Industrial Noise Control
It's always best to have a qualified acoustician evaluate the problem and make recommendations.
- By Patrick J. Brooks, P.E.
- Sep 28, 2007
In any work environment, there can be many reasons to keep sound levels within a reasonable range. Sound levels above this range are perceived as "noise." Noise can distract the workforce, creating an unsafe workplace. Or, worse yet, it can cause hearing loss.
A worker distracted by noise may become less production and even irritable. If noise levels are too loud, the worker may not be able to hear warning signals or instructions. High noise levels over prolonged periods of time can lead to permanent hearing loss. When any of these conditions exists, it is important to control, contain, reduce, or eliminate the noise source so a safe work environment can be maintained.
To understand how to control noise levels, the reader needs to know some basic fundamentals. For a noise problem to exist, there has to be a noise source, a path that propagates the noise, and a receiver of noise. If any one of those three elements is missing, there cannot be noise or even sound. This gives us a clue about how to control noise problems. By treating any one or a combination of the three elements necessary for noise, we are able to control it. A noise source such as a rough-running generator could be made quieter by tuning it up (treating the source). A barrier could be placed between the generator and the receiver, such that the sound waves cannot propagate to the receiver (treating the path). Finally, the receiver (human ear) could be treated with ear plugs or a headset (treating the receiver). The solution to solving the noise problem often must be engineered to determine the most cost-effective and safe method that allows production to continue with minimal interference.
OSHA's Requirements
OSHA has put new emphasis on protecting workers from hearing loss. Most workers subject to noise should have an annual audiogram. If there is a shift in their hearing threshold relative to their baseline audiogram of an average of 10 dB or more in the 2000, 3000 and 4000 Hz frequency levels, in either ear, the worker must be retested within 30 days and the person must be logged as an injury on the company's OSHA 300 report. If the standard threshold shift in hearing still exists after the retest, (unless a physician determines the standard threshold shift is not work-related) the hearing loss is permanently logged on that year's OSHA 300 report, and the employer must take several steps. Here are some of the most important ones:
• Hearing protection or other means must reduce the noise levels to 85 dBA on an eight-hour time-weighted basis.
• Fit or retrofit the worker with hearing protection and train him in the use of hearing protection.
• Refer the worker to a clinical audiological evaluation that includes an evaluation as to whether hearing protection is aggravating a medical pathology of the ear.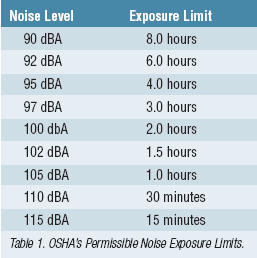
OSHA has established permissible noise exposure limits to help avoid the standard threshold shifts in working. If the noise level exceeds 85 dBA on a time-weighted average, a hearing conservation program is required. The actual exposure limits are given in Table 1. (Review OSHA’s occupational noise exposure 1910.95 for a full explanation.)
What is Sound?
We have already stated that noise is unwanted sound levels, but what is sound? Sound is composed of variations (vibrations) of air pressure above and below local ambient pressure. It is waves of various amplitudes and frequencies. Our eardrums respond by vibrating similarly to these waves. We identity the eardrum vibrations as sound. As sound waves increase in amplitude or pressure, we perceive the sound as getting louder. However, our ears are not sensitive to small variations in pressure. The amplitude, in terms of pressure, has to change in large percentages to be perceived as getting louder, and in general, the units of sound pressure are very small.
A deafening passenger ramp of a jetliner is only about 0.08 inch water column. Therefore, sound is usually quantified in logarithmic decibels instead of pressure units. When converting to decibels, we refer to the units as sound pressure levels. There are standard conversions of sound pressure to decibels, but the output of sound meters is in decibels, so for this article we won't worry about the conversion. However, that same passenger ramp of the jetliner at 0.08 inch water column pressure is equivalent to 120 decibels (dB) of sound pressure level.
The other important component of sound is frequency. A very rapid or short sound wave is perceived as high frequency, measured in cycles per second of vibration, or hertz (Hz). A very low rate of vibration or long waves is heard as low frequency. A young person with excellent hearing may be able to discern frequencies below 20 Hz and above 20,000 Hz. As with sound pressure, though, our ears are not linearly sensitive to frequency. We generally talk about hearing and controlling sound by octave bands. The normal eight octave bands we hear are defined at the mid-range of each frequency range, and each subsequent octave band is a doubling of the frequency range of the previous one. The octave bands for the frequency range normally associated with hearing are given in Table 2.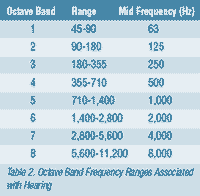
Our ears are most sensitive to the sound in the 5th, 6th, 7th, and 8th octave bands. People perceive these frequencies to have loudness equivalent to lower frequencies, which are at higher actual sound pressure levels. This concept is often called "equal loudness."
One common way of applying the equal loudness concept is to present the total effective level of sound in the audible frequency range as a single A-weighted sound level. When this is done, the decibel level of a sound's frequency components below 1000 Hz are weighted to lower values (de-emphasized) to compensate for the reduced sensitivity of the human ear to low-frequency sound. An A-weighted overall sound level provides a single number rating that is commonly accepted as representative of the perceived loudness of the sound if it were at low to moderate overall sound pressure levels. A-weighted sound levels are common design goals in occupational and outdoor noise control projects. When sound is A-weighted, it should be denoted by the unit dBA.
If you believe you have noise problems, then a qualified acoustician should be used to measure the sound levels. The sound is measured where the worker will be exposed to the maximum level for that period of time. This is done on an eight-hour basis if the sound level varies throughout the day. A sound level meter can measure instantaneous sound levels, but to properly measure noise over time, an audio dosimeter should be used.
An omnidirectional microphone is used on all dosimeters. The microphone responds to dynamic pressure variations, with the output being an electrical signal proportional to the sound pressure. The output signal of the microphone is fed into an attenuator and A-weighted network.
The dosimeter must calculate C/T ratios equivalent to those obtained by using a sound level meter, where "C" is the actual exposure time at a noise level and "T" is the permissible exposure time at the noise level as defined in Table 1. The measurements are taken for eight hours, so the dosimeter must integrate over the total eight-hour shift.
Solving Noise Problems: Three Approaches
A number of factors determine the best noise control measure. They are:
• Financial and technical feasibilities
• Safety
• Maintenance accessibility
• Minimum allowable disruption time for a particular production operation or process
As previously discussed, the source, path, or receiver can be treated.
Source Control
Noise radiates from a source. For projects in the design stage, try to specify the quietest operating equipment you can. This may not eliminate all potential for a noise problem, but it will make the noise control project easier and less expensive to implement. Buyers should be aware of and consider the noise level when making new equipment purchases.
When a noise problem already exists, it is unusual that the mechanisms or processes that generate the noise can be quieted. In these situations, adding acoustical materials to the noise-radiating surfaces may help reduce the noise strength at the source, either eliminating the noise problem or partially controlling the problem. The materials that are added in these situations may provide sound absorbing, sound blocking, or damping properties (or any combination of these three properties). Particularly in industrial noise problems, compressed air discharge noises are easily treatable with the addition of pneumatic silencers.
Path Control
Noise is transmitted via sound waves through the space that separates the source from the receiver. Altering the path of this transmission to reduce the amount of acoustical energy that will reach a receiver is an effective approach to industrial noise control. Usually, this involves impeding the sound transmission by interfering with its reflected and direct paths.
Reflected noise paths can be reduced by adding sound-absorbing panels to walls and by hanging sound-absorbing devices (unit absorbers) from ceilings. Direct noise paths can be disrupted by using enclosures or acoustical barrier walls between the source and receiver. These barriers are most effective when used in combination with materials designed to treat reflected sounds.
Receiver Control
Ear plugs or ear muffs are considered highly economical methods for reasonably effective receiver noise control. However, employees are often uncomfortable having to constantly wear these devices. They also note their inability to detect changes in the sound of equipment and problems in communicating with other employees. In environments with a lot of material handling equipment, such as forklifts, the use of hearing protection devices can create unsafe working conditions because employees may not be able to hear equipment entering their work areas. Quiet zones or personnel enclosures are preferred to reduce the noise level that reaches the receiver.
The Use of Enclosures
Maximum noise control is provided by quality sound enclosures because they normally include materials and design features that provide sound absorption, transmission loss, sealing, and ventilation in one system. Noise is blocked from either leaving or entering the enclosure. This provides the option of enclosing either the noise source or the noise receiver.
Proper sealing is required for an enclosure to maintain its acoustical integrity. Access doors, windows, and ventilation systems can pose special problems. Doors, windows, and structural joints must be properly sealed and caulked to ensure no sound leakage, in or out, occurs to degrade an enclosure's performance. In cases where a manufacturing process requires materials to be constantly moved in and out of an enclosure, acoustic tunnels or shields must be incorporated into the design to ensure acoustical integrity. The enclosure's ventilation system also may require adequate silencing of the inlet and outlet paths.
Typical Noise Control Results
Figure 1 and the illustrations from Figure 2 demonstrate the relative noise reductions and methods that can result when various basic noise control measures are applied to a typical industrial noise problem. In this case, the machinery did not generate any significant noise at frequencies below the 500 Hz octave band.
Summary
Only option E reduced the overall A-weighted level to less than 90 dBA, and in fact, it reduced it to less than 85 dBA, the level at which OSHA requires a hearing conservation program. Thus, a worker could be exposed to the resulting sound level using option E for up to eight hours.
The results of all of the other measures required limited exposure, according to Table 1. Untreated (and without hearing protection), the worker could be exposed to the 112-dBA sound level for only about 15 minutes during the day. Option B would allow the employee to be exposed to the 105-dBA sound level for one hour; Option C of 98 dBA for about 2 hours; and Option D of 91 dBA for about 7 hours. These times assume the worker is not exposed to other high noise levels; otherwise, these have to be accounted for, as well.
The best solution depends on how long the parts tumbler is in operation and whether barriers or enclosures are practical. Other solutions may exist, as well. It's always best to have a qualified acoustician evaluate the problem and make recommendations.
References
1. Acoustical Engineering Report, Number 4, Applying Acoustics--Part 1, McGill AirSilence LLC, 2005.
2. "Noise Dosimeters: Past, Present, and Future," by Dennis A. Giardino and John P. Seiler, Pittsburgh Technical Support Center.
3. OSHA 29 CFR 1910.95, Occupational Noise Exposure, U.S. Department of Labor.
This article originally appeared in the October 2007 issue of Occupational Health & Safety.