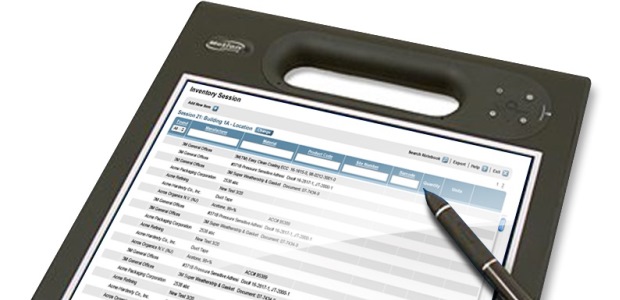
Chemical Management on the Go -- What's New in Mobile Solutions
It's critical to ensure that key chemical safety information and inventory management functions are readily available and at the fingertips of your personnel.
- By Kraig Haberer
- Oct 01, 2013
Enterprise mobility continues to gain momentum as the consumer world impacts the business world. As more and more of us carry technology capable of serving ever-expanding personal and entertainment functions, it's natural to think about how our mobile devices can play a part in our business careers, as well as our personal lives. In fact, there is a new term to describe this movement: B.Y.O.D., known as "Bring Your Own Device."
This phrase simply means that business workers are influencing the mobile movement in the workplace by bringing the devices that they are already carrying with them. Instead of top-down mobile initiatives, many opportunities in enterprise mobility are happening because of a swell of support and interest from the ground up (i.e., at the individual employee level). This article will discuss trends and opportunities for environmental, health, and safety professionals to incorporate mobile solutions into their work lives.
Why Mobility Matters in EH&S
The B.Y.O.D. trend, especially in the EH&S group, is sparked by the expectation and need to rapidly access key information in the plant, in the field, and with customers. This can range from looking up an SDS, reviewing safe use instructions for a particular chemical, or even updating inventory information for your chemical stores. For many companies, the need for chemical information is based on compliance needs, safety needs, and manufacturing operations needs as well. Thus, this multi-faceted requirement leads to several different opportunities for business applications to step in and deliver a mobile solution.
Chemical safety and chemical management occurs in the field, not in the office. Therefore, it's critical to ensure that key chemical safety information and inventory management functions are readily available and at the fingertips of your personnel. For example, it's no longer efficient or practical to manage hard-copy binders of material safety data sheets. Nor is this a good solution for remote or mobile workers because of the time, cost, and upkeep of physical binders all over the organization and in the field. Therefore, having safety data sheet (SDS) lookup applications available on a smartphone or tablet is a quicker, more efficient method of delivering critical safety and compliance information on a timely basis directly to field personnel. Mobile applications can speed processes and support rapid decision-making, both of which translate into increased productivity. For EH&S professionals, it also translates into safety and compliance.
The other advantage for environmental, health, and safety professionals is that mobile applications and devices "democratize" key safety information and processes. With many safety organizations running leaner because of overall cost minimization efforts, mobile apps allow companies to do more with less. As an example, leveraging mobile technology for physical chemical inventories and the reconciliation back to the SDS notebook can be drastically streamlined. Simply scanning inventory items with bar code scanners and having the application perform automated lookups against the SDS notebook kills two birds with one stone. First, you get the item inventories recorded. Second, the app is checking to see whether a safety data sheet exists. Taking this one step further, some chemical management applications will let you perform a service request directly from the app to request or upload a safety data sheet if one doesn't exist for that inventoried chemical.
Apps for Chemical Safety and Chemical Management
According to an Arc Advisory Group Study on Mobility Applications for the Process Industry, the top adoption trends for business applications based on mobile solutions focused on maintenance/asset management, inventory management, real-time reporting/alerting, and facility management. This is very much in line with the opportunity for mobile deployments in the chemical management arena. The table below outlines some of the current mobile solutions available today.
Table 1: Areas to Consider for Mobile Applications
Area |
Mobile Application Examples
|
Compliance |
Mobile HazCom Compliance
Chemical Inventory-Taking
Chemical Inventory Tracking
SDS to Chemical Inventory Reconciliation
|
Safety |
Remote SDS Lookup
Online and On-site Training
QR Code Lookup for Reference Materials (e.g., Safe Use Instructions, SDS, etc.)
Industrial Hygiene Apps
|
Sustainability |
Material Analysis and Risk Profiling
Sampling and Testing
|
The most impactful and readily available chemical management applications are chemical inventory tracking and SDS lookup/searching via barcodes or QR (Quick Response) codes. With OSHA adopting the GHS standard in the HazCom 2012 standard, all companies will see an influx of safety data sheets coming across their desks. However, the first step in having an accurate, compliant SDS notebook is having an accurate, compliant chemical inventory. These mobile applications not only help you with the inventory, but also they help you with the SDS notebook updating.
With QR codes or barcodes, there are also some innovative new ways to attach chemical and safety information to your chemical containers, as well as retrieve that information in a split second with common smartphones. Additionally, there are some interesting solutions available right now for cross-referencing materials in the lab or field for regulatory exposure, physical hazards, health hazards, and other common properties of a hazardous material. The primary gain here is speed in decision-making and not having to rely on an R&D group running a profiling request through the EH&S team for any environmental, health, or safety concern.
Making Mobile Work For You
So, how do you identify a business process that is right for a mobility solution?
First, the process or business need must be time-sensitive. Is the safety, compliance, or EH&S decision-making need measured in minutes or days and weeks? Obviously, when dealing with chemicals and chemical safety, minutes matter more than days, so it tends to be a good candidate for mobile technology. Additionally, it may be important to have ingredient or substance data readily available in the field or for research purposes so as to accelerate decision-making regarding use of materials in product manufacturing, assembly, or maintenance.
Second, is the process based on centralized data or a common workflow, but it needs to be disseminated throughout your facility or across multiple facilities? The management of chemical data and safety data sheets is (and should be) centralized for efficiency and compliance purposes; however, access to the information needs to be universal and readily accessible. This is another reason why mobilizing your chemical information is important.
Finally, is your organization geographically and/or functionally diverse? If you have a global, national, or even campus-wide enterprise with centralized EH&S teams, mobile applications will enable process control and information dispersion to be much easier for both you and your IT department.
However, having said all this, don't go mobile just to go mobile. Have a specific business need, with a specific mobile technology approach, and targeting an expected business outcome to ensure success with your mobile technology adoption.
This article originally appeared in the October 2013 issue of Occupational Health & Safety.