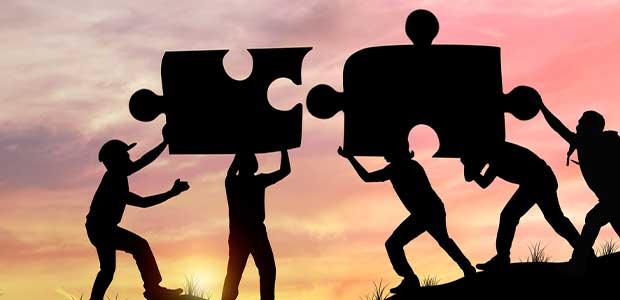
Why Many Change Initiatives Fail to Achieve Expected Results
- By Peter Furst
- Jul 06, 2021
Introduction
Organizations invariably face operational issues where improvement in their product or service is necessary. This can occur in the value, utility or cost of their output, the efficiency of their process and practices, the utility of their systems as well as the performance and behavior of their employees. This results in an analysis of the situation and selection of an intervention which is deployed in order to solve the problem.
It is a given fact that many of the deployed change initiatives fail to deliver improvements expected by the management of the organizations. In fact, in many cases, virtually all changing initiatives applied to every facet of organizational performance fail to deliver on the expected improvement. There are many reasons for the degree of this failure as indicated by the following researched data:
- Up to 75 percent of all change initiatives fail to achieve expected improvement.
- Virtually all change initiatives have inherent problems.
o Most senior managers understood the need for change; this dropped to one half for managers and one third for supervisors.
- Although most companies trained their managers in managing change, only about 20 percent of them felt that the training was effective.
- Only half of employees felt the deployed change initiatives met the initial objective, but less than sone fifth felt gains were sustained over time.
- A third of change initiatives fail due to faulty deployment practices.
Initiatives to improve safety outcomes are even more challenging due to additional factors such as the separation of responsibility, management and control:
- Project supervision is responsible for planning, directing and controlling production as well as quality while the safety manager is responsible for worker safety.
- Most of the construction hazards are created by the natural progression of the work as it is put in place, while safety is responsible to find and have them corrected.
- Production is driven by the schedule while safety is managed by inspections, training and loss data.
- The focus of operations is mostly proactive while safety in primarily reactive.
Traditional Improvement Management
Since most shortcoming regarding the organization’s products or services becomes evident after the work is completed and deployed, management’s focus tends to gravitate to the worker. This is based on the assumption that workers have total control of their action and should be able to deal with the situation and perform their tasks correctly. So, the next logical step is to assume if this person had done things differently the outcome would have been different (acceptable). Therefore, most of the interventions deployed tend to be focused on somehow “changing” the worker’s behavior or work practices, utilizing traditional interventions.
Another contributing factor may be the fact that the cause or source of the problem involves the worker failing to identify the hazard or not properly evaluating the level of the risk of having an unacceptable negative outcome resulting in a discrepancy, injury or loss. This also causes management to look to the worker as the place in need of intervention. The traditional approach is to provide training as a first step.
A third area that may need to be addressed involves the failure of the intervention deployed to improve the worker’s performance. This could indicate that the focus of the intervention was wrong or that the change initiative process as well as the roll out is not properly planned, implemented and managed, which accounts for more than 30 percent of all change initiatives launched failing to garner any results and up to three quarters of all change initiatives failing to achieve some or many of their intended or anticipated outcomes.
This obviously requires the identification of the appropriate area(s) which requires improvement and a well devised and robust change initiative properly deployed and implemented. Change initiatives invariably have downsides. Employees generally do not like any form of change. Change may cause stress or some form of “pain” through uncertainly, lack of clear information, disruption of the work routine, misunderstanding of the potential impact on the work, etc. A significant amount of the unnecessary disruption, distress or distraction can be avoided. Some of the possible factors impeding the successful implementation of change include:
1. Failing to articulate a compelling vision
2. Not devising an integrated strategy
3. Failure in creating a powerful guiding coalition
4. Allowing the continuation of worker complacency
5. Failing to identify and remove barriers to excellence
6. Allowing the normalization of deviations
7. Failing to create short term achievable wins
8. Ignoring workplace politics and relationships
9. Failing to implement systems to sustain the change
10. Failing to properly empower and enable employees
11. Gathering and evaluating all relevant metrics
12. Failing to change the climate and culture
13. Elimination of dysfunctional behaviors
14. Claiming victory too soon or rushing the process
15. Avoiding uncertainty and dealing with resistance to change
16. Flexibility to address unforeseen impediments
17. ID a champion to oversee and guide the process
18. Open and continuous communication
Besides these and other possible impediments to improving processes and procedures, management must implement a means for measuring the progress and/or gains in the ongoing improvement in order to keep the focus on continual improvement.
The Improvement of Safety Outcomes
Change initiatives in construction safety usually are implemented after an annual evaluation of the past year’s loss statistics. This may be triggered by the renewal of the worker’s compensation insurance policy. The broker or carrier’s representative may sit down with their customer and report on the status of their losses during the past year and may offer some suggestions as to how to control the company’s rising cost of insurance, which is affected to some degree by the number (frequency) of accidents and to some extent by the severity of the losses.
It may also be triggered by a serious accident or too many similar unsafe physical conditions or unsafe acts by workers identified during the safety manager’s worksite inspections. The safety manager is then tasked with coming up with a plan of how to reduce the accidents or unsafe situations on site. The typical interventions are mostly focused on the worker and include training or retaining as well as more inspections with emphasis on particular behaviors or conditions implementation of an incentive program or emphasis on disciple.
These interventions have been tried since the inception of workers compensation requirements by law, as well as the passage of the OSHA act. Though some improvement has been achieved, hundreds of workers are still getting killed and thousands get injured every year in construction alone-- ten times that in all industries. The underlying problem is in the bifurcated approach to managing operations separately from that of safety.
Conclusion
Every organization is unique. Invariably, they all need to make corrections or changes to various aspects of their business or operations in order to address changing conditions or situations, as well as meet customer dynamic expectations. They have system (means & methods) which enable their employees to create their products or services. The workforce is managed by supervision and lead by managers.
This creates the work environment which affects the employee’s perception of the organizational climate as well as its culture. For any change initiative to be successful all these factors must be taken into consideration in order to devise and implement improvements which are effective, robust, result in significant amelioration as well as sustained over the long haul. For solutions to this problem, see my upcoming article on “Avoiding Change Initiative Failures.”