce repetitive strain.
According to OSHA, the implementation of an effective ergonomics program can help prevent musculoskeletal disorders, such as carpal tunnel syndrome or back injuries, which are a leading cause of workdays lost due to injury and illness.
This approach to safety underlines the idea that rather than expecting workers to adapt to a static work environment, the work environment should be adapted to meet the needs of workers. The commitment to an ergonomic workplace not only enhances worker safety but also contributes to higher morale, reduced absenteeism and increased productivity.
The Need for Continuous Improvement in Safety Measures
Building on established safety measures, it is crucial to recognize the necessity for continuous improvement. The ever-evolving landscape of technology, regulations and best practices demands safety protocols that are not stagnant.
Regular safety audits are fundamental to this process, ensuring that all measures remain effective and relevant. These audits help identify potential hazards and prevent accidents before they occur. They also provide an opportunity to reassess risk and make the necessary adjustments to the safety plan.
Moreover, staying abreast with advancements in safety technologies and techniques can further enhance safety standards. For example, advancements in wearable technology can now monitor a worker's vital signs and environmental conditions in real time, providing valuable data that can be used to further improve safety protocols.
Finally, encouraging open conversations about safety can contribute significantly to continuous improvement. Workers, being on the front lines, can provide valuable insights and ideas for improving safety measures. By fostering an environment where workers feel comfortable voicing their concerns and suggestions, organizations can tap into this wealth of firsthand knowledge to make their workplaces safer.
Wrapping up
Understanding safety in the context of warehousing and fulfillment is crucial for organizations. It should be viewed as an opportunity for progress rather than just a compliance requirement. The future holds great potential for innovative solutions that can revolutionize safety measures in warehouses and fulfillment centers.
Advancements such as AI-powered safety systems and predictive maintenance have the ability to significantly enhance the safety standards in these environments.
In addition to technological advancements, it is essential for organizations to place a strong emphasis on safety. Doing so cultivates a sense of mutual respect between the organization and its workers, leading to increased productivity and loyalty.
To summarize, safety in warehousing and fulfillment goes beyond mere prevention of harm. It encompasses multiple dimensions aimed at creating a healthier and more productive workspace. As we continue to progress, it is imperative that we all actively contribute to this safety revolution in our respective roles.