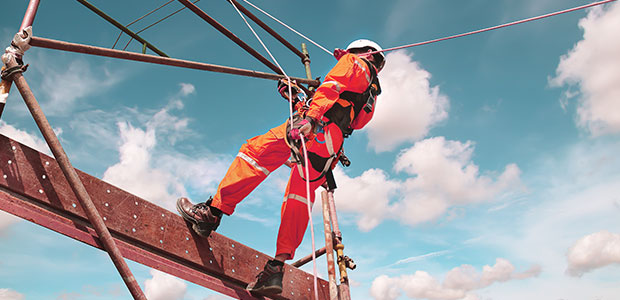
Four Reasons Why Safety Matters in Construction
When it comes to identifying the most hazardous occupations in the USA, working in construction ranks very high on the list. Responsible for 20 percent of work-related deaths in 2013, the construction industry is known to pose several risks for workers in the sector.
- By Lauren Holman
- Dec 13, 2019
When it comes to identifying the most hazardous occupations in the USA, working in construction ranks very high on the list. Responsible for 20 percent of work-related deaths in 2013, the construction industry is known to pose several risks for workers in the sector. It is typical for construction workers to perform their duties off-site or in remote and isolated locations. Not to mention, heavy machinery and equipment are regularly used to perform day to day jobs.
For these reasons, and several more, thousands of construction workers are injured on the job each year, many of whom will never be able to work again due to the severity of their injuries. When it comes down to it, the construction industry is extremely high-risk and therefore requires employers to execute appropriate, ongoing safety measures. In this article, we will point out three main reasons why your construction company should not take safety lightly.
1. The “Fatal Four”
Working in construction creates a very high risk for falling from a height, being struck by an object, electrocution, and getting caught or crushed by heavy machinery. These industry risks are commonly known as the “fatal four.” According to the US Bureau of Labor Statistics, the fatal four were responsible for 57.7 percent of fatalities that occurred in the construction industry in 2013. These risks are even more prevalent for those employees who work alone.
In the construction industry, falls pose the greatest threat to workers. According to EHS Today, this aspect of the fatal four accounts for 37 to 57.7 percent of construction-related fatalities. Furthermore, OSHA reported that in 2010, 402 deaths were due to employees being struck by objects. Lastly, working with or near power lines is hugely hazardous. A tool could explode into liquefied gas in an instant, emitting temperatures up to 19,000 degrees Celsius. Construction workers are incredibly susceptible to burns and other electrical risks in this environment. The last hazard in the fatal four, becoming stuck or lodged, often occurs when construction workers are trenching, as cave-ins are common, and employees can quickly become trapped.
Your organization must have safety measures in place that ensure the safety of your lone workers and minimize the risks associated with the fatal four. This may include regular check-ins or insisting that each worker wears a panic button to signal for help should they need it.
2. Property, Plant, and Equipment
Sometimes, a hard hat or safety goggles just isn’t enough. A surprisingly large number of construction companies solely rely on their PPE to keep their workers safe, and overlook the fact that injuries are still bound to happen. For instance, if one of your employees is a victim to the fatal four, it is unlikely that a hard hat will save the day. Will your company know if one of your workers gets caught under a heavy object, falls from high up, or loses consciousness? If the worker is at a remote site or is alone, the only way of knowing that they are in trouble is by using a lone worker safety monitoring service. In an industry like construction, monitoring your lone workers is necessary.
3. Minimizing Response Times
Does your company have a fail-proof emergency response system in place? What have you done to reduce your response time when a worker needs help? It is essential to acknowledge that the unexpected can and does occur. That is why construction companies must employ proper safety procedures to make sure that they can respond promptly if there is an emergency.
Protocols must be clear, concise, easy to understand, and well-communicated. The best way to promote fast response times is through regular check-ins. If employees are working in an unusually high-risk environment, they can shorten their check-in intervals to let monitors know that they are OK more often. If a worker misses a check-in, monitors will immediately know that something is wrong and can respond accordingly. You can learn more about Proactive Safety measures here: https://www.scatterling.co/blog/a-comprehensive-look-into-proactive-safety
4. Your Business is Ultimately Responsible
Proper safety measures are in place to minimize workplace injuries. However, if your organization does not employ suitable safety measures, you might be breaking the law. This could result in severe fines in the event of an accident or even being prohibited from operating in your sector. If a construction site on which your employees are working does not meet specific safety standards, your company could be taken away from you.
With that said, there are ample long-term benefits to a positive safety culture as well, including heightened morale, boosted productivity, and more satisfied employees. To learn more about understanding safety as an “investment,” visit this Scatterling blog article.
Workers in the construction industry are constantly faced with unique risks on the job. Because of a construction worker’s high rate of exposure to life-threatening hazards, a lone worker safety monitoring service would be hugely beneficial in preserving your workers’ safety.