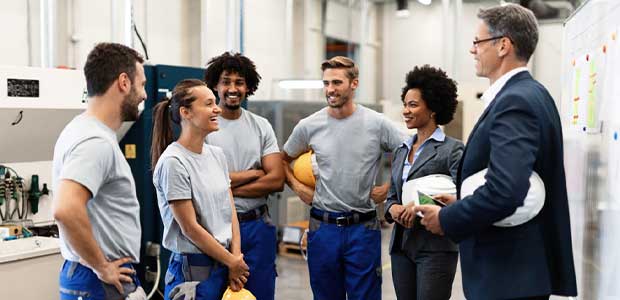
Discovering the Real Problem in Health and Safety and How to Solve It
Leaders at all levels should lead by example.
- By Jules Reed
- Aug 09, 2022
I have worked in health and safety for around 20 years in local authority, construction, rail and utilities. My background was in teaching, applied behavioral science and H&S. Combining these disciplines, I created and delivered several Behavioral Safety Programs. However, the more I listened and understood about safety and the obvious divide between managers and the workforce, the more I realized that the issues were much deeper than just behaviors.
There were clear patterns in collective thinking, feeling and behaving on both sides that created a cycle of negative actions, interactions and reactions. It was a bit like being in the Matrix, in that I could observe the routines and rituals that were making up the culture, but the people in it could not. The patterns became easy for me to predict, and I realized that they were influencing the way that everyone played their part at every level of the business.
As you can imagine, I wanted everyone to see what I was seeing. It was a revelation that could cause a significant paradigm shift in saving people from harm. All I needed to do was help organizational leaders to change the unhealthy psychological and sociological patterns that sabotaged their safety cultures. However, this proved more difficult than I had anticipated. Leaders generally don’t like to be handed a problem without a solution.
Leadership is the Solution
The problem with most behavioral safety programs is that they focus on the behaviors of frontline managers and the workforce. This is the equivalent of trying to make the tail wag the dog! Actually, the focus must be on the vertical lines of leadership within the organizational structure because they are responsible for creating the underlying patterns that govern the safety culture, which in turn influences safety behaviors.
It is obvious that each leader within the structure has a distinct part to play, and therein lies the first problem because most leaders don’t even know they are in a game. They are mostly unaware of the patterns they are generating. This creates a lack of consistency in leadership and subcultures emerge, which makes the whole culture change issue seem complex. Especially as each leader would need to know how, why and when they are out of sync with the organizational aspiration for safety culture and then would need to know what to do about it.
Pathways to Alignment
The key to developing a mature safety culture in my opinion is the alignment of leadership patterns vertically. The most senior leaders will describe the vision and lead by example, the middle managers will create an environment where the vision is feasible and lead by example and the frontline managers will implement the vision and lead by example.
A word of caution: obvious changes in leadership patterns can be met with suspicion and have a negative effect. Leaders who make small, incremental, stealth-like changes will achieve sustainable results.
Once aligned leaders create an unmistakable and unshakeable pattern that is repeated constantly, it becomes instinctive and intuitive in every employee. It is said that workers provide what they believe their managers “really” want and so the patterns are naturally adopted by the whole organization over time. This is how a psychological nudge into safe behaviors is created by a good safety culture.
Support is Necessary
For me, the main investment to remove outdated patterns and instill new ones is the time and effort of leaders. They must be willing to participate fully in the process of change. This means sustained effort and it is obvious that leaders are not going to keep this up without knowing they are getting somewhere.
About the Author
Jules Reed is Tended’s Head of Behavioral Science. She is experienced and qualified in applied behavioral science, working in high-risk industries to lead culture and behavioral change programs, including HS2, Interserve and Balfour Beatty. Jules is passionate about supporting organizations to achieve a culture of safety, where safe behaviors are second nature.