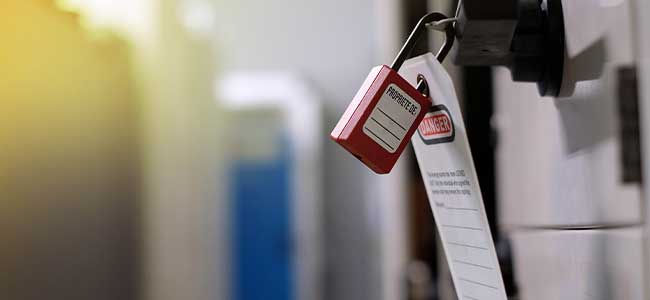
Assessing Alternative Measures
Why a machine safety risk assessment process is critical before implementing alternative measures for lockout/tagout.
- By Steve Misuraca
- Jun 01, 2023
Lockout/tagout (LOTO) is a critical safety procedure that is designed to prevent the release of hazardous energy during maintenance, servicing or repair activities. OSHA 1910.147 requires LOTO whenever an employee enters the point of operation of a machine or danger zone to prevent injuries from the accidental release of hazardous energy.
There is an exception to this requirement for minor tool changes and adjustments, and other minor servicing activities, which take place during normal production operations. These activities are not covered by the standard if they are routine, repetitive and integral to the use of the equipment for production, provided that the work is performed using alternative measures that provide effective protection.
Electronic Controlled Safe Positioning Devices
Electronic controlled safe positioning devices are often used as alternative measures to provide protection when workers perform these types of activities. These devices are tied into the machine’s electrical circuitry through a PLC or safety relay to stop the machine when the device is initiated. Some commonly used devices include:
- Light curtains. These devices use a series of infrared beams to detect the presence of objects in a specified area. If an object interrupts the beam, the light curtain sends a signal to the machine or equipment to stop moving.
- Laser scanners. Like light curtains, laser scanners use laser beams and are programmed to detect the presence of objects in a specified area. If an object is detected, the scanner sends a signal to the machine or equipment to stop moving.
- Pressure-sensitive mats. These mats are placed on the floor and are designed to detect the presence of a worker by the pressure applied from stepping on the mat. If a worker steps on the mat, the machine or equipment is automatically stopped.
- Interlocks. Interlocks are mechanical devices that prevent a machine or equipment from operating unless certain conditions are met. For example, an interlock may prevent a machine from operating unless a guard is secured in place.
Ensuring the Best Option
However, before implementing these types of measures, an evaluation must be done to ensure the measure is the best option for the hazard and that any residual risks have been accounted for. We are depending on alternative measures to perform as effectively or better than applying LOTO for the same exact task.
Take for instance a large stamping machine that has a powered coil infeed area on the backside of the machine. Within this coil area, there are multiple rotating equipment hazards, in going nip points and access to the stamping press die. The coil area is guarded by fencing with an interlocked door that shuts down all machine movement when the door is opened. The operator must enter the coil feed area routinely to manually adjust tension on the coil feeder.
The alternative measure for the task is utilizing the interlocked door to shut down the hazardous energy when the operator enters the area. But how do we know that we can rely on the interlock system to fully protect the operator from the machine hazards in this situation?
We need to consider things like the dependability of the safety system components and the stopping speed of hazardous motion when the system components are triggered. Also, what would happen if the start button on the control panel were initiated by someone else who is unaware that the machine operator is behind the machine in the coil feed area?
A thorough review and analysis must be done to identify and evaluate all potential failure modes for the alternative measures we are utilizing.
Risk Assessment Under ANSI
Section 8 of ANSI/ASSP Z244.1-2016 The Control of Hazardous Energy, Lockout, Tagout and Alternative Methods covers alternative measures including evaluating and reliability and effectiveness of alternative measures. Section 8 of this standard also specifies that alternative methods to lockout or tagout shall be based on a risk assessment that identifies the hazards associated with the tasks to be performed.
Risk assessment methods can be found in ANSI B11.0, ISO 12100, ANSI/PMMI B155.1, ISO 14121-2, SEMI S10, ANSI/ASSP Z10.0 and others. However, the key elements of a risk assessment include:
- Prepare for/set limits of the assessment
- Identify tasks, elements of each task and hazards
- Assess initial risk
- Reduce risk
- Assess residual risk
- Achieve acceptable risk
- Validate solutions
- Document the process
When considering safety-related components of control systems utilized in devices for alternative measures within the scope of a risk assessment, as the risk increases the architecture/structure requirements shall also increase (from single elements to redundancy, monitoring and self-checking). The higher the risk of harm, the more robust the architecture/structure required. ISO 13849-1 Safety of Machinery – Safety related parts of control systems: Part 1 – General principles for design provides information on performance and reliability of these types of systems and must be incorporated into the machine risk assessment where applicable.
In summary, before implementing alternative measures for LOTO, a machine safety risk assessment process must be completed to ensure that the measures are effective and residual risks associated with the measures have been identified and evaluated for potential failure modes.
Risk assessments should be performed by qualified persons who, because of training and experience, understand and demonstrate competence with the design, construction, operation or maintenance of the system and associated hazards.
This article originally appeared in the June 1, 2023 issue of Occupational Health & Safety.