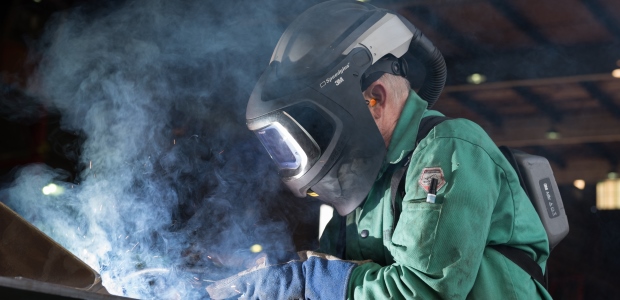
Tips for Dealing with Respiratory Hazards in Welding
After identifying the hazards, the exposure levels from the exposure assessment must be compared to the permissible exposure limit, as set by OSHA, to determine whether respiratory protection is needed.
- By Michael Hallock
- Dec 01, 2017
Welding processes typically generate hazardous ultraviolet/infrared radiation and (intense) visible light that have the potential to cause eye damage. Physical eye hazards include welding spatter and grinding particles. Typically, however, professional welders know about these eye and face hazards and seek out hood features such as auto-darkening welding filters. But other hazards—like welding fumes, which contain gas and/or particles—are sometimes not as well known and may not be addressed.
With welding fumes swirling around workers, they need respiratory solutions that fit under welding shields. According to the U.S. Occupational Safety and Health Administration, it is the responsibility of the employer to identify any hazards in a work environment and to provide the workers with adequate protection.
Employers use a hierarchy of controls to address these hazards and risks. The idea is that the highest priority items on the hierarchy not only do the most to reduce fumes and workers' exposure, but that they also put the least burden of responsibility of the welder. However, every welding fume control has its limitation.
The effects of workers breathing in airborne hazards can lead to serious health complications, many with signs or symptoms that may not immediately appear after the exposure has taken place. Ask yourself: Can the work process be modified to reduce contaminants? Can a different welding technique be used that makes less fume? What ventilation and other engineering controls should be used? However, many times when other types of controls are insufficient workers must be protected with various forms of Personal Protective Equipment (PPE) and training.
When PPE is needed, protecting workers from airborne hazards requires more than simply handing out respirators and should be supported after creating a respiratory protection program. A respiratory protection program will help you identify the hazards, assess the risk levels, select the right type of equipment, and focus on user acceptance and proper use. Following are suggestions on how to develop your respiratory protection program or revisit an existing program.
Begin with an Assessment
Conducting a respiratory exposure assessment and utilizing the results to design an effective respiratory protection plan for your team is a science. It can seem like a complicated science when you factor in the types of things that commonly go into developing and creating a respiratory protection program, such as the initial review of potential hazards, measurements, evaluation of those measurements, selection of controls, their implementation and assessment of their effectiveness, and other factors.
Exposure Assessment
Employers are required by OSHA to evaluate respiratory hazards in the workplace. The assessment should identify:
- What respiratory hazards are present (e.g., fumes)
- Exposure levels
- Whether or not those levels are acceptable—compared to OSHA permissible exposure limits (PELs) or, if lower, other good practice occupational exposure limits (OELs)
It is important to note that this exposure assessment is based on what exists at present. If there are changes in the workplace that may create new exposures, or possibly alter existing hazards, a new assessment needs to be conducted.
Hazard Control Evaluation
If the assessment shows that exposure levels of airborne contaminants are outside of the OSHA limits, the respiratory protection program administrator should first see whether the exposure can be controlled through engineering controls (e.g., workplace ventilation, fume extractors, etc.) or administrative controls (e.g., use of relief workers, rotation of workers, or work breaks). If there is no way to effectively reduce the exposure to acceptable levels, respiratory protection must be provided.
Respiratory Protection—Getting Started
OSHA in 29 CFR 1910.134 details the requirements for a respiratory program. Employers who will be using respirators at their facility must read and understand these regulations.
A written program is also required by OSHA and is a core component to an effective and complete respiratory protection program. Per 29 CFR 1910.134, the written program must address work site-specific procedures for:
- Respirator selection
- Medical evaluation of the wearer
- Fit testing
- Use of respirators in both routine and emergency situations
- Maintenance, cleaning, disposal, and care of the respirators
- Ensuring adequate air quality if supplied air respirators are used
- Training of the worker on the respiratory hazards they may encounter and the proper use, care, and maintenance of the respirator they will use
- Program evaluation to ensure proper functioning
Respirator Selection and APFs
After identifying the hazards, the exposure levels from the exposure assessment must be compared to the permissible exposure limit, or PEL, as set by OSHA, to determine whether respiratory protection is needed. Occupational exposure limits are good practice recommendations set by product manufacturers or other professional societies and also can be considered if exposure levels are below the PEL.
Any respirator used in a U.S. workplace must be approved by the National Institute for Occupational Safety and Health (NIOSH), which has an assigned protection factor (APF). The APF is the workplace level of respiratory protection that a respirator or class of respirators is expected to provide to employees when a complete respiratory protection program is implemented, and it ranges from 10 to 10,000. An APF of 10, for example, means that, when selected and used correctly, a particular class of respirators can reduce exposure levels that are up to 10 times the contaminant PEL to a level determined by OSHA to be acceptable. When considering respiratory products, first identify the necessary APF for each job application that will be performed.
Medical Evaluation and Fit Testing
In some instances, there could be health conditions that could prevent a worker from being able to wear a respirator. OSHA requires workers to have a medical evaluation to help ensure they can safely wear the respirator. The process includes, first, for them to complete a questionnaire regarding health conditions that could affect their ability to wear a respirator, as well as the workplace conditions and hazards they face. A licensed health care professional then must evaluate the employees' responses and advise whether they are able to wear the class of respirator being considered.
After being medically approved, the worker should then undergo fit testing for tight-fitting respirators. Fit testing must be conducted annually or whenever a change occurs that may affect the fit (e.g., significant change of weight that affects the face, significant dental work, or change in model of facepiece). Refer to 29 CFR 1910.134 for more details.
Respirator Training
For maximum benefit from any piece of PPE, it pays to focus on user acceptance and proper use. In addition, OSHA mandates that employers ensure that workers are trained annually. At a minimum, training should cover:
- Why employees need to use respirators
- What a respirator can and cannot do to protect them
- How to properly inspect, put on, take off, and use a respirator
- How to perform a user seal check
- How to use the respirator effectively in emergency situations, including what to do if it does not work properly
- How to recognize medical signs and symptoms that may limit or prevent workers from using a respirator
- How improper fit, use, or maintenance can reduce the effectiveness of the respirator
- Maintenance and storage procedures
- The requirements for federal/state OSHA respiratory protection standards
Respiratory Maintenance
Respirators should be inspected before each use and during cleaning. Users must follow the manufacturer’s user instructions for specific inspection and maintenance procedures, which commonly point to the following considerations:
- Respiratory function
- Tightness and connection
- Pliability of elastomeric parts
- The condition of various parts, including the face piece, head straps, valves, connecting tube, cartridges, canisters, or filters
Program Evaluation
All elements of a respiratory protection program should be evaluated regularly. The respiratory protection administrator should examine all records to make sure tests, training, and inspections are up to date. They also should observe and talk to users of respiratory protection equipment to ensure respirators are meeting their needs and that workers understand and follow procedures for using and maintaining them. It is important to make a record of evaluations and findings, to note any deficiencies, and to document all necessary corrective measures. All of these observations and records help when updating a written respiratory protection program.
Managing an effective respiratory protection program not only keeps companies compliant with relevant regulations, but a well-run program also is the best way to help ensure that your welders are protected from respiratory hazards.
References
1. A Strategy for Assessing and Managing Occupational Exposures 4th ed. (2015) American Industrial Hygiene Association (www.aiha.org)
2. 29 CFR 1910.134 – Respiratory Protection (www.osha.gov)
3. www.3M.com/PPESafety
This article originally appeared in the December 2017 issue of Occupational Health & Safety.