Page 2 of 2
Fit Testing of Hearing Protectors
We live in a world of labels. We trust some labels to be precise: We expect a 250 mg capsule to deliver 250 milligrams of medication, and our 2-liter soft drink bottle undoubtedly holds two liters. But we also accept that some labels provide us only with an estimate: The highway mileage estimate of 32 mpg on a new car sticker is just that--an estimate. The fine print reminds us that actual mileage depends upon our personal usage: If we accelerate faster than the standard 3.2 miles per hour per second the EPA uses to calculate the estimate or if we operate our air conditioner or drive over 60 mph, our actual mileage will vary.
Hearing protectors operate in that latter category of labels--estimates. The EPA-mandated Noise Reduction Rating (NRR), used since 1974, is a population-based laboratory estimate. But there are a number of reasons why a Hearing Protection Device (HPD) fit at the work site might not achieve the same rating as those estimates on the label. Users in the real world might not receive proper training and might fit the HPDs improperly. Users sometimes adjust HPDs for comfort (too loose or a shallow insertion), or they may intentionally compromise the fit in order to hear what they need to hear: co-workers, warning signals, telephones, or communication radios.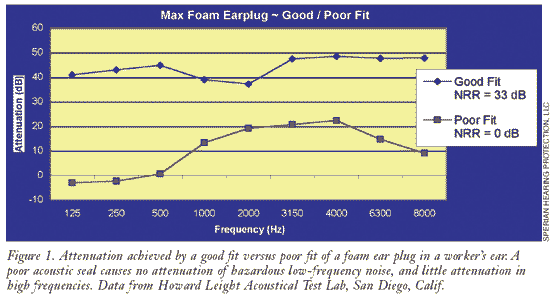
The graph in Figure 1 shows the difference in attenuation between two fittings of the same ear plug in the same worker's ear on the same day, about 10 minutes apart. In both cases, the ear plug was in the ear far enough to satisfy a cursory visual compliance check. To an observer, seeing an ear plug in a worker's ear implies protection. But the mere display of an ear plug says nothing of the protection being achieved by the user. The difference shown in the graph--a good insertion versus a poor insertion--is enough to cause a 30-40 decibel improvement in attenuation at many frequencies when the ear plug is deeply inserted and achieves a good seal in the ear.
Personal Attenuation Rating
Fit testing of hearing protectors in the field has been available for several decades, though somewhat difficult to administer. But current fit test products now allow us to easily measure the attenuation of hearing protectors just as they are being used in the field--for better or worse. Instead of using population estimates on the label, hearing protector effectiveness can be verified at an individual level, ear plug by ear plug and ear by ear.
Several different fit test methods are now available (see "Fit Testing Ear Plugs" by L. Hager in June 2006 OH&S). The oldest method involves a special hearing threshold test similar to traditional audiometric tests, performed in a quiet room, with and without ear plugs. Another method uses a probe microphone, pushed through a small hole in the ear plug, to measure the difference in noise levels on both sides of the ear plug when inserted in the ear canal. The newest fit test method involves a loudness balance procedure performed with and without ear plugs. It can be used with any ear plug in almost any room.
Using this loudness balance fit test, we visited eight different locations to test 104 workers. Locations and workers were not pre-screened. Workers were asked to use the ear plug they typically wear, inserting it in a normal manner. They received no training or coaching as part of the test. The results (Figure 2) show that the distribution of ear plug fit follows a predictable one-tailed bell curve. The majority of workers achieved attenuation within ±5 dB of the published attenuation, regardless of the model of ear plug used. But nearly one-third of the workers achieved attenuation more than 5 dB lower than the labeled NRR. Armed with these individual measurements, a safety manager can target these low performers who are at risk for noise-induced hearing loss.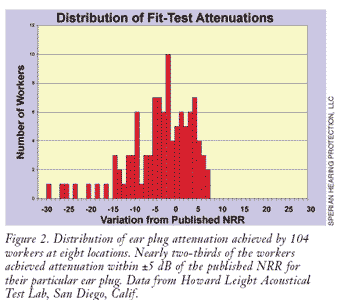
Like a respirator fit test, field verification of hearing protectors provides valuable information, but it also has its limits. Fit testing verifies the capability of an ear plug in the hands of a user. But it only provides a snapshot of attenuation at the time of test; it does not tell us what the noise exposure is for that worker a day later--or even an hour later.
While measuring the attenuation of an ear plug is useful, the most valuable contribution of field verification systems will likely be in employee training. Fit testing of ear plugs provides immediate feedback: Users will know right away whether their fit is good or bad and can make immediate adjustments. And study after study confirms that the best predictor of whether a worker will achieve good protection from an ear plug is one-on-one training, not group hearing conservation training.
Employers also can use fit testing in selecting the proper hearing protector for a new employee. Without objective fit test measures of attenuation, that selection process often reverts to factors that have little to do with hearing loss prevention: color, comfort, or "whatever you have available." OSHA's mandate to offer a variety of suitable hearing protectors to noise-exposed workers in no way guarantees a good fit or adequate protection.
Protecting All Workers
How much noise-induced hearing loss is acceptable at a work site? Even with a Hearing Conservation Program limiting noise exposures to 85 dB, some studies indicate a 10-15 percent increased risk of suffering material hearing impairment over a 40-year working lifetime in noise.
When viewing NRR labels on hearing protectors, safety managers should keep the bell curve in mind. Do not assume that an NRR of 30 dB on the label means that all users, or even most users, will achieve 30 dB of protection. Some will achieve more, some less.
In the past, safety managers lacked the tools to individually identify and correct poorly fitted ear plugs. But field fit testing now allows us to verify the amount of hearing protection and take corrective action with those workers who are unprotected. Prevention of noise-induced hearing loss takes place at a personal level, monitored by personal audiometric exams and personal fit testing of hearing protection.
This article originally appeared in the October 2007 issue of Occupational Health & Safety.
About the Author
Brad Witt, MA, CCC-A, is the Director of Hearing Conservation for Honeywell Safety Products, the manufacturer of Howard Leight® hearing protection products. He holds a B.S. in Communication Disorders from Brigham Young University, and an M.A. in Audiology from Northwestern University. For 14 years, he managed a hearing conservation practice in California, providing OSHA-standard services at 175 locations. He has served as president of the National Hearing Conservation Association (NHCA) and has presented more than 250 hearing conservation seminars on behalf of Howard Leight during the past eight years in 18 countries. Contact him by e-mail at [email protected].