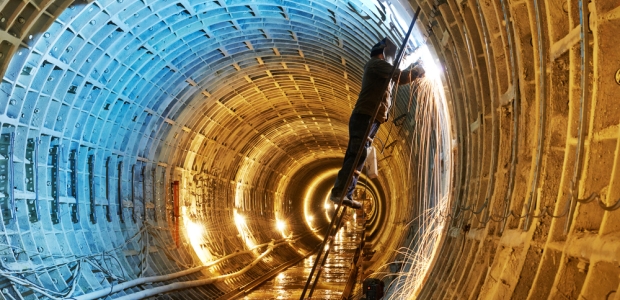
Optical Clarity: Why It's Important and What It Means for You
Viewing your welds through a clearer, better-quality lens allows your eyes to work longer with less fatigue and also less overall strain on your body.
- By Jamy Bulan
- Apr 01, 2015
Selecting the best auto-darkening welding helmet reaches beyond standard occupational safety issues; it also should take the wearer's vision into account. Wearing the right helmet not only protects your face and eyes from sparks, but also can contribute to your overall productivity and work quality. And it all comes down to the helmet’s optical clarity, or how well you can see out of it.
We know that welding isn't an easy process, especially for welders who wear a helmet for the better part of an eight- or 10-hour day, sometimes while working on thin, exotic, and/or expensive materials. When you're able to more clearly perceive subtle variations in the ever-changing arc and weld puddle, you're able to deliver more accurate end results, with higher-quality welds.
A helmet that's too dark or has too many variations in the quality of sight through its filter can cause discomfort, vision problems, and even irregular welds. Think of a high-quality auto-darkening helmet and its cartridge in the same way as you think of your TV: You want to watch sports and movies in crystal-clear high definition, not on an old, grainy analog screen, right? Shouldn't you want the same viewing quality from your welding helmet?
That's where optical clarity comes in. While the United States hasn't yet adopted any formal requirements for welding helmet design, manufacturers are finding guidance in the third-party European Standards that govern eye and face protection for the welding industry. Prefixed by EN (European Norm), the standard that governs auto-darkening welding helmet cartridges is known as EN379 and incorporates important ratings for optical clarity.
Defining Optical Clarity
These ratings are determined by tests that measure light transmission across the welding cartridge, as well as scattered light from the cartridge's layers. Rating tests occur in each of the following four classes of optical clarity:
- Optical (accuracy of vision). Qualifies how distorted the image is when you look at it through a welding helmet lens. Is it like looking at something through rippled water, or is it clear and crisp?
- Diffusion of light. Examines the manufacturing impurities in the cartridge’s glass. Is it clear and defect free? Is it uniform?
- Variations in luminous transmittance (light or dark areas within the lens). Focuses on the lens’ adjustable shade function and consistency of this shade across different points of the lens surface. No random areas should be too bright or too dark in comparison to others.
- Angle dependence on luminous transmittance. Tests for a clear view without stretching, dark areas, blurriness, or problems viewing things at an angle, as the result of inconsistent shade.
Cartridges are graded on a scale of 1 to 3 in each class. A score of 1 is perfect, while a score of 3 is the worst rating. The best rating is 1/1/1/1. Auto-darkening welding helmets rated with EN379-1/1/1/1 for optical clarity deliver even shade levels across the full height and width of the viewing area, which offers little, if any, distortion of view from clear, uniform glass.
While the EN379-1/1/1/1 rating is not a requirement in the United States, it does offer a known benchmark for quantifying lens clarity. Not all U.S. manufacturers use this rating, but we have begun to incorporate this standard into our helmet design and manufacturing process.
Benefits of Clearer Helmet Vision
There's a real benefit to undergoing the testing to achieve this rating, even though it isn't required: It eliminates the user's guesswork involved in trying on helmets and determining by trial and error which one offers the best viewing lens. Now, when you're looking to upgrade your helmet, you will know that one with a 1/1/1/1 optical clarity rating will deliver a perfect view and the best quality lens.
Experienced welders who already have used a 1/1/1/1-rated helmet report they immediately can tell the difference in optical clarity. They say they can see better, the workpiece is more clearly in focus, and the overall experience is more comfortable than using a helmet with, say, a rating of 1/2/1/2. These welders also have said they see the arc with less distortion with the higher-rated lens and have noticed clarity issues in helmets with a lower rating. While these parameters might be subtle, professional welders can and do notice the difference between 1 and 2 and a huge difference between 1 and 3.
These differences can play a role in overall productivity. If you're looking through a distorted lens with impurities and inconsistent shade, your eyes will strain to see what you are doing. This could cause you to work harder. Viewing your welds through a clearer, better-quality lens allows your eyes to work longer with less fatigue and also less overall strain on your body.
Other Helmet Considerations
When evaluating helmets, other factors do come into play beyond optical clarity. Welding helmets must meet relevant safety standards. In North America, applicable standards are ANSI Z87.1 in the United States and CAN/CSA Z94.3 in Canada. Before purchasing a helmet, be sure the helmet meets prevailing industry and regulatory standards.
Also consider the type of welding you plan to do. Amperage ratings associated with various welding applications generate different levels of light emission, thus requiring different shade levels. Advanced auto-darkening helmets protect from harmful light emissions at all times and darken to almost any pre-selected shade in milliseconds, thanks to quick-changing LCD (liquid crystal display) technology in the auto-darkening cartridges. With auto-darkening helmets, welders can see clearly while the helmet is in the down position, so that setting up to weld can be performed with the hood in position.
These advanced auto-darkening helmets offer a full shade range of up to 6-13 with additional grind modes, allowing welders to optimize the shade for optimal protection and greater comfort. Welders who make frequent changes between welding processes and applications likely will find this beneficial.
Also, be sure to also to consider headgear style and adjustability, the overall weight, whether or not the helmet can lower with a simple head nod, hands-free operation, and even the comfort of the built-in sweatband. All of these can affect wearer comfort and productivity.
These days, selecting an auto-darkening helmet involves more than just pulling one off of the shelf, putting it on, and striking an arc. Optical clarity plays a major role in the decision process, moving from a factor that once was hard to determine without trial and error to something that can be identified through quantifiable benchmarks and ratings. The demand for better optical clarity in auto-darkening helmets is increasing in the United States and will only get stronger as welders continue to demand top-quality viewing capabilities from their eye protection.
This article originally appeared in the April 2015 issue of Occupational Health & Safety.