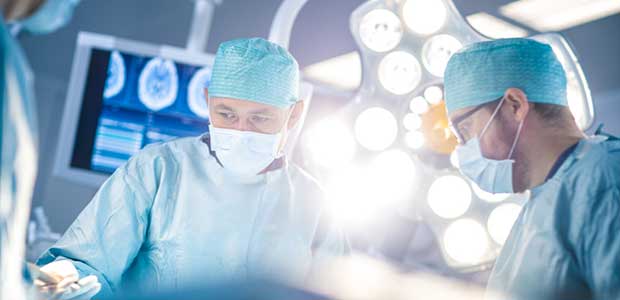
Energized Work in Healthcare Facilities is a Risky Business
The extreme risks of uncertainty may be something you never thought to think of.
- By Corey Hannahs
- Jun 01, 2021
Managing day-to-day operations of a facility is a big responsibility and requires having your finger on the pulse of everything going on in a single building or a full campus. Any flatlines in the inner workings of a healthcare facility system could have a deadly effect on its overall ability to function properly. One such example of a critical system that can impact a healthcare facility is the electrical system. This system provides not just basic power but also supplies power to items considered critical to human life such as ventilators and defibrillators.
Because the stakes are so high within healthcare facilities, decision makers must be strategic about not only what work gets done on the facility electrical system, but also how the work gets done. Even prescheduled and planned work can lead to unintended power outages with unknown durations that can weigh heavily on the needs of the facility. Managers of the facility must weigh every potential risk when making determinations as to how the electrical system is serviced, modified or upgraded. With power availability being closely tied to a healthcare facility operating flawlessly, a common decision that a facility manager must make is whether or not electrical work should be performed in an energized state.
Is it Necessary?
Energized electrical work, or “hot” work as it is often referred to within the trade, is an extremely risky proposition that should not be taken lightly. While de-energizing a part, or all, of the electrical system can often be considered an inconvenience, healthcare facility managers must consider all risks involved when determining a course of action. An important thing to consider when it comes to determining if energized work is necessary is that a coordinated and planned electrical power shutdown is much easier to manage than an unexpected power loss that happens while energized work is being performed.
Determining the areas of impact for an electrical shutdown ahead of time allows you to move the necessary chess pieces around because you know exactly what you’re dealing with, and it allows the technician to keep doing the work safely because it is being done in a de-energized state. Performing energized work leaves your facility susceptible to unplanned outages and can leave you scrambling to determine how to resolve power distribution issues throughout.
What Are the Requirements?
Looking at OSHA regulations around energized work, standard number 1910.333 speaks to de-energized parts. Section 1910.333(a)(1) states, in part, “Live parts to which an employee may be exposed shall be de-energized before the employee works on or near them, unless the employer can demonstrate that de-energizing introduces additional or increased hazards or is infeasible due to equipment design or operational limitations.”
While some decisions that facility managers need to make lie within a gray area, this one is pretty black and white. If a manager is considering energized electrical work being done within their facility, they must: ensure that they can clearly demonstrate that by de-energizing, there would be an increased risk to the individual who is working on the system or show that it would be infeasible to de-energize based on equipment design or operational limitations. If either item cannot clearly be demonstrated, then continuing to allow energized work to be done on the system is, simply put, breaking the law.
What’s Next?
If we review the OSHA requirements and determine that we do indeed have justification to perform energized work, what are the next steps? Reading further into OSHA standard number 1910.333, section 1910.333(a)(2), it says that if the work is to be done energized, as determined after considering section 1910.333(a)(1), then “other safety-related work practices shall be used to protect employees who may be exposed to the electrical hazards involved.”
Section 1910.333(c)(2) further states that work on energized equipment shall only be done by qualified persons. Where in OSHA standards does it say what the safety-related work practices that we must utilize are when exposed to electrical hazards? It doesn’t. That is where a document such as NFPA 70E Standard for Electrical Safety in the Workplace comes into play. The purpose of NFPA 70E is to provide a practical safe working area for employees relative to the hazards arising from the use of electricity.
From a safety-related work practices standpoint, OSHA standards tell you what needs to be done and NFPA 70E tells you how it should be accomplished. OSHA standard number 1910.333 contents can be seen as a nearly mirror image within NFPA 70E section 110.4 dealing with energized work with both documents only allowing for energized work only where de-energizing would pose and increased risk or infeasibility. NFPA 70E section 110.5(H) provides a Risk Assessment Procedure as follows:
1. Identify hazards
2. Assess risks
3. Implement risk control according to the hierarchy of risk control methods, which are listed in order within section 110.5(H)(3) as:
Elimination, Substitution, Engineering controls, Awareness
Administrative controls and PPE
Where Does PPE Fall In?
It is extremely important to note that based on this hierarchy, PPE should be the absolute last resort before energized work is performed. PPE does not free you from exposure while performing energized work. In reality, PPE only helps to minimize results from being exposed to the hazard. It does not prevent exposure in its entirety and even when wearing properly rated PPE, there is still a significant potential for you to become injured while performing energized electrical work.
Should you become involved in an incident, such as an arc-flash, PPE gives you a chance for survival yet offers no guarantees. PPE is the last risk control method that should be utilized when energized work is being considered and should be used only when the five prior methods within the hierarchy of risk control have been openly, thoroughly and honestly explored, without utilizing the all-too-common excuse of the “inconvenience” of de-energizing power.
Is it Worth the Risk?
As a facility manager, controlling risk is inherently within your job description. There is some level of risk to every decision you make. When the facility you manage is in the business of healthcare, the stakes are even higher. Performing energized work within a healthcare facility not only exposes the life of the people performing the actual work but the lives of many others, as well. Any incident, such as an arc-flash, can severely injure the worker and would likely cause the loss of power to other areas within the hospital like emergency bays or critical care units. Is it worth the risk?
While de-energized work may require more forethought, planning, difficult conversations and temporary aggravation among staff, making the effort to go through this process will minimize risk. While the coordination of de-energized work may sometimes lead us down a more difficult path, the steps we take will ensure that we arrive at the right destination.
This article originally appeared in the June 1, 2021 issue of Occupational Health & Safety.