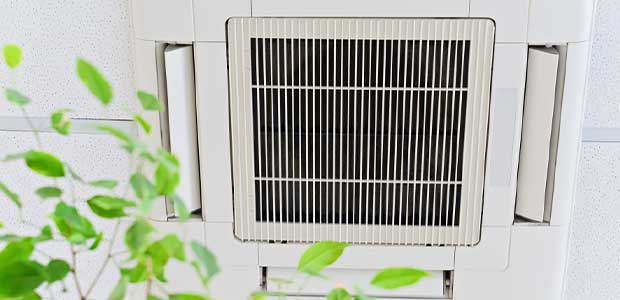
Page 2 of 3
Why Differential Air Pressure Monitoring is Critical to Employee Safety
What’s that smell? From procedures as complicated as those involved in electrolysis to more commonly understood tasks like coffee roasting, many industrial processes create byproducts that we do not necessarily want escaping into the air we all breathe.
Sure, roasting coffee has an enticing aroma—especially when you’re waking up in the morning—but most other manufacturing processes involving chemical, physical, electrical or mechanical changes do not emit such pleasant odors. And worse yet, many of these processes result in pollutants much more harmful than a whiff of espresso.
Consider coffee roasting as an example. When roasting coffee, chaff—the papery-thin skin of the coffee bean—falls off. In industrial roasting plants, special filters collect chaff and other pollutants, helping ensure they do not penetrate the air outside the facility. Consequently, these filters must be cleaned periodically for maximum efficiency. But what if the filter had a hole or tear, allowing chaff and other pollutants to escape?
Enter differential air pressure monitoring. Ideal for monitoring HVAC filters, exhaust blowers and clean rooms, differential pressure sensors help ensure optimal indoor conditions, improve energy efficiency and protect human health and well-being. Throughout the rest of this article, we’ll delve into what differential air pressure is and why it’s important, highlighting critical applications for differential air pressure sensors.
What is Differential Air Pressure?
Air pressure is the weight of air molecules, with cool molecules being heavier and denser than warm air molecules. But measuring how the air presses down onto the earth or other objects can be incredibly difficult. Consider checking the air pressure of your car’s tires. A tire gauge will inform you that the pressure is a certain number of pounds per square inch, but what does that mean? Basic air pressure measures the difference between the atmospheric pressure outside the tire and the air pressure inside the tire.
On the other hand, differential air pressure measures the difference between two points on independent systems or between two different points on the same system. For example, the outside and the inside of the previously mentioned coffee roasting plant’s baghouse filter, across a filter in an HVAC system or in the entrance to a clean room. Essentially the difference in pressure between two given points, differential air pressure is more complex than basic air pressure since the reading and reference values are variable.
Differential pressure is calculated by subtracting either the reading or reference value from the other. Very small differential pressure is measured in inches of water (shortened to inH2O), with 1 inH20 equal to .036 psi. Despite being commonly misunderstood and somewhat more complicated than other pressure measurements, differential pressure monitoring is vital to ensuring employee safety in industrial environments across a myriad of applications.
Wireless Differential Pressure Sensor Use Cases
Whenever decision-makers need to know quickly about slight changes in pressure comparisons that impact an employee’s health and well-being, the ability to monitor the differential pressure continuously between two environments is essential. Plus, unlike traditional pressure gauges, wireless monitors do not require manual readings and recordings, nor are they as expensive and inconvenient as digital pressure transmitters that require electrical wiring.
In addition to continuous monitoring, modern differential pressure monitors can alert maintenance staff of any issues via phone, text or email, empowering advanced maintenance and necessary repair planning that minimizes downtime and keeps your people out of harm’s way. So much more than just pressure measuring, differential pressure measurement can be utilized across industries that monitor filter conditions, positive-pressure rooms, and proper exhaust pressure and much more.
Industrial HVAC Systems. With price tags of $1,000-plus, industrial HVAC filters are expensive. And when a dozen or more such filters are located throughout the typical factory, changing one too soon or too late can impact the bottom line. Changing one based on scheduled maintenance before its end of life is a poor economic decision. Change the filter too late, however, and the system could operate inefficiently, driving up energy costs and possibly spewing dangerous emissions into the workplace or environment.
By monitoring the air pressure on each side of an HVAC filter, a differential air pressure sensor can help detect two different issues. First, by measuring the differential air pressure, the sensor can help determine whether the filter is clogged and needs to be changed. A wireless HVAC differential pressure sensor can alert to a special event, such as excess dust in the plant due to construction, that can clog a filter earlier than expected. Second, if the difference between the measurements on each side of the filter is lower than expected, that could indicate a possible tear or hole in the filter.
Differential air pressure sensors can also monitor exhaust vents, which is especially important in industries like pharmaceuticals, biotech, wafer fabrication and others where a faulty clean room can expose employees to danger and cause expensive product loss.
Clean Rooms and Data Centers. Efficient, accurate monitoring of HVAC systems is also critically important in data centers. Servers generate significant amounts of heat that can lead to overheating, ultimately resulting in unplanned downtime and possible data loss.
Wireless differential pressure sensors also compare the pressure inside and out of clean room environments in a continuous manner to help keep contaminants out and harmful compounds from invading the rest of the workspace.
With continuous wireless monitoring, maintenance operations managers can schedule data center filter replacement at the optimal time, maintain compliance with regulations and protect employees working in and around clean rooms from harmful particles.
Other General Differential Pressure Measurement Applications.
- Filter monitoring in oil filter, gas turbine and water/wastewater applications.
- Heat exchanger efficiency.
- Liquid level measurement in sealed tanks undergoing potential liquid and gas phase changes.
- Torque output of hydraulic motors.
Today’s most advanced differential pressure sensors are easy to install, augment with any other necessary industrial sensors and operate. Leveraging differential pressure monitoring has several important applications across industries, and choosing the right differential pressure monitoring system signals to your employees that you’ve prioritized their safety above all else. Regardless of its application and the sector in which your organization operates, differential air pressure monitoring should be used to ensure you are providing safe, controlled, comfortable environments that are conducive to employee productivity and essential for the health and well-being of your most important asset—your people.