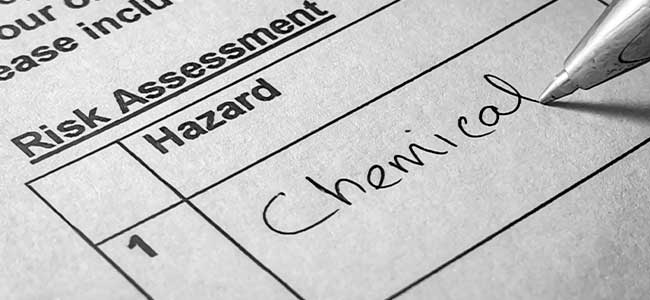
How to Harness Hazard Communication Training
There are multiple benefits of hazard communication training. What are they and how do you get started?
- By Gen Handley
- Aug 01, 2023
All of us, regardless of industry, face safety hazards at work. Some are obvious like heavy machinery or working from tall heights, while some are less obvious such as workplace violence and biological hazards including viruses or dangerous wildlife. Yes, some are more dangerous than others, but they are still occupational hazards nonetheless and must be communicated to those affected, promptly and properly.
What is hazard communication?
This is where hazard communication—as well as the training and education of employees around that very important communication—comes in. By most definitions, hazard communication is a standardized language and/or processes that notify employees about occupational hazards, particularly toxic chemicals and substances.
OSHA’s Hazard Communication Standard (HCS) requires employers to educate workers about the identities and hazards of specific chemicals, including labels and safety data sheets, as well as safety training on how to handle chemicals properly. Hazard communication is based on a set of internationally recognized pictograms, as well as hazard statements and warning words; it’s aligned with the Globally Harmonized System of Classification and Labeling of Chemicals (GHS).
What is hazard communication training?
In order to best ensure that a company’s employees understand hazard communication, provide thorough training to all people handling or working around dangerous chemicals. OHSA states, “Employers are required to train workers on the new labels elements and safety data sheets format to facilitate recognition and understanding.”
Additionally, under Standard 1910.1200 - Hazard Communication, OSHA says the employer is responsible for developing a hazard communication program which can include:
- List of hazardous chemicals currently in use
- Chemical container labels, stickers and decals
- Safety data sheets
- Training programs about chemical hazards and protective measures
What Are the Benefits?
There are many benefits of hazard communication training:
Improved Occupational Safety. The most significant and obvious benefit of hazard communication training is increased protection of employees by improved handling, storage and transportation of dangerous chemicals at work. This educates team members on how to work with and around certain chemicals so that they are not harmed—to proactively take measures in chemical handling and storage now so that accidents don’t happen in the future.
Strengthened Internal Communication. Training improves communication between employees and reduces accidents because everyone is speaking the same language, so to speak. Using an internally recognized set of pictograms and language to communicate hazards about chemicals, prevent any confusion, misinterpretation, and as a result, harmful accidents or mistakes.
Enhanced Emergency Response. As much as we try to prevent accidents from happening, they sometimes inevitably occur, no matter how much preparation we perform now. When they do occur, as in a chemical spill or release, employees trained in hazard communication will be able to respond faster and in a coordinated manner as they are all speaking the same language and using the same information.
Boosted Compliance. Additionally, training keeps the organization compliant with OHS legislation and regulations, preventing harmful injuries and litigation. It helps satisfy OSHA’s hazard communication standard of providing training and education about chemical hazards and protective steps that can be taken now. Make sure you remain up-to-date on local safety legislation, regulations and industry standard.
Hazard Communication Program
Hazard communication training can fall under a hazard communication program, which, as you will see below, entails a few more important elements that will benefit your team’s safety.
Start with a chemical hazard assessment. One of the first steps you need to take when developing a hazard communication program is to perform a chemical hazard assessment of your work environments. In occupational health and safety, a hazard and risk assessment is a document that exhaustively outlines all of the dangers your people are facing while on the job—chemical as well as physical, ergonomic, biological and psychological hazards. Once you’ve identified the chemicals and the occupational hazards they include, you can then look at strategies to help your employees work around them.
Some of these strategies include simple, safe practices that can be implemented into regular operations and schedules:
- Daily clearing of work areas and walkways
- Visible, posted instructions on proper cleanup for specific chemicals
- Regular maintenance/updates of chemical cleaning supplies and equipment
- A well-researched and consulted emergency action plan
- Hazardous chemical usage limits or alternatives
Overall Hazard Communication
Chemical hazard communication training is a part of your greater OHS program and protocols that address the overall safety and well-being of your people. Hazard communication and training your employees about it are part of a healthy communication culture where there can be less accidents as well as increased productivity and quality of work.
Look at how you educate your employees about other occupational hazards, identifying opportunities to integrate or leverage other available channels for hazard communication. Are there places you can add pictograms and warnings? Does this information need to be added to other safety materials and resources? Would this be beneficial for HR and onboarding new employees?
No matter what the occupational hazard might be—chemical or psychological—it’s beneficial for everyone when they are clearly communicated, the reason for the training, and how that hazard directly helps them and their coworkers. As mentioned earlier, you want everyone at the organization to be speaking the same safety language and hazard communication will help make that happen.
This article originally appeared in the August 1, 2023 issue of Occupational Health & Safety.