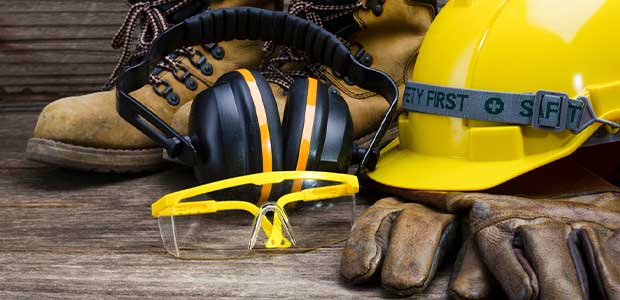
Page 2 of 4
Managing Safety Performance
Introduction
Typically, the annual safety performance records kept by construction companies may include the number of accidents and possibly related information, safety training provided over that period of time, possibly inspection related information and maybe a few others. These may be evaluated, reported and form the basis for improvement interventions for the upcoming year. The problem with this approach is that the data is historical and construction projects are somewhat different from one another, as well as they progressively change, conditions vary, tasks, workers and subcontractors may be different going forward.
The interventions devised based on historical information may not be quite on target for future, somewhat different conditions. More importantly they do not provide pertinent data that can be applied just-in-time to correct situations immediately. In 1992, Kaplan and Norton introduced the balance scorecard as a more effective way to measure and manage organizational performance. Before that, only financial metrics were used and did not provide key information to effectively address some of the underlying operational issues. The balanced scorecard measured performance in four key areas:
1. The customer perspective
2. The internal business process perspective
3. The innovation and learning perspective
4. The financial perspective
Many of the fortune 1000 companies have adopted some form of scorecard with a number of different areas (perspectives) to reflect their specific needs. It seems that this may be a more effective means for managing safety performance, as well, especially for construction organizations.
Devising a Safety Scorecard
So, how do we apply the balanced scorecard technique—or for that matter any other scorecard—to safety? If the business has implemented an organizational scorecard process, then it would make sense for the safety perspectives to be aligned with that. If not, then safety must have its own unique scorecard. Using the balanced score card as a model for an effective safety management tool:
1. The stakeholder in safe work performance—This may primarily include the project owner, the company’s various levels of management as well as the workers, and peripherally, possibly subcontracts, designers and any others that may be relevant to that particular situation, organization or project. We will address this from the workforce perspective and note its effect on the organization, as well as potentially the project owner.
2. Safety process and procedure—Everything that is done to make safety "work": planning, organizing, directing, controlling, programs, training, audits, employee management, relevant risks, etc.
3. Innovation in safety—Technological innovation, people skill and knowledge improvement, system alignment, etc.
4. Safety performance management—Operational excellence, leadership, empowerment, performance standards, performance measurement, innovative solutions, etc.
Now, how do we go about accomplishing this? For example, assume that the vision we have for our safety effort is "an injury-free workplace." The next step is to identify strategies, objectives, measures and targets for each of the above perspectives. The organizational scorecard places vision and strategy at the center. This process establishes goals that ensure everyone within the organization will adopt behaviors and take the actions that will achieve these goals. A measurement system is also designed to ensure this occurs and provides an assessment of how everyone is doing in accomplishing the core vision. Senior management now has a process that effectively focuses all the efforts of the organization toward the vision and has the information with which to manage it effectively.
A Holistic Metrics Approach
Excellence in safety can only be achieved through a strategy-driven, performance-based safety management process. The challenge is how to devise a safety process that will enable the organization to impact performance holistically in order to achieve excellence. Safety should be fully integrated into the organization's operations and outcomes should be aligned with business goals. As a result, the safety process will become integrated into the very fabric of the organization.
1. Stakeholder Focus (two elements)
The primary operational element involves values, vision and strategies which must be focused on garnering stakeholder satisfaction through meeting and/or exceeding their expectations. This must be effectively inculcated in all organization employees and partners. This is in order to create a productive and safe operation which results in a well-planned and smooth work flow, meets and/or exceed schedule and quality requirements. This will result in a safe and engaged workforce, meet owner expectation by creating value, delivering on promises thereby fostering everyone’s satisfaction.
The basic supporting element is the organizational climate and culture which enables and helps sustain the operational element above. But in reality, the best laid plans are susceptible to challenges, delays or unforeseen problems, which may threaten meeting schedule (production) goals. Therefore, to meet expectations, workarounds or deviations from accepted practices may be implemented which may increase the risk of putting work in place with deficient quality or increase the potential for worker injury.
If this is achieved with no negative or unacceptable consequences, such a deviation may be tried again to deal with the next problem, ultimately leading to normalization of deviations with the workaround becoming the accepted work practice. This is an unacceptable outcome. To avoid this, the leadership must create a climate which is on the lookout for this and refocuses operations as well as employees to acceptable processes, procedures and practices going forward.
2. Safety Processes and Procedures (three elements)
The first element is an effective safety program whereby all the safety standards are implemented and adhered to. The program should sound like engineering practices, enabling integrated systems, state-of-the-art education, innovative metrics and audits that will be conducted to ensure that policies and procedures are diligently followed.
The second element requires that specialized safety programs elements be written to address the unique requirements of the business and/or the project. These might include a substance abuse program, an automobile fleet program, a wellness program, advanced technology, innovative practices, etc.
The third element of this cornerstone is risk assessment and pre-operational planning. This is by far the most important element in this cornerstone. The identification of risk and the planning of the operations to effectively deal with the associated risk is a critical activity that all levels of management should engage in.
3. Safety performance management (four elements)
The first is resource management. This means the organization must provide the necessary resources, technology and time required to educate, mentor and protect its employees.
The second element is managing performance. This includes such things as goals and objectives, setting performance measurement standards, establishing accountability, open communication, an empathic work climate, etc.
The third element is measurement. This area deals with how performance is measured and what targets it should be compared to. There are a number of measures the organization can use. These include input, output, process, progress and outcome measures. Input, progress and process measures are predictive and provide information with which to affect change and improvement. Outcome and output measures are historical and indicate results.
The fourth element is about contingent plans and change management. There are typical situations that are more likely to occur. If contingent plans are prepared in advance, then corrections may be able to be immediately implemented post haste. A change implementation process may also be developed to make corrections even more quickly rolled out with minimum disruptions thereby avoiding the acceptance of additional unanticipated risk into operations.
4. Innovation in safety (three elements)
The first deals with the organizational systems and business processes and procedures. This element analyzes the systems to identify barriers, pinch-points and anything that will foster inefficiency or drive unwanted behavior. This element also strives for continuous improvement.
The second element is behavioral interventions. This element looks at the behavior and work practices of individuals and tries to identify the underlying drivers of them, through system change or consequence management this element tries to improve organizational behavior.
The third element is innovation and learning. Change is the only constant in business today. Therefore, for the organizations to thrive, it must become a learning organization. It must identify changes in the environment and react to those changes quickly as well as effectively.
Conclusion
In reviewing the 12 elements, one sees that only one cornerstone with a couple of elements really relates to the traditional safety management area. The rest relates to the way the organization is structured and goes about doing business. The only way to truly manage the risk of incidents, injuries and losses involving the company's workforce requires an analysis of the operational means and methods, the planning and systems, with an innovative scorecard as well as the employees’ behaviors and leaderships’ actions within the organization.