Changes are Reducing Accidents
Task-enhancing features are incorporated into many of today's general-purpose gloves to make them perform better in specific applications.
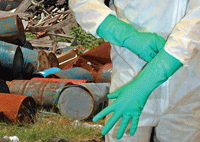
Sharp or rough surfaces/edges, hazardous chemicals, heat, cold, and biomaterials all threaten unprotected hands--and they have for decades. But with ever-changing technology, newer and faster equipment, and emerging health threats, hand protection has never been more important. Fortunately, today's hand protection options are more task-specific, better engineered, and more comfortable than ever before.
According to a recent study, wearing appropriate gloves can reduce hand injury risk by as much as 60 percent. This study was co-sponsored by the National Institute for Occupational Safety and Health and Liberty Mutual, in collaboration with colleagues at the Harvard School of Public Health. The study found the most common occupational acute hand injury to be laceration (63 percent), followed by crush injury (13 percent), avulsion (8 percent), puncture (6 percent), fracture (5 percent), contusion (1 percent), and dislocation (0.1 percent). The study further found that the risk of hand injury was significantly elevated when:
- Equipment, tools, or work pieces did not perform as expected.
- Workers used a different work method or performed an unusual task.
- Workers were distracted and rushed.
Sixty percent reduction in risk (with variance by job category) is an impressive figure in light of Bureau of Labor Statistics reports showing that 250,000 serious hand, finger, and wrist injuries occur in private industry and approximately 110,000 workers with hand and finger injuries lose days away from work annually. On the manufacturing side, glove companies are working hard to develop gloves that not only do the job of hand protection, but also provide the comfort and appeal that helps keep gloves on workers' hands.
Categorizing Hand Protection
Hand protection can be viewed in the broad categories of disposable gloves, chemical-resistant gloves, cut-resistant gloves, thermal gloves, and high-tech gloves. Within these categories there are literally hundreds of variations that make one glove more suitable for a particular task than another. For example, workers handling glass need a different cut-resistant glove than workers handling oily, slippery pieces of sheet metal. Similarly, health care workers have hand protection issues far different from those of food handlers although both wear disposable gloves.
Disposable Gloves Get More Colorful
Disposable gloves (one-time use) are a first line of defense everywhere from the dental office and other health care environments to the SWAT team to the maintenance department. Now these protective gloves are stepping out in colors that range from black for military and police force stealth operations to pink for applications where glove wearers want to express their support of others. Citrus green and vibrant blue also join the traditional mix of white and translucent glove colors.
Depending on the task requirements, nitrile, natural rubber latex (NRL), and vinyl are all effective disposable glove materials. Nitrile is favored for its latex-free composition and solid performance in barrier protection and strength. NRL, although connected with allergy issues, offers strength, elasticity, barrier protection, and skin-like tactile sensitivity. Vinyl is very inexpensive and widely used in food applications where cross contamination to the food is paramount, in comparison with worker protection.
General Purpose Gloves Get Specific
Gone are the days where just any work glove would do. Task-enhancing features are incorporated into many of today's general- purpose gloves to make them perform better in specific applications. Often, these new capabilities are provided by dipping the glove shell in a coating that provides the desired performance.
For example, the addition of spongenitrile coatings facilitates grip in oily, slippery applications, while smooth nitrile coatings provide the dexterity and tactile capabilities needed in assembly.
More and more, popular general purpose gloves are being produced in high-vis colors to make the worker's presence more obvious everywhere, from the construction site to the roadway and the warehouse.
Chemical-Resistant Gloves Stand the Test
Chemicals are a real threat to hands. Wearing the wrong glove when dealing with hazardous chemicals can be disastrous. Research and development departments around the globe work tirelessly to keep glove technology ahead of chemical development.
One of the best ways to ensure the glove being considered for use in a chemical application will provide the necessary protection is to consult an online guide such as Chemrest, which can be accessed at www. showabestglove.com/site/chemrest. This user-friendly Web site contains easy-to-read chemical resistance data from more than 9,000 conclusive tests, including rankings from most effective protection for that particular chemical to least effective, not only for ASTM F739 Method for Heavy Exposure, but also for the often overlooked ASTM F1383 Method for Intermittent Contact with Chemicals—an important factor for many industries.
Cut-Resistant Gloves Take the Edge Off
Special fibers such as DuPont's Kevlar®, stainless steel, and High Performance Polyethelene (HPPE) are key to hand protection when cut threat is a constant. Some cutresistant gloves are offered as liners to be worn under disposable gloves in meat cutting and fishing operations. Others models have grip-enhancing qualities added through the dipping process. The news in cut-resistant gloves is that additional capabilities are being added to the cut-resistant shell to aid in grip and performance.
Thermal Gloves
Workers who handle very hot materials or work in cold conditions need the added protection a thermal glove offers. There are now gloves available that protect hands in temperatures as high as 500 degrees Fahrenheit. On the other end of the spectrum, high-quality thermal gloves offer protection well into minus temperatures.
Proper Fit is a Must
Fortunately for today's workers, there are thousands of hand protection options available to help reduce the risk of hand injury by the 60 percent found in the Harvard study. And, thanks to the diligence of hand protection R&D teams, the options keep getting better.
However, human nature is one element in hand protection that is not changing. The key for everyone is to select the right glove for the job and the right glove for the person. This means not only finding the desired performance properties, but also determining which glove size is right for the individual. To determine proper fit, measure the circumference of the hand around the palm or at the base of the metacarpals. The number of inches will help determine the correct size:
< 7="" inches="Extra">
7.5 inches = Small
8 inches = Medium
9 inches = Large
10 inches = Extra Large
> 10.5 inches = Extra Extra Large
Ill-fitting and uncomfortable gloves seldom get worn as much as they should. A glove that is not worn cannot protect and does nothing to reduce risk of injury.
This article originally appeared in the August 2009 issue of Occupational Health & Safety.