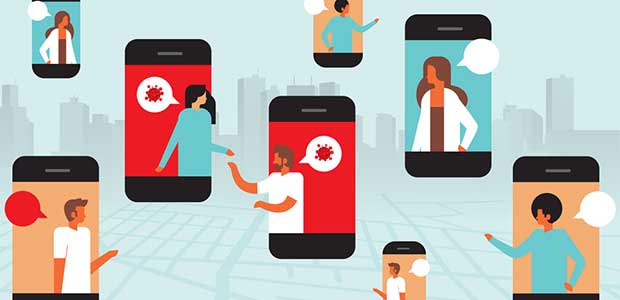
Workplace Safety Technology in the Time of COVID-19
The future of workplace safety post-pandemic will include new technologies, including contact tracing and PPE wearables.
- By Karl Bream
- Jun 18, 2020
The recent celebration of World Day for Safety and Health at Work fell right in the middle of the Covid-19 crisis this year, which got me thinking about the future of workplace safety. Although there are signs that the infection rate is beginning to flatten in most countries, all of the experts agree that we can’t expect to go back to business as usual. We are going to have to adapt our business practices to accommodate the current pandemic, and we have to be better prepared for similar events in the future. As with many crises, this is accelerating the adoption of recent innovations, and this will also be the case for workplace safety.
As the world gears up for re-opening the economy, organizations such as the Center for Disease Control (CDC) in the US and the World Health Organization (WHO), are publishing recommendations for how to operate manufacturing and other business operations while still practicing social distancing and other aspects of workplace safety. These include having office workers telework where possible, staggering shifts to reduce the number of workers using lunch, break and washrooms at the same time, increasing physical space between employees in the workplace, and even downsizing operations if necessary.
Given Covid-19’s ability to be spread by individuals that do not show symptoms, it is generally acknowledged that tracking contacts will be a key way to identify those who might have been exposed to a sick employee. Knowing the cost to the business of having to shut down a facility due to illness, management will need to work with public health authorities to implement practices that allow for the quick identification of suspected contacts, allow for testing and quarantine of workers in the case of an outbreak in their operation and be able to show compliance with these practices.
The technologies needed to do this are not so far away. In fact, they already exist in industries where operating environments have residual risks or require robust control measures in ways that are similar to what will be needed to protect people from contracting the virus. These include mines, nuclear facilities and high-tech chip fabricators. With some adaptation, it is not hard to see how the technologies associated with these industries can be adapted to make the workplace of the future near virus-free.
From a safety management perspective, the ultimate goal is to create a real-time, dynamic picture of what is happening with people, assets and environmental conditions at all times — what is known as ‘situational awareness.’ It is crucial for conducting forensic analysis to understand the pattern of interactions and identify possible transmission paths so as to limit exposure and trigger remediation protocols including testing and quarantining. Much of this already exists, but simply needs to be adapted to the current outbreak.
This full digital awareness of everything going on in the workplace is the main thrust of Industry 4.0, which brings together several technology streams: low-powered IoT sensors, AI and machine learning, edge computing and next-generation wireless connectivity. These technologies combine to allow for the automation of repetitive processes, improved efficiency of operations, preventative maintenance of assets, quality control and enhanced situational awareness.
Applying these technologies to deal with Covid-19 will help to solve many of the new workplace constraints identified above. For instance, there are types of digital smart personal protective equipment (PPE) that incorporate wearable sensors and communications devices. They communicate with the operations control center and can be used to track employee movements, enforce geo-fenced areas deemed too dangerous for entry or sense environmental contaminants and warn employees who have had excessive exposure to leave the area and follow decontamination protocols.
With some small adjustments, smart PPE and wearables could be deployed in many operations to enforce safe distancing between employees, using software to digitally map out work zones. They could warn employees when they are in danger of violating social distancing rules. And they could also enable management to forensically track past exposure of employees to those who have tested positive for the virus.
If sifting through location data for all the employees in a large manufacturing facility or mine sounds like a nightmare, this is where AI comes to the rescue. Sophisticated analytics software already exists that sift through location data to look for correlations. It isn’t much of a stretch to adapt this software to smart PPE data that tracks worker movements in the facility. This kind of software also exists to analyze video footage from CCTV cameras. All of this analysis can be used to prove compliance or trace infection vectors.
One of the important enablers of Industry 4.0 use cases is the existence of highly reliable, secure wireless connectivity. The key to end-to-end awareness of operations is ubiquitous connectivity. Because of privacy concerns, that connectivity should be very secure. To support video and the large amounts of data that can be generated within a fully automated facility, it also has to have bandwidth capacity as well as supporting low latency edge computing. Geo-positioning and geo-fencing services for employees and mobile machines need more precise coordinates than can be provided by GPS.
Delivering all these essential capabilities is fortunately available with today’s 4.9G/LTE and tomorrow’s 5G industrial wireless networks. Early generation wireless technologies, such as Wi-Fi, were designed for connectivity to best-effort networks. They are not highly reliable, secure or capable of providing mobility and geo-positioning services. Cellular-based 4G services, on the other hand, have been used in public mobile networks for a decade and have never been compromised. 5G is designed to be even more secure and has a number of features, like ultra-low latency, that are specifically intended for industrial automation use cases.
Covid-19 is likely to be a reality we have to live with for several years. If we are lucky and develop a vaccine quickly, it may be a short-term problem. But the scientists have been warning us about the possibility of pandemics of this nature for decades. This will not be the last.
The good news is that the same Industry 4.0 technologies that are transforming our workplaces can be harnessed in this fight. Industrial IoT, edge computing, AI/machine learning and industrial-strength wireless networking will play a key role in ensuring the safety of our workers and our ability to come out of this crisis stronger than before.