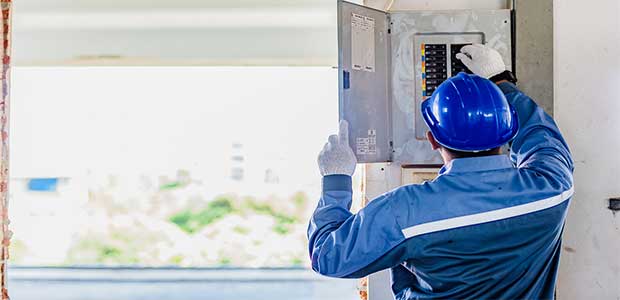
The Bottom Line on Absence of Voltage Testers: How AVTs Allow Us to Engineer Safer and More Productive Processes
Replacing the Danger of Routine with the Safety of Automation
Imagine you are a mechanic called to get a machine back up and running. Imagine as complex or simple a machine as you like, as long as you imagine all the other employees (and customers and clients and business partners) inheriting this headache if you can’t clear this issue up. As you complete your lockout/tagout protocol, you come to a step where you need to verify the machine is truly powered down, and you need to open an electrical panel to verify that, an action that could expose you to electrical hazard.
To keep yourself safe and avoid an incident, you’re supposed to call in an electrically qualified person to do that for you. As the electrically qualified person knows (and perhaps you, the mechanic, do not), there’s a step required for verifying an electrically safe working condition here, and that’s testing for absence of voltage. That step itself requires its own procedure to complete safely (which you, the mechanic, have had to wait through in the past.)
But you’ve done this all before, and everything was fine. In fact, the last time you fixed this machine, you were commended for figuring it out so quickly and getting everything back online – saving the employees, clients, customers and your boss those headaches. So, you open the panel yourself – and perhaps, we don’t need to imagine the rest.
We’ve imagined this scenario to point out two key benefits of permanently mounted Absence of Voltage Testers (AVTs). Those benefits are: (1) a safer process and (2) a more efficient process. An AVT would quickly allow our mechanic to complete the verification step without exposure and without the need to call an electrically qualified person. While the AVT clearly contributes to cost and risk avoidance, and safety is always the primary concern, it’s important to also focus on the benefits of the more efficient process AVTs allow facilities to build in.
What is an AVT?
Absence of Voltage Tester (AVT) is a permanently mounted test instrument designed to replace the risks of manually testing for an absence of voltage with a handheld device. The AVT is connected at the point of work, automatically completing a series of self-tests and tests that typically require 10 to 20 minutes at the push of a button. An AVT is permanently mounted so the button to activate the device can be pushed without opening the panel to access the test location. In addition to providing test results visually, some AVTs are designed with contacts that would allow the tester to be integrated into a control system.
The Hierarchy of Controls
The more efficient process an AVT empowers won’t matter if it’s not also helping us prioritize safety. To understand why the permanently mounted tester might be safer, it’s worth noting an important concept in safety engineering: The Hierarchy of Controls. Introduced in 1950 by the National Safety Council (NSC), the idea is that some safety measures do a better job at reducing risk, and those measures should be prioritized. A generic example: if there’s something on the floor my friend could trip on, I could put up a warning sign, or I could pick the thing up, so nobody trips over it. Removing the hazard is the preferred control because the sign could be missed or ignored. Or, if I’m the one who put up the sign, I might think I know better and don’t need to pay attention to it and forget to be mindful and trip over it myself.
Although it is done every day, there is risk associated with the process of verifying the absence of voltage with a handheld tester because it exposes the qualified person to electrical hazards. The AVT is an engineering control that helps us control the risk that a qualified person faces by replacing the process with one that requires less exposure. The AVT is higher up the Hierarchy of Controls because it does more than administrative controls and PPE. It gives us more control and more power to stop the event in the first place by reducing the risk an individual faces during the course of work.
The Efficiency of Control
Replacing that process not only reduces exposure to hazards, but it also saves us time. Even more importantly, that time-saving process also eliminates some issues with administrative controls. Let’s say we’re responsible for the facility where our imaginary mechanic works. We might ask ourselves: how do we make sure our mechanic follows the procedure to avoid this incident? That question assumes, however, is a better protocol, or better training or supervision, the best way to keep the mechanic safe this time and every time?
The AVT empowers us to build in a different process, one that helps mitigate exposure to hazards in the scenario. With a permanently mounted test instrument that completes the test in seconds, the mechanic is no longer in a position where worry or hurry comes into conflict with a protocol.
With a simple button-press, this tester, which is built with engineered safeguards, performs its voltage check without the panel being opened. The AVT allows us to create a scenario where the mechanic can complete his or her lockout/tagout safely without waiting on a qualified person, removing the possibility of that process being skipped or performed by someone who is not qualified. We’ve replaced an administrative control with an engineered one.
The benefits of the new scenario are multiplied when we consider how and when the machine should really be put into lockout for many other employees. There may be nightly cleaning crew members that work near the machine or even on parts of the machine itself. The AVT gives us the power to replace the danger of routine with the safety of an automated process engineered with fail-safes.
Engineering for a Better Bottom Line
An AVT allows facilities to do more than replicate the solution above but to design automated safety protocols into new and existing equipment that would be impossible without it. For instance, a cage door or other barrier could be designed with a control that won’t let it open until the AVT has verified the absence of voltage. This allows facilities to plan processes that are safer and more efficient for workers that aren’t electrically qualified.
It also creates more safety for those who are qualified. When troubleshooting or performing maintenance, there may still be a need for handheld test instruments, but the initial test by the AVT allows the qualified person to quickly verify an electrically safe work condition before the panel is open.
The AVT helps facilities increase productivity by building safer, more efficient processes. By reducing the time required for vital safety needs, the workplace is made more efficient and less prone to the failure points endemic to administrative controls. For more information on how AVTs can help your facility design safer, more efficient processes for your facility, reach out to your electrical infrastructure solution partner.