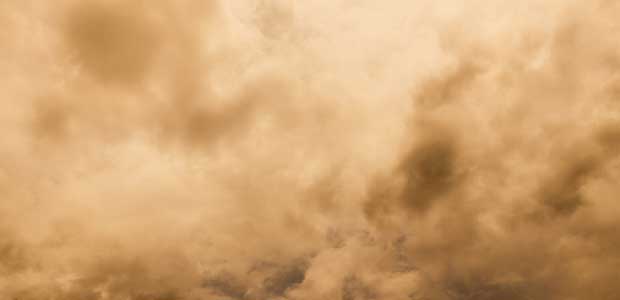
Dust Hazards Analysis and NFPA 652 in Industrial Hygiene Settings
Solely using hygiene measurements to address hazards is not a safe strategy.
- By Zach Hachmeister
- May 01, 2022
Airborne or layers of dust in industrial settings can present a variety of hazards, but the two that are most prevalent relate to the toxicity and explosive characteristics of the material. Both hazards are addressed in different fashions; however, there is some correlation between the two.
For toxicity purposes, government agencies such as the American Conference of Industrial Hygienists (ACGIH) and OSHA have developed threshold limit values (TLV) or permissible exposure levels (PEL) for a wide range of materials. These values set a safe level at which employees can be exposed to specific material over a given amount of time and are usually reported in parts per million (ppm) or mg/m3.
When addressing explosion hazards, the potential for an explosion does not begin until dust concentrations suspended in the air reach a value above the minimum explosible concentration (typically above 20 g/m3). To help put this in perspective, a 25-watt light bulb positioned one meter away would be barely visible in a dust cloud that has a concentration of 60 g/m3. Keeping that in mind, it is also possible to see dust particles suspended in air and still be below the threshold value set by OSHA.
In accident investigations, combustible dust explosions are usually referred to as primary or secondary explosions. A primary dust explosion is one that occurs inside a process vessel such as a dust collector, and the fuel is usually the actual process dust. Secondary explosions often follow a primary explosion. Essentially, the pressure wave from the primary explosion lofts fugitive material previously deposited on overhead surfaces. The lofted material then forms a cloud and eventually finds an ignition source resulting in a secondary explosion. One of the more well-known dust explosions was the incident at Imperial Sugar, where a series of secondary explosions demolished the facility causing over $270 million in damage.
The toxicity and explosion hazards relationship primarily relate to secondary dust explosions and fugitive dust deposits. From a hygiene perspective, an extremely low dust concentration is usually an indication of reasonable dust control, especially if these measurements are taken near process equipment. In addition, reasonable dust control leads to lower fugitive dust deposits, which can alleviate housekeeping duties and ultimately reduce secondary dust explosion hazards. However, solely using hygiene measurements to address dust explosion hazards is not a safe strategy. This is not acceptable because it will not always tell the story of what is on elevated horizontal surfaces such as overhead I-beams or ductwork, walls and elevated surfaces as even very low-level emissions can lead to dangerous dust accumulations over time. It also does not address primary dust explosion hazards, which exist inside process equipment.
To mitigate the hazards associated with dust in the workplace, it is essential to look at hygiene levels and evaluate the explosive characteristics of processed materials. A good starting point is to have dust explosibility screening tests conducted on samples taken from process equipment such as dust collectors or mills and fugitive dust deposits found on elevated surfaces. If the materials are identified as non-explosible, then the primary safety concern may be reduced to toxicity effects. However, if the materials are explosive, the process and facility should be evaluated for dust explosion hazards. This can be accomplished through conducting a Dust Hazard Analysis (DHA). A DHA is a systematic process outlined in the National Fire Protection Association (NFPA) 652 that is targeted at identifying hazards to enable the development of hazard mitigation plans.
In NFPA 652, the term “Dust Hazards Analysis” was introduced when it was initially issued in 2015. This is designed to differentiate from the more complex Process Hazard Analysis (PHA) required by the OSHA Process Safety Management (PSM) program for the chemical process safety industry. Industrial and academic experts in combustible dust, fire and explosion safety guided the formation of NFPA 652. Its purpose is to give personnel a single source for information on the fundamentals of safe handling combustible dust and powders in an industrial setting. The standard also directs users to commodity-specific standards such as the following, which offer material and production-specific guidance:
- NFPA 654 – Prevention of Fire and Dust Explosions from the Manufacturing, Processing, and Handling of Combustible Particulate Solids,
- NFPA 61 - Prevention of Fires and Dust Explosions in Agricultural and Food Processing Facilities,
- NFPA 484 – Standard Combustible Metals and
- NFPA 664 – Wood Processing and Woodworking Facilities
The principles discussed within NFPA 652 focus on fuel containment, controlling ignition sources and limiting the spread of a combustion event by identifying potential risks. These elements can be found by conducting a DHA, which must be revalidated at least every five years or whenever a process change is under consideration. The NFPA is developing NFPA 660, which will make the standard into a code. The separate NFPA sections listed above will be collapsed into one code, NFPA 660.
The requirement established in NFPA 652 is one good reason to complete the DHA, but the safety of your employees and facility should be the primary reason. OSHA currently follows NFPA standards to ensure that a facility stays safe while handling explosible and/or combustible materials. Currently, OSHA will point to The General Dust Clause, Section (a) (1) of the OSHA standard to enforce safety guidelines for combustible dust safety.
This article originally appeared in the May 2022 issue of Occupational Health & Safety.