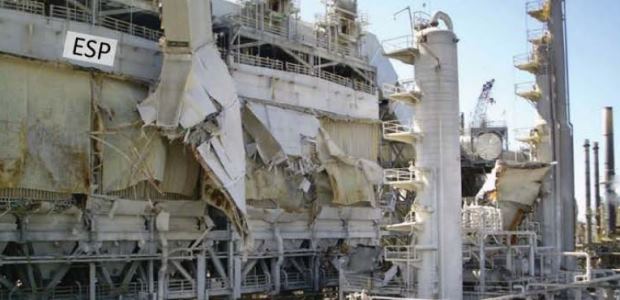
CSB's Top Torrance Recommendation Concerns Variances
The U.S. Chemical Safety Board's final report on the February 2015 explosion at the ExxonMobil refinery in Torrance, Calif., also recommends that the company require identification of all safety critical equipment and consequences of failure for each mode of operation, and also ensure safety critical devices can successfully function when needed.
The U.S. Chemical Safety Board released its final report May 3 on the Feb. 18, 2015, explosion at the ExxonMobil Refinery in Torrance, Calif., a blast that injured four workers and resulted in $566,600 in penalties assessed by Cal/OSHA against ExxonMobil Refining & Supply Company. The report establishes causes of the explosion and contains 10 recommendations in all for ExxonMobil Corp., Torrance Refining Company, and American Fuel and Petrochemical Manufacturers.
In the report, the board said it "views the modernization of United States process safety management regulations as one of the most important chemical safety improvement goals," and it supports the effort to improve process safety management of California refineries and asks California to fully implement the recommendations issued in CSB's Chevron Richmond refinery investigation.
The board's news release about the Torrance final report says as a result of the refinery explosion, the refinery was run at limited capacity for more than a year, raising gas prices in California and costing drivers in the state an estimated $2.4 billion.
The explosion occurred in the refinery's fluid catalytic cracking unit. The report emphasizes it is critical that hydrocarbons don't flow into the air side of that unit because this can create an explosive atmosphere; the board determined that on the day of the explosion, a spent catalyst slide valve that acted as a barrier failed, hydrocarbons flowed into the air side of the unit, and they ignited inside an electrostatic precipitator, or ESP, which exploded.
"This explosion and near miss should not have happened, and likely would not have happened, had a more robust process safety management system been in place," said CSB Chairperson Vanessa Allen Sutherland. "The CSB's report concludes that the unit was operating without proper procedures."
The report says there were multiple gaps in the refinery's PSM system, allowing for the operation of the FCC unit without pre-established safe operating limits and criteria for a shutdown, and the refinery relied on safeguards that could not be verified and reused a previous procedure deviation without a sufficient hazard analysis of the current process conditions. Also, the spent catalyst slide valve was degraded significantly.
A chart in the report describing the incident shows how severe violation problems were addressed three times during the week leading up to the explosion and personnel decided to reuse a variance developed for a 2012 procedure without technically reviewing it to ensure safeguards it contained were adequate for the 2015 operation.
The report recommends that ExxonMobil require identification of all safety critical equipment and consequences of failure for each mode of operation, and also ensure safety critical devices can successfully function when needed. It has similar recommendations for Torrance Refining Company and also recommends that Torrance Refining Company implement protective systems that prevent ignition of flammable gases, and it asks American Fuel and Petrochemical Manufacturers to facilitate forums for member companies and fluid catalytic cracking unit engineers to discuss the causal factors and lessons of the Torrance explosion.
ExxonMobil sold the refinery in July 2016 to PBF Holdings Company, LLC, which now operates as the Torrance Refining Company. But since the February 2015 explosion, the refinery has experienced multiple incidents, according to the report.
"There are valuable lessons to be learned and applied at this refinery, and to all refineries in the U.S. Keeping our refineries operating safely is critical to the well-being of the employees and surrounding communities, as well as to the economy," Sutherland said. "Adoption of and adherence to a robust safety management process would have prevented these other incidents. In working with inherently dangerous products, it is critical to conduct a robust risk management analysis with the intent of continual safety improvement."