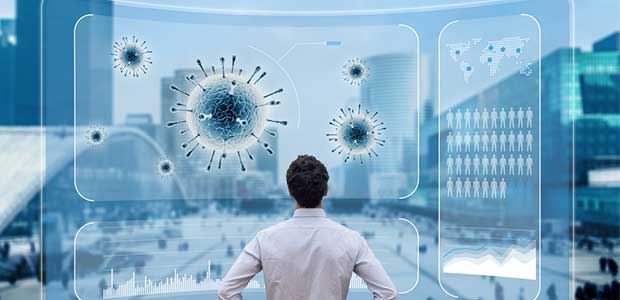
Breaking Down the Silos to Simplify Industrial Hygiene During COVID-19 and Beyond
OHS practitioners must expand their knowledge and programs to account for industrial hygiene.
Occupational health and safety professionals have been forced to do more with less long before the COVID-19 global pandemic. Corporate investment support for traditional industrial hygiene (IH) programs has steadily declined, resulting in many complex IH responsibilities being adapted by technicians and EHS generalists, outsourced to costly consultants or—worst of all—left unmet entirely. Realistically, this trend does not appear to be going away anytime soon; due to COVID-19, many companies have needed to lay off or furlough workers and share job responsibilities across disciplines in order to survive.
Now, more than ever, as an OHS practitioner you must expand your knowledge and skills to be able to manage programs outside of your normal silo to include IH. Fortunately, the growth of smarter EHS software solutions, which is aimed at empowering employees at all levels to improve workplace safety, has made it easier for you to take on more complex tasks.
Let’s take a closer look at how software breaks down the silos to help you run a more effective and efficient IH program now and well into the future.
Simplifying Complex IH Tasks for Non-IH Professionals
During the recent virtual conference, 57 percent of the attendees polled reported having no on-staff IH professionals employed within their companies. These findings fit in with a larger industry trend towards a dwindling number of in-house IH professions and IH programs lacking the resources necessary to properly manage all the requisite IH tasks.
Among the biggest benefits of EHS software is that it makes IH management tasks easier for employees at all levels. Today’s best of breed cloud-based programs make it easy to follow industry best practices, capture data, facilitate the flow of information and provide real-time visibility and reporting into occupational activities.
One way software does this is by simplifying the formation of similar exposure groups (SEGs). Assessing exposures and identifying hazards for individual employees is not practical. A better method is to group those with similar exposures based on location, job and tasks into SEGs. Once defined, you can then identify which SEGs require medical surveillance, qualitative exposure assessments and additional air sampling. Advanced software programs simplify this process by helping to identify SEGs and perform qualitative exposure assessments that meet your unique IH program needs. They also make it easier to keep historical tracking of each employee’s inclusion in SEGs in order to document exposure histories that help support medical or legal inquiries.
Maintaining a Chemical Inventory and IH Sampling Plan
Now, more than ever, it is critical to keep a current inventory of what chemicals you have in your workplace. One significant impact of COVID-19 is an urgent need for the more frequent use of disinfectants to clean potentially contaminated surfaces to limit the spread of the SARS CoV-2 virus. As a result, workplaces have experienced an influx of new cleaning chemicals into their existing inventories.
Knowing what chemicals you already have in your workplace and visibility of any new chemicals entering your facility helps ensure you have all necessary safety data sheets (SDSs), effectively manage workplace labels, train your employees on chemical hazards and meet your regulatory responsibilities.
Having a complete and current chemical inventory list with exposure assessments is also a required when developing your IH sampling plan and will be important to inspectors as well. During compliance inspections, it is common for regulatory compliance officers to ask which chemicals have been recently added to your inventory and whether an exposure assessment has been conducted. While qualitative assessments can reduce the number of samples, they are still needed to document the potential exposure risk and show compliance with the regulations.
As new chemicals arrive, review the information in their SDSs to identify all ingredients that may pose exposure hazards and their relevant occupational exposure limits (OELs) in your IH plan. It is important to not only consider sampling for 8-hour time-weighted average exposures, but also for extended shifts (10 or 12-hour shifts), short-term exposure limits (STELs) and immediately dangerous to life and health (IDLH) concentrations.
How this information is incorporated into your IH sampling plan will depend on your operations and available resources. Most begin full-shift exposures assessed against the 8-hour OELs. Later, you can assess tasks with periodic aspects to them, like cleaning out a tank or adding chemical ingredients to a mixture when concentrations can temporarily spike.
Once you have established a baseline of samples, you can adjust the IH sampling plan accordingly. You may determine you do not have sufficient data to make accurate determination of the risk, or you may decide there is sufficient data and reduce the number of samples required.
A good IH software solution assists with many of the mundane tasks associated with building your IH sampling plan by giving you a simple platform for selecting chemicals from your chemical inventory to be sampled, identifying correct analytical methods and even helping choose the right laboratories for the job. Cloud-based solutions benefit users the most by making information accessible to all those who need access to it, including corporate EHS representatives, consultants and laboratory personnel. This helps streamline the hand-off of responsibilities from one stakeholder to the other, minimizes errors and saves both time and effort throughout the overall process.
Improved Employee Reporting Requirements
Once you have your IH sampling results, you need to share the results with employees. Specific standards require employers to automatically notify affected employees of monitoring results. For instance, you must notify your employees of their methylene chloride exposures within 15 working days of receiving results. The OSHA Standard “Access to Employee Exposure and Medical Records” in 1910.1020 requires you to provide access to exposure records within 15 days of an employee request. If this cannot be done, you must inform the employee of the reason for the delay and the earliest day when the records will be available.
Software helps streamline these notification requirements by allowing you to track and maintain your results in one centralized location. Most solutions today will flag results that exceed the applicable OEL to make it easier to prioritize and automate communications and know when follow-on activities are needed.
Preparing for the Unexpected
COVID-19 has created unprecedented demand for respirators, especially N95 filtering facepiece respirators (FFRs), which are among the preferred models for reducing risk of exposure since they remove approximately 95 percent of very small (0.3 micron) particles, including bacteria and viruses.
This expanded use has introduced an entirely new challenge, as employers who had a very small respiratory protection program, or not at all, before COVID-19 are now scrambling to get one up and running. This is mostly due to the fact that special testing with appropriate protocols must be followed for each person using these types of respirators, which takes extra time and resources. OSHA’s Respiratory Protection Standard and respirator fit test (RFT) requirements are among the most important of those obligations because they ensure that the specific respirators employees rely on will actually provide the required level of protection. As part of an effective respiratory protection program, RFTs need to be performed and documented for every worker who wears a respirator and for every covered respirator used.
Good IH software helps you implement and maintain a centralized RFT program by standardizing the scheduling, documentation and follow up of your activities. The best systems streamline management across multiple locations and a large number of employees by allowing you to more easily see which workers use which types of respirators, schedule and assign fit tests, select from pre-defined fit testing procedures and record results to easily demonstrate compliance. Typical testing protocols (like those required by OSHA and others) take between seven and eight minutes per employee, and completing paper forms takes another three to five minutes. Software significantly cuts down this time to improve efficiency and verify worker safety and compliance with less effort, time and cost.
Some EHS software providers recognized the unprecedented and urgent need for respirator fit testing among groups that did not already have a program in place and provided complimentary software access to customers serving on the front lines of the COVID-19 response including hospitals, health care facilities, fire departments and other emergency responders. This not only demonstrates the sudden need for an IH program but also how easy software makes it to implement such a program more quickly and easily.
Build More Organizational-Wide Support
A significant, but often overlooked, benefit of IH software is its ability to help gain organizational-wide support and buy-in. IH management is often decentralized, with each site doing its own thing—a trend that creates a vicious circle. The lack of visibility isolates IH from other company efforts, the value of IH gets lost in management’s eyes, and IH is further deprioritized.
No matter your level of expertise, IH software provides the control and visibility needed to manage all aspects of IH and demonstrate the value of your efforts. The best solutions provide you with more than just a passive IH database, but instead provide you with real support to plan and implement your IH program following proven strategies, assess your IH performance in real-time, coordinate with your staff, consultants, laboratories and, most importantly, prove the value of IH to management and others.
Planning for COVID-19 and Beyond
The COVID-19 pandemic significantly impacted businesses and changed the way they approach workplace health and safety. While having an existing IH program in place helped some better approach these changes, it also left many scrambling to create one to protect their workforce.
No matter where you fall on the IH maturity curve, EHS software is empowering employees at all levels to make workplaces healthier, more productive environments. By cutting through the time and complexity of the most important IH tasks, software makes it possible to maintain a world-class program and have real-time visibility and reporting of important activities now during COVID-19 and beyond.
This article originally appeared in the September 2020 issue of Occupational Health & Safety.