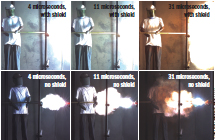
Page 2 of 4
Arc Flash Training & PPE Protection
I received a call recently from a large electric
utility. A line worker, we'll call him Bill, had
been badly burned while performing work near
a 69kV piece of equipment. This incident illustrates
several issues that a safety professional or engineer
must consider in development of an electrical
safety training and PPE program, two of which are
not directly addressed in regulations or the consensus
standards. Thinking through a clothing system and
electrical safety program can save money and make
compliance easier and more effective.
The worker was in a 50 cal/cm2 rated winter suit.
The undergarments and outer garments were provided
by the company, but workers were given a lot of
latitude on undergarments as long as the outer shell
was compliant with the company's clothing policy.
The worker chose not to wear an arc-rated sweatshirt
even though this was commonly available in
the company's clothing catalog. Instead, the worker
was wearing a non flame-resistant T-shirt under the
sweatshirt. Though this system was in compliance
with NFPA 70E, NESC, and OSHA 1910.269, it was
not the best choice for the worker. Commonly when
doing assessments for electric utilities or any electrical
installation, companies will consider the OSHA
standards and the latest consensus standards such
as NFPA 70E and the NESC; in addition, the most
diligent companies will have their engineers or a contractor
perform detailed arc flash studies and label
equipment. Yet many companies do not thoroughly
think out their full program. This article will introduce
you to a few new things you can consider to help
go beyond standard compliance to a better-thoughtout
approach to arc flash hazards.
Understanding Arcs
When engineers talk about electric arc nowadays they
teem with enthusiasm. Many have popped up shingles
on the Internet touting their expertise in arc flash.
Most are not experts and often have little more than
exceptional knowledge of electrical theory and software
predictors. Clothing companies consider themselves
experts, too, but few really are and the vast majority
are blinded by their product mix focus. Having
internal experts is a great idea, and such professionals
should direct the internal game; getting training and
having periodic external expert program audits and
periodic system assessment audits will bring much
to improve even the best program. Equipment and
clothing vendors are a nice free source, but an independent
auditor will see things these folks will miss
and his value often will be a life-saving program tweak
that may have little or no cost.
An electric arc is a complex phenomenon that is
just being better understood in the electrical world.
The effect on clothing is interesting, and the field of
research is growing in many ways that are not getting
much publicity but that can affect the effectiveness of
your arc flash program. Usually in the popular literature
you will hear of two types of arcs, but there are
actually four types of arcs and the last two are rarely
considered in arc hazard assessments and only cursorily
addressed in the arc flash calculations.
The four types of electric arcs are:
1. Open air arc (this is the primary arc used in arc
testing)
2. Arc-in-a-box (this is used in one form for arc
testing in the EU)
3. Ejected Arc (when arc plasma hits the worker)
4. A tracking arc (most common at higher voltages,
arc plasma conducts on skin or through clothing)
Only the first two are considered in the calculations
and standards. The open air arc is well understood.
In lab testing, we control movement of the arc
for the sake of repeatability, but in real life from 480V
higher the open air arc can quickly turn into an ejected arc or a tracking arc. The tracking arc is
most common at very high voltages or during
an electrical contact. This is the arc type
that caught Bill. The standards and calculations
didn't offer Bill the best protection,
which would have been arc rated garments
over his whole body. Obviously, Bill broke
several company rules that would have prevented
this injury entirely and the company
isn't to blame, but to make a program more
"forgiving" of worker mistakes, arc rated
clothing on the whole body makes the most
difference.
Toward Better PPE
In doing arc flash calculations, some of the
effects of the ejected arc will be accounted
for by default. The IEEE 1584 equipment
configurations account for some of this
type of arc, but the tracking arc is totally
unaccounted for, even in the literature. I
recently had a utility company safety person
in a heated meeting tell me that NESC
doesn't require them to consider it at all.
This is a misunderstanding of how standards
work and their intent. Certainly one
would like simple, definable compliance to
a known standard, but OSHA standards
do not require you to only consider certain
defined hazards but to attempt to protect
from all "recognized hazards" even if they
are not easily definable.
Dr. Tom Neal of Neal Associates Ltd.
and Michael Lang of Ferraz-Shamut have
introduced us to "ejected arcs" in several
IEEE papers in the past two or three years,
but this hasn't gained much momentum
(Dr. Neal and I have an ASTM F18 taskforce
working on a test to measure this effect).
The new ASTM F2676, of which I am
taskforce chair, uses an ejected arc to rate
blankets for their resistance to arc plasma
in a defined current over time. This revolutionary
standard, developed by the ASTM
F18 committee, might enliven research for
better arc flash clothing, protective blankets,
shields, and even dramatically safer equipment.
Research using this model could also
lead to a more realistic model of arc flash
calculations (it is not the intent of the author to disparage current calculation techniques
but to help spur research using ideas
gleaned from the leading edge of clothing
testing). Dr. Neal and Lang's papers have
opened a new insight into PPE that could
lead to much better PPE and less arc flash
energy.
Researchers in ASTM have long known
PPE performs differently at different amperage
exposures. Lower amperages and
longer exposures create the same total energy,
but the PPE response is dramatically
different. Plasma ejection is usually a lower
part of the total energy in a lower amperage
arc such as the 8000 amp arc used in
the ASTM arc testing. Recent testing using
a high-speed camera and the ASTM test
set up indicate that the bulk of the plasma
doesn't reach the mannequin/panel until
the arc energy reaches 10-15 cal/cm2, and
as the energy increases more and more
plasma reaches the test surface. In higher
current arcs more of the plasma reaches
the test surface faster. Recent tests have
shown this at work.
At 10kA an ejected arc plasma cloud,
as picked up on a high-speed camera (see
Figure 24), has reached a worker 34 inches
away in 23 microseconds, while a 20kA arc
has reached a worker at 34 inches in 11 microseconds
and ignited a cotton T-shirt at
that distance in about 15-25 microseconds.
Because of the newer information
coming out all the time, we recommend
including the following steps when performing
an arc flash hazard assessment
and building an arc rated clothing program
that will give better protection from
all four types of arcs:
1. Mandatory clothing for electrical
workers should offer choices, but it should be
clear, enforceable, and adequate for protection.
2. No melting "flame-resistant materials"
anywhere in the system.
3. Use (non-melting) flame-resistant
materials, especially for the upper torso,
including undergarments. Underwear is
a huge issue. I have seen three underwear
ignitions under arc rated outer garments.
4. Think about moisture management
underneath the clothing for worker comfort
and reduction of the risk of tracking arc. Arc
rated T-shirts may eliminate the use of 7-9
oz. outer shells in shirts in the next few
years. Two layers are often more protective
and more comfortable to wear.
5. Use clothing systems that provide arc
rating in multiple layers rather than just a
thick, 8 cal/cm2 shirt. Though compliance
is easier with a single garment, making all
the garments arc rated will almost always
provide better protection.
For more information, visit https://www.e-hazard.com/.
This article originally appeared in the August 2009 issue of Occupational Health & Safety.