Global Classification Systems for Chemical Protective Apparel
ISO 16602 and ANSI/ISEA 103 provide a way for you to specify its performance in an objective and detailed manner.
When faced with protecting workers from chemical hazards, there are no "all hazards" chemical protective garments. The chemical hazard, work activities, and environment vary from job to job. An "all hazards" garment would end up being too protective in most situations. Over-protection may limit the workers' ability to perform their jobs, adds the risk of heat stress, limits the workers' ability to see or be seen, reduces agility and dexterity, and adds cost. That is why you have so many chemical protective clothing options available to you.
The task becomes selecting the garment with the right seam, design, and material and selecting the matching respirators, gloves, and footwear. And that selection process must also consider factors such as flex and abrasion performance, cut resistance, flame resistance, and color.
You now have access to three chemical protective clothing classification systems that consider most of the important factors. When fully adopted, these classification systems will help you select chemical protective clothing for your situation. The classification systems cover a range of protection, from total isolation (Level A) to garments intended to protect part of the body from light liquid contact (aprons). Europe implemented a six-level classification system over 10 years; the rest of the world has begun to recognize and use this concept. The limitation is how fast manufacturers classify their products so that you will be able to use these useful tools to evaluate chemical protective apparel for your application.
One system is found in the recently released American National Standard for Classification and Performance Requirements for Chemical Protective Clothing (ANSI/ISEA 103). The second system is found in ISO 16602 Protective clothing for protection against chemicals -- Classification, labeling and performance requirements. The ISO system closely resembles the oldest six-level classification system developed by the Committee for European Normalization (CEN).
The oldest of the three systems comes from CEN. In 1989, as the Common Market government was forming, the European Union parliament mandated a system of common personal protective equipment standards. For chemical protective clothing, this mandate led to a six-level system (Table 1). This system has been in use in the Common Market for more than 10 years and is now being referenced by countries outside the EU.
Members of the Protective Clothing Committee of the International Safety Equipment Association (ISEA) drafted a similar six-level system in the late '90s. This system was introduced as a working document to the International Standards Organization (ISO). As that document moved through the ISO process, it was significantly modified until it closely resembled the CEN six-level framework. This is understandable, given that many of the ISO committee members serve on the corresponding CEN committees. That document was issued in 2007 as ISO 16602. Both the ISO and CEN systems refer to each of the six levels of garment performance as "Types" (Table 1).
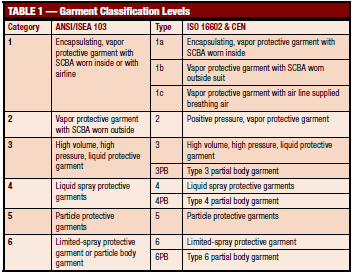
While its original submission moved through the ISO process, the ISEA Protective Clothing Committee continued to work on its own document. That document was processed through the American National Standards Institute (ANSI) and issued in 2010 as ANSI/ISEA 103. To avoid confusion with the CEN/ISO classification system, the six levels of protection in ANSI/ISEA 103 are referred to as "Categories" (Table 1).
For each Type or Category, there is a series of performance requirements. There are performance requirements based on whole garment testing and requirements on the materials, seams, closures, and interfaces with gloves, boots, and respirators. The performance requirements specify the test methods and minimum acceptable values. The most significant differences between the six levels of performance are the whole garment tests. These whole garment tests have a major impact on the garment design. Many of the material and seam tests are used across the six levels, but in most cases, the minimum acceptable values differ by level.
To provide additional granularity, the test results are stratified. An example of how tear resistance results are layered is shown in Table 2. In the ISO/CEN documents, these levels are called "Classes," while in the ANSI/ISEA document they are called "Levels."
This stratified system for test results allows you to fine-tune your garment selection. For example, if you need additional durability or barrier, you can select a garment with higher than minimum levels of barrier or durability. You might specify an ISO Type 4 garment with Class 4 tear resistance (or an ANSI/ISEA Category 4 garment with "M" Level of tear resistance). The CEN standard for vapor-protective emergency response garments (Type 1 ET) uses this concept. Because of the severity of the application, Type 1 ET requirements are generally higher by requiring higher than the minimum Type 1 requirements. The specification for Type 1 ET calls for a Type 1 garment with specific minimum performance Classes for the requisite tests.
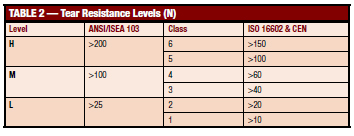
The requirements for ISO/CEN Type 2 and ANSI/ISEA Category 2 are the most obvious differences in these classification systems. The ANSI/ISEA standard makes no special provision for positive-pressure air-fed suits. When worn without a separate respirator, these garments provide respiratory protection and are classified as respirators under U.S. regulations. Performance specifications for air-fed ensembles are addressed in ASTM F2704, Standard Specification for Air-Fed Protective Ensembles.
Partial body garments are also handled differently. Under the ANSI/ISEA structure, partial body garments are considered only in light liquid exposure situations (Category 6). The ISO and CEN systems anticipated partial body garments under higher volume and higher pressure liquid exposure situations (Type 3 & 4).
The requirements for the other levels result in garments with similar overall performance and design. Except for the Category/Type 2, the three standards have similar performance requirements. And in many cases the same test methods are used, but the minimum performance requirement may be slightly different. There are cases where the test methods are different but have similar names. Be warned; similar names does not mean the method is the same. An example is burst, which uses a 6-inch-diameter specimen in ISO/CEN test method but only a 1-inch-diameter specimen in the ANSI/ISEA specified method. Confusion is also created by liquid chemical barrier methods that vary between permeation, penetration, or repellency.
Certification is another obvious difference. The ANSI/ISEA document contains detailed information on the certification process. Certification is not mentioned in the ISO & CEN documents. ANSI/ISEA 103 specifies the roles of the manufacturer, certification agency, and testing labs in the certification process. Similar to the NFPA protective clothing standards, ANSI/ISEA 103 assigns oversight of the certification program to third-party independent agencies. ANSI/ISEA 103 describes a system of ongoing, annual recertification that is missing in the ISO and CEN systems. This certification process ensures that the manufacturer continues to produce compliant products.
The ANSI/ISEA document also introduces the use of AQL (acceptable quality limits). AQL is a statistical basis to ensure ongoing compliance with the requirements of the standard. It is commonly used in medical device quality control, including medical garments.
Using the Standards to Select Apparel
In summary, these standards provide a way for you to specify the performance of chemical protective clothing in an objective and detailed manner. You can use these classifications as a basis of your purchase specifications. Manufacturers are just now beginning to certify garments to the ISO 16602 and ANSI/ISEA 103. Many of the garments you already use should fall into one of the classifications. If they do not, you should ask why.
These multi-level classification systems address the lack of an "all hazards" chemical protective garment. When the chemical, tasks, and environments are assessed for hazards, we can define performance requirements for "all hazards" we reasonably anticipate for that activity. A good example of "job-specific, all-hazards" performance standards are those established by the protective clothing project in NFPA. That project has defined different standards for different jobs: structural, wildlands, and proximity fire fighting, emergency medical response, hazmat, first response to CBRN terrorism, and urban search and rescue. The requirements within those standards are very different, yet each establishes minimum performance requirements for "all hazards" reasonably anticipated for those work activities.
Initially, these six-level classification systems may seem to make the job of selecting chemical protective clothing more difficult. That job has always been difficult. These classification systems give structure and objective measures to the selection process. If you have garments that already perform adequately, have your vendor map their performance back to a specific Type or Category. Don't take your vendor's word for it -- make them show you how the garments compare to the requirements. Going forward, it will be easier to communicate with your vendors, once we all talk the language of Type/Category and Class/Level.
This article originally appeared in the August 2011 issue of Occupational Health & Safety.