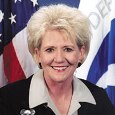
DOT Rule Makes Cheating on Drug Testing Harder
U.S. Secretary of Transportation Mary E. Peters recently announced a new rule that will make it more difficult for transportation workers to cheat on their required drug tests by requiring drug testing labs to analyze every test for tampering.
"We want to make sure there are no doubts about the ability of anyone working in transportation do their job as safely as possible," Peters said. "There is no margin for error when it comes to the safety of the traveling public."
According to Peters, the new rule would cover the nation's approximately 12.1 million transportation employers, safety-sensitive transportation employees, collectors, labs, and medical review officers. She noted that under the terms of the rule, labs would no longer have the option of testing urine samples for signs of cheating, but instead would be required to test every specimen for possible adulterants and urine substitutes.
"In addition, all collectors will be required to put in place new procedures designed to prevent tampering with drug tests," Peters said. For example, observation procedures will include checking employees for items designed specifically to cheat the test. The rule also requires collectors to observe all tests for transportation workers who return to their jobs after a previous test failure. Peters added that the department would treat any invalid test results as the same as a refusal to be tested by any employee who admits to tampering with or adulterating their test.
DOT regulates drug and alcohol testing of safety-sensitive transportation employees in the aviation, motor carrier, railroad, transit, pipeline, and maritime industries. The Drug and Alcohol Testing Final Rule was published in the June 25, 2008, Federal Register. The effective date of the Final Rule is Aug. 25, 2008.