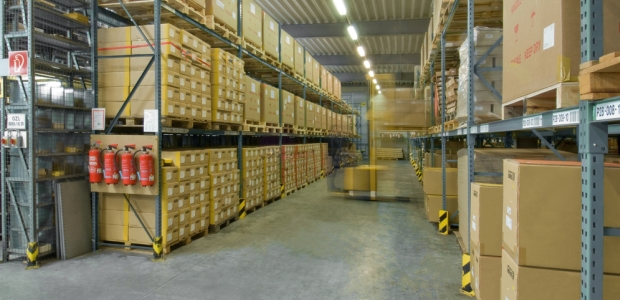
Elements of a Quality Maintenance Program
Best practices include completing documented equipment inspections on schedule and consistently performing detailed cleaning of equipment.
- By Jerry Laws
- Dec 01, 2014
Facility maintenance is a multifaceted topic, involving diverse programs and responsibilities that range from housekeeping and contractor hiring and oversight to maintenance employees' lockout/tagout training. All of these are worth revisiting periodically to ensure your programs haven't gone stale or fallen behind changes in processes, personnel, or your facility's layout.
Having an agreed upon definition of preventive maintenance "is important for good communication in meetings, improvement efforts, and training seminars," Torbjörn Idhammar, president of IDCON Inc., a reliability and maintenance managing consulting firm, explained in an online article1 about preventive maintenance (PM) best practices. "We have often attended meetings or interviews where we are told a plant is continuously working on improving preventive maintenance. When we ask for the definition of PM, we notice that there are as many definitions of PM as there are people. How can we expect to improve PM if we are not clear on what PM really is?"
IDCON defines PM as "essential care and condition monitoring," using the acronym PM/ECC, he wrote. His article explained that the company uses 95 points to evaluate a plant's performance, and that top-notch companies follow alignment and lubrication stands, complete equipment inspections on schedule and document them, and consistently perform detailed cleaning of their equipment—as well as redesigning dirty areas so equipment won't become contaminated.
According to OSHA, the elements of a good preventive maintenance program for ventilation systems include:
- Establishing a safe place to file drawings, specifications, operating instructions, and other papers generated during design, construction, and testing
- Establishing a program of periodic inspections. While the types and frequencies of inspections depend on the specifics of the operation, the agency suggests daily inspection activities (visually inspect hoods, ductwork, access and clean-out doors, blast gate positions, hood static pressure, pressure drop across air cleaner, and verbally communicate with users about system performance); weekly (check air cleaner capacity, fan housing, pulley belts); and monthly (check air cleaner components).
- Establishing a preventive maintenance program
- Providing worker training about the purpose and functions of the ventilation system
- Keeping written records, not only of original installations but also of all modifications, problems, and resolutions
Housekeeping
Some OSHA standards reference housekeeping, notably 29 CFR 1910.22, the Walking-Working Surfaces standard, which requires that "all places of employment, passageways, storerooms, and service rooms shall be kept clean and orderly and in a sanitary condition." The agency has noted that 1910.22(a)(1) requires employers to remove dust accumulations, including accumulations of combustible dust.
Inspections and cleaning at regular intervals also are recommended in NFPA 654, Standard for the Prevention of Fire and Dust Explosions from the Manufacturing, Processing, and Handling of Combustible Particulate Solids. This standard recommends inspecting for dust accumulations and cleaning dust residues at regular intervals, as well as implementing a hazardous dust inspection, testing, housekeeping, and control program. Section 8.2 of the 2013 revision of the standard covers housekeeping requirements; if a facility's hazard assessment determines that dust accumulations present a flash fire or explosion hazard, the operation must set housekeeping frequencies that prevent the threshold accumulation levels from developing and must put an inspection process in place to monitor the accumulations.
Housekeeping is the practice of maintaining a clean, clutter-free, organized work site, Paul Giannetti, a workers' compensation attorney in Albany, N.Y., pointed out in an April 2014 article, "Good Housekeeping is Good Business,"2 which he wrote for the OH&S website. "Implementing effective housekeeping practices is critical for businesses of every size, but particularly for hospitals and construction, manufacturing, and retail industries, where risks of STFs [slips, trips, or falls] are highest. Much of good housekeeping is common sense. Unfortunately, not everyone applies the same degree of common sense at the same time. To ensure that all employees understand the importance of good housekeeping practices and how to engage in them, it is essential to have explicit plans, instructions, and routines."
He recommended establishing housekeeping procedures as part of a daily routine and also having a mandatory program to train all employees, including temporary workers, on good housekeeping practices. "These programs should give a clear picture of the end goal of the housekeeping plan (a safe work area and zero STFs) and effectively communicate the importance of good housekeeping," Giannetti wrote. "Make sure training is more than a lecture. Get employees engaged in a discussion about hazards and potential hazards in their work environment and ask for their ideas about how these hazards can be minimized. Help employees to see what’s in it for them: Good housekeeping can not only keep everyone safe, but also boost morale and productivity, making for a more pleasant work environment. By the end of the program, employees should fully understand both their individual and global responsibilities toward maintaining a safe work site. Individual responsibilities include whatever specific housekeeping tasks are expected of them (e.g., cleaning up spills, putting away tools, etc.), as well as the duty to act in a manner that reduces the risk of STFs (no running , distracted walking, etc.). Global responsibilities include developing the habit of noticing and reporting hazardous or potentially hazardous conditions and encouraging fellow workers to abide by housekeeping practices for their own safety."
Lockout/Tagout
The OSHA Lockout/Tagout standard, 29 CFR 1901.147, directs employers to protect employees from the unexpected energization, start-up, or release of stored energy while they are performing servicing and/or maintenance operations.
OSHA defines servicing and/or maintenance as "workplace activities, including installing, setting up, inspecting, adjusting, repairing, replacing, constructing, modifying, and maintaining and/or servicing machines or equipment," and it says these activities include lubrication, cleaning or unjamming of machines or equipment, and making adjustments or tool changes. Setting up includes any work done to prepare a machine or equipment to perform its normal production operation.
References
1. http://www.idcon.com/resource-library/articles/preventive-maintenance/461-checking-best-practices-for-preventive-maintenance.html
2. http://ohsonline.com/blogs/the-ohs-wire/2014/04/good-housekeeping-is-good-business.aspx
This article originally appeared in the December 2014 issue of Occupational Health & Safety.