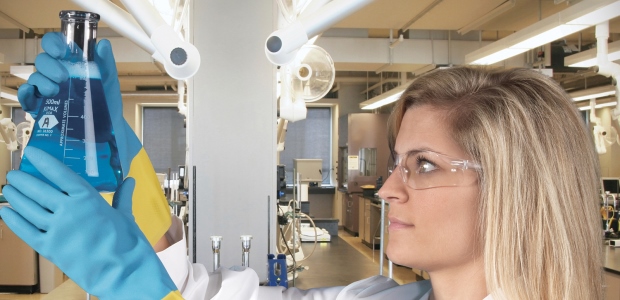
Choosing the Best Protective Eyewear
Safety glasses selection seems so simple on the surface, but many factors should influence the choice.
- By Mike Myrick
- May 01, 2014
Every day, about 2,000 U.S. workers have job-related eye injuries. This statistic should make all of us see the startling need for workers to wear safety glasses. The Occupational Safety and Health Administration has stated a number of times that as much as 90 percent of these injuries can be prevented with the proper use of safety glasses.
According to OSHA's 29 CFR 1910.132, employers must provide training for each employee who is required to use PPE in the workplace. How do we assist the workers to decide which glasses are best for their application? It is important for us to look at the coating options and application needs and understand how to determine the proper fit.
First, recognize that all coatings are not equal. There are many options for coatings with significant performance levels in the industry. Time spent evaluating coating performance will reward you by making the correct selection and best performing product. Challenge your eyewear supplier for testing data. Many safety directors have started turning to uncoated lens options to save some money. Is there a place for uncoated lenses in the industry? Yes, they absolutely have a place. Uncoated lens options can offer a cost savings for visitor or walk-through glasses. If uncoated options are only used for non-work related situations, they might assist with the bottom line. There are a number of reasons you would not want to use these options while working, however. One is fogging; another is scratches that impede vision.
Now that we have seen the need for coatings in working environments, let's look at the options available. For the past 18 years I have seen safety directors struggle with the need for premium coatings. If a worker's glasses are fogging, it will pose a potential risk. Workers might attempt to "look around" the fogging or remove the glasses out of frustration. There are a number of fog- or condensation-reducing coatings. The main options feature either a hydrophilic or hydrophobic coating. Hydrophobic, or water-fearing, coatings repel the condensation, causing the liquid to bead and roll off the lens. In contrast, hydrophilic, or water-loving, coatings absorb the condensation, causing the water droplets to spread across the lens.
"While people have noticed these differences since ancient times, a better understanding of these properties, and new ways of controlling them, may bring important new applications," said David L. Chandler of the MIT News Office.
Embracing New Technologies
The safety industry has done an exceptional job in recent years of embracing new technologies to improve workers' vision.
One common issue wearers have with anti-fog and condensation-reducing coatings is that the coatings wear off. Many users ignore manufacturer instructions. The majority of safety glasses manufacturers offer cleaning options, such as a pre-moistened lens cleaning towelette or spray and tissue options.
It is important to follow manufacturer recommendations. A major pharmaceutical company contacted me a few years ago: An employee had scratched his eye when the glasses broke as he donned them. The safety director sent me the glasses to determine why they broke. When I received them, I noticed the material was extremely brittle. Upon further discussion, we discovered the wearer had cleaned the glasses with 80 percent alcohol and household cleaners for 30 days. The combination of the chemicals caused the polycarbonate frame to dry and easy to break. If the wearer had followed the manufacturer recommendation of using proper cleaning products, the accident might not have occurred.
Another common concern is that with the increased expense of the anti-fog coating, some manufacturers do not apply a scratch-resistant coating. When this occurs, the lens becomes scratched easily, thus causing reduced visibility. Users should ask manufacturers if the anti-fog coating also provides a hard coat or scratch-resistant coating.
Ensuring Sufficient Protection
Another common question with safety glasses is what to wear in certain circumstances. I have been asked many times, "Will all safety glasses work for every circumstance?" The answer is an emphatic "No!"
Safety directors are challenged to assist workers in determining the best coverage, fit, and lens option. Many times, I have walked into plants and observed workers not wearing safety glasses. When asked, they say that they only have flying debris "sometimes," so they don't need to wear them all the time.
A co-worker of mine walked into a factory that manufactured car seats. In the area he walked through, there were many workers using rivet guns and rivets were flying, but workers did not think this was a hazard. Any time debris has the potential to be airborne, you have a potential risk. This can include, but is not limited to, dust, flying debris, and chemicals, in addition to bump hazards.
Many accidents involving workers have occurred when they walked into objects. Most workers do not wear proper eye protection because they don't feel safe due to improper fit. Keep in mind that the area that we are intending to protect with safety glasses is the orbital area--the area within your orbital bone. Basically, if you feel the eye socket (hollow place in the skull that hold the eyeballs), the bone around this area is the orbital bone. The wearer wants to make sure this area is completely covered by the lens of the glasses.
For that to be possible, companies will need to offer multiple styles. This can become expensive and is not easily maintained if too many options are offered. Most manufacturers can assist the safety director in determining a few options that will meet everyone's needs.
Eye Fatigue
Another issue with applications is the amount of light in the area workers are exposed to in a given shift. Eye fatigue is a common and very genuine issue in the work place. The ANSI/ISEA Z87.1-2010 standard in section 7 discusses the amount of visible light that is transferred or allowed through the lens. For example, a typical clear polycarbonate lens offers a 15 percent filter, or it allows 85 percent visible light. As you change the tint of the lens, you will change the amount of visible light transmission, thus changing the clarity of the worker's eyesight.
An example would be a construction worker working outdoors during daylight hours; he would need to wear a gray or mirror lens to filter light on sunny days. That same worker would need to change to clear or lighter shades lens option on cloudy days to ensure full visibility. In applications where a worker will be dealing with glare from water or metal, a polarized lens would be most applicable.
Use caution when using polarized lens options in the safety industry, however. After multiple tests of polarized lenses in the safety industry, we have found that some do not meet the high-impact portion of the standard. In general, polarized lenses that meet the standard tend to cost more than other shaded lens options. If in doubt, ask the manufacturer to provide you with test data. In areas that include heavy debris, sparks, or chemical splash, faceshields provide additional protection to the entire face.
Ask Them What They Want
So how do you choose a safety glass that your workers will wear and be safe with? First, this is a common struggle among safety directors. Do not feel alone. As a safety director, I struggled to get my workers to wear their safety glasses. So what worked for me? I asked them what they wanted.
I know many of you just threw the magazine across the room or clicked to close your browser. For those that are still with me, having the workers give input will help you empower them to help you. Ask them what they like and don't like about the glasses they are currently using. Document that information and have a reputable manufacturer assist you in analyzing with need.
Many workers want a more stylish option, which will typically translate in a higher-priced option. Keep in mind, an average injury will cost the company $36,000, according to the Bureau of Labor Statistics. If you look at it that way, the increased expense is very small. If the workers feel they look good and the glasses are comfortable, they will be more likely to wear the glasses.
Fit is another complaint by workers. No one glass fits all workers. You will need to have multiple options and some with adjustability. Have the manufacturer bring in several options to "fit test" each employee. This will give you an idea of the number of options you will need to stock. Look for comfort features, such as TPR (thermo plastic rubber) temples and nose pads or adjustable nose pads. Foam-lined options also offer additional comfort and dust protection.
Coatings, applications, and choice, oh my! Safety glasses selection seems so simple on the surface, but many factors should influence the choice. Evaluating the need, the type of hazard, and employee choice will assist in protecting the worker.
Many of us who subscribe to this great publication have one goal: "Protect the workers." Taking time to understand the options offered today might help an employee go home with his or her eyesight at the end of their shift.
This article originally appeared in the May 2014 issue of Occupational Health & Safety.