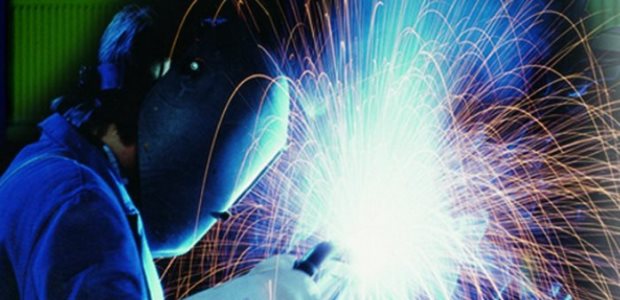
Fire Safety: Managing Risks for Industrial Hot Work
A Job Hazard Analysis is the most critical part of the job—this gives us an opportunity to go in the field with operations and review, recognize, and control hazards at the job site or in the area.
- By Jeremiah Q. Varner
- Apr 01, 2018
Once a fire ignites, it can spread rapidly and out of control in seconds, especially in industrial refineries and petrochemical facilities where highly flammable chemicals are manufactured and stored. Flammable and combustible liquids are classified in the NFPA 30 Code published by the National Fire Protection Association (NFPA) based on their flash point and additional criteria that affect any potential fire risks. Fire safety requires managing the risks or mitigating the causes of potential fires and explosions. Hot work is one of the leading causes for fires in industrial facilities across the nation, according to NFPA.
Hot Work
Hot work is any open-flame welding, torching, brazing, and cutting or the use of any spark-producing power tools, such as a grinder. These activities and tools are common ignition sources. Other ignition sources could be a static discharge from a cell phone or possibly a vehicle in the area that has flammable gases present. What does hot work mean to you and me in a large-scale industrial chemical facility? It could mean a wide array of things, and there are many scenarios, such as retrofitting some new piping in the plant, that require welding and grinding for hours upon hours while the plant is in operation.
Managing Our Risk
During this process, one of the very first questions we should ask ourselves is can we eliminate performing hot work completely? What are our options to reduce and/or eliminate our risk? Can the task be completed without producing an open flame? Sometimes you won’t be able to eliminate the hazard, but you can review alternatives such as the type of tools available. Is there another tool that could be substituted for the hot work project to reduce the hazard? Using a band saw to cut a piece of pipe instead of using a grinder or open-flame torch may take longer, but the hazard and chances of injury to the worker are reduced. We should review our engineering and administrative controls in place—for example, isolating other people in the area from sparks with the use of fire retardant blankets; keeping people out of the area with the proper barricading and tags if there is overhead hot work; and checking for combustible materials, flammable liquids, flammable gases, flammable metals, flammable dust particulates, and electrical equipment.
A lot of these items should be covered during the Job Hazard Analysis, Permitting, and Hazard Field Checks with maintenance and operations, and we will touch on that more below. The training is paramount for everything to come together, and lot of thorough training should take place, such as proper documentation of hot work permitting, Job Hazard Analysis, Hazard Field Checks, as well as fire watch roles, responsibilities, and expectations. Not only should training take place, the training should be continuous in order to stay proficient in whichever role you play in the job. It is important that the proper tools have been given to the craftsmen to manage the risk they have been dealt, such as proper PPE to ensure all members involved are protected. As an industry, it is essential that we are striving for an all-in engaging and sustainable safety culture at all levels.
Hot Work Program and Permitting
It is important to have a good, comprehensive hot work program and permitting process. This gives the maintenance and operations group a chance to engage and talk about the area where the work is going to be performed, as well as the equipment being worked on. It is critical in our industry that all flammables, combustibles, and any other ignitable material are moved 20 to 35 feet away, covered with proper fire retardant blankets for containment, and stored properly as required by OSHA.
Discussions should include lockout /tagout (LOTO) and whether the equipment is ready for maintenance—if there is poor communication, things can go downhill in a hurry. During the field hazard review, it is important that the two groups work together on identifying the hazards and controlling them. Also, if there is a potential for ignitable gases in the area, some companies may require testing in the area with a gas meter to check for any atmospheric ignitable sources, to ensure the area is suitable to perform hot work tasks.
Once we have a fire watch in place with all of the proper tools required, then we are good to commence work. Once the work area is cleaned up and hot work is complete, the fire watch should stay in the area for at least 30 minutes to scan for any hot spots or rekindling of potential fires.
It Takes a Team Partnership
In order to create a zero incident hot work project, it takes a team from start to finish. It takes several different members—maintenance; operations; on-site contractors; engineering; environmental, health and safety department; and any other parties needed to ensure we take the proper steps to have a successful hot work operation.
- It starts with the proper planning: maintenance planners, operations, and engineering communicating about what needs to be cut and replaced, for example.
- Some companies may require the use of a Positive Line Identification policy to supplement as a communication tool. The Positive Line Identification policy should be detailed on where a cut may exactly need to be and have the proper people involved in the process.
- Contractors or company personnel needed and verifying it is the right contractor or person for the job.
- It is up to the maintenance and operations teams to have a clear line of communication to make certain they are working on the right piece of equipment, where the cut is being made, for example; the equipment is depressurized or de-energized, locked out/tagged out; and all other procedural steps have taken place before hot work begins.
- A Job Hazard Analysis is the most critical part of the job—this gives us an opportunity to go in the field with operations and review, recognize, and control hazards at the job site or in the area. Operations should review anything safety-related in the area, such as wind direction, location of the nearest evacuation shelter, safety eyewash/showers and fire extinguishers, and ensuring all combustibles are out of the area.
- The fire watch has the most significant role during hot work activities; he or she is accountable for ensuring no fires take place. The fire watch should have a fire extinguisher that is the correct type and large enough to mitigate an incipient stage fire.
There is the potential for hazards to change in a matter of seconds, and anything can happen, so everyone must stay vigilant and keep their head on a swivel at all times. If we take the proper steps on recognizing our hazards in the beginning, then we are already heading in the right direction. Going through these processes may take longer than the hot work job itself, but our goal should be zero incidents. By taking the proper time to identify, plan, and manage our risks prior to performing hot work, we can reach that goal together.
There Is Always Room for Improvement
In an article from the U.S. Chemical Safety and Hazard Investigation Board (CSB), they investigated incidents involving deaths during hot work in and around industrial storage tanks. There were a lot of improvement opportunities and hazards that could have been mitigated, but we want this to be about the lessons learned and how we can improve going forward in our industry. Here are seven key lessons from recent hot work accidents from the CSB:
1. Use alternatives—Whenever possible, avoid hot work and consider alternative methods.
2. Analyze the hazards—Prior to the initiation of hot work, perform a hazard assessment that identifies the scope of the work, potential hazards, and methods of hazard control.
3. Monitor the atmosphere—Conduct effective gas monitoring in the work area using a properly calibrated combustible gas detector prior to and during hot work activities, even in areas where a flammable atmosphere is not anticipated.
4. Test the area—In work areas where flammable liquids and gases are stored or handled, drain and/or purge all equipment and piping before hot work is conducted. When welding on or in the vicinity of storage tanks and other containers, properly test and if necessary continuously monitor all surrounding tanks or adjacent spaces (not just the tank or container being worked on) for the presence of flammables, and eliminate potential sources of flammables.
5. Use written permits—Ensure that qualified personnel familiar with the specific site hazards review and authorize all hot work and issue permits specifically identifying the work to be conducted and the required precautions.
6. Train thoroughly—Train personnel on hot work policies/procedures, proper use and calibration of combustible gas detectors, safety equipment, and job-specific hazards and controls in a language understood by the workforce.
7. Supervise contractors—Provide safety supervision for outside contractors conducting hot work. Inform contractors about site-specific hazards, including the presence of flammable materials.
(U.S. Chemical Safety and Hazard Investigation Board, Feb. 2010, No. 2009-01-SB).
Final Thoughts
When it comes to industrial fire safety and hot work in our industry, it is important to start the process of engaging with positive interactions and making good decisions together. Before any hot work begins, any consideration of potential hazards and control measures should take place, and we should be asking ourselves, how are we going to safely and efficiently manage our risks?
This article originally appeared in the April 2018 issue of Occupational Health & Safety.