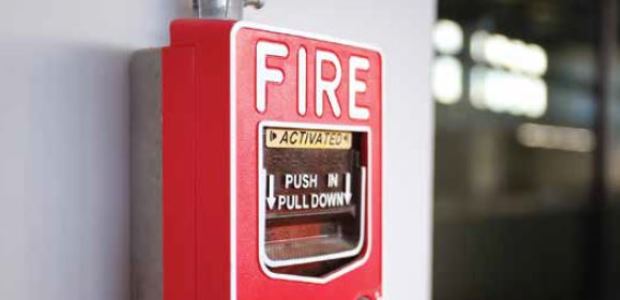
Eliminate 10 Fire Hazards That May Be in Plain Sight
Smoke alarms, carbon dioxide detectors, and hazardous gas sensors need to be tested and sometimes calibrated regularly to ensure they will function properly when needed.
- By Karen D. Hamel
- Apr 01, 2019
Fire departments across the nation respond to about 13 calls from business and industry every hour, according to NFPA estimates. That's in addition to the average of 43 calls from residential properties that come in hourly.
In total, these fires cause more than $13 billion in property damage and kill more than 3,000 people each year. Preventing workplace fires involves identifying the specific hazards that are present in the facility, following local building and fire codes, and putting plans in place to minimize potential fire risks.
At an everyday execution level, routinely checking for some of the most common causes of workplace fires and the injuries related to fires can help to reduce the need to be one of those 13 hourly calls to local responders. Each of these items can be added to daily, weekly, or other routine safety inspections that are already taking place, and most take less than two minutes to check in an area.
Clutter
Good housekeeping is tied to a myriad of safety efforts, and fire prevention is certainly among them! Dust, shavings, clutter, and waste that is permitted to accumulate in work areas does more than just look bad. It can increase the risk of fires and hide other serious safety hazards.
Providing adequately sized recycling and waste collection containers that are conveniently located to work areas facilitates regular removal of unneeded items. Stocking the tools and supplies that employees need to keep their work areas clean and allowing time at the end of each shift for cleaning promotes housekeeping efforts, helps to minimize clutter, and keeps things in order. Hosting quarterly or bi-annual clean-out events can also help to eliminate outdated and unnecessary items from workspaces and keep clutter from piling up.
Improper Fire Extinguishers
Multi-purpose dry chemical fire extinguishers (Class A, B, C) are the most common type of fire extinguisher used in workplaces. However, they won't work on all types of fires. For example, they aren't designed for fighting fires involving metals. In other areas, a carbon dioxide extinguisher may be advantageous. Review the fire hazards in the area to choose the best type for each situation.
Fire extinguishers are useful for incipient fires, but they need to be inspected regularly to ensure that they are still pressurized and in working order. Inspections also should include making sure that the extinguishers are not blocked and that they are located in an area that gives the user a clear exit path if the contents of the extinguisher cannot extinguish a fire.
Electrical Issues
Electrical distribution and lighting equipment issues are the leading cause of fires in industrial properties, according to the NFPA. Electrical issues also frequently make OSHA's top ten list of violations.
Extension cords, daisy-chained connections, and overloaded outlets are three of the easiest electrical problems to spot, as are blocked electrical panels. Checking power cords for frays and verifying that outlets have the proper tension takes a bit longer but will help avoid more than one safety risk.
Inadequate Sprinkler Clearance
Storage space is usually a precious commodity in facilities. It can be tempting to stack things just a little bit higher or to put things on a top shelf, just for the time being. Sprinkler systems need a minimum of 18 inches of clearance to function correctly. Items that are stored too close to sprinkler heads can disrupt their flow patterns and diminish the sprinkler system’s ability to adequately drench an area.
Improperly Stored Chemicals
Few facilities operate without at least a handful of different hazardous chemicals on site. Knowing the properties of each chemical is the first step in keeping employees safe. It's also the first step in storing, handling, and using it correctly to avoid reactions and other unsafe conditions.
Section seven of every hazardous chemical's safety data sheet (SDS) lists storage and handling information. This includes any incompatibilities as well as any other special precautions that need to be taken, such as storing the chemical away from ignition sources, water, or oxidizers; or keeping it within a specific temperature range.
Open Waste Containers
Waste and recycling containers that do not have lids can encourage misuse. Often the misuse is unintentional, but it can lead to the mixing of incompatible materials or putting something hot into a container of combustible materials. Uncovered containers that contain flammable wastes can also release vapors that contribute to indoor air quality issues and can could potentially cause unsafe flammable atmospheres.
Keeping lids on containers helps to prevent unintentional mixing and fugitive vapor emissions. It can also promote recycling and segregation efforts.
Improperly Rated Appliances and Tools
Household appliances and tools that are sold for home use are usually not appropriate for use in a workplace. When these items are safety tested, they are tested under normal conditions for home usage, not for the continual or more frequent usage that usually occurs in a workplace.
Overuse and misuse of household appliances and tools can lead to premature wear, overheating, and short-circuiting. Their use in office areas and breakrooms can also overload breakers.
Defective Detectors
Smoke alarms, carbon dioxide detectors, and hazardous gas sensors need to be tested and sometimes calibrated regularly to ensure that they are still in working order and will function properly when needed. Like detectors, emergency exit lighting, alarms, and signs also should be checked periodically.
Blocked Aisles
Fire codes and OSHA regulations require emergency exit paths to remain clear at all times. Large shipments, construction, demolition, and temporary needs don't negate this requirement. If an emergency exit path needs to be blocked for any reason, alternate routes must be planned before the route is blocked; all exit path markings obscured so that people will not use that path; and the changes must be communicated to all affected employees.
Unmanaged Hot Work
Welding, cutting, brazing, and other hot work are sometimes taken for granted, especially when they aren't part of normal operations. The NFPA estimates that about 2,500 non-residential fires involve hot work each year.
Good housekeeping keeps areas free of combustible materials, and proper ventilation systems and proper chemical and waste management can keep flammable vapors in check. But there is still a need to have and use proper procedures for any and all hot work—even those jobs that will take only a few minutes.
Incorporating regular checks of each of these items into daily, weekly, and monthly inspections will help to ensure that fire safety plans and procedures are working and will continue to minimize fire risks. Each of these items also can be incorporated into toolbox talks or used as a scenario for fire and evacuation drills to keep everyone aware of the need to be vigilant in reducing the risk of workplace fires.
This article originally appeared in the April 2019 issue of Occupational Health & Safety.