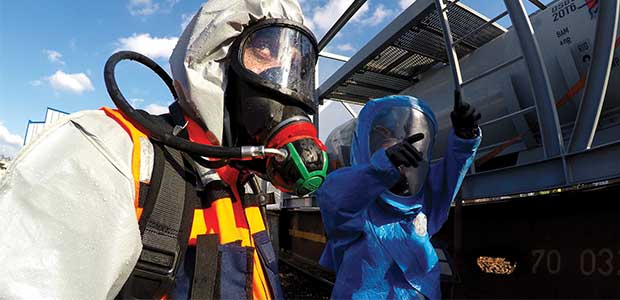
Limiting the Risk of Exposure to Hazardous Materials in the Workplace with the Correct Use of PPE
Consideration of the different variations of PPE and the correct ways to use it are what make the equipment truly safe.
- By Mark Heuchert
- Apr 01, 2021
Working in an industrial environment presents a variety of dangers. One of the most common risks for industrial personnel is exposure to hazardous substances. OSHA defines a hazardous substance as “any biological agent and other disease-causing agent which after release into the environment and upon exposure, ingestion, inhalation or assimilation into any person will or may reasonably be anticipated to cause death, disease, behavioral abnormalities, cancer, genetic mutation, physiological malfunctions or physiological deformations in such persons or their offspring.”
Hazardous substances are present in work environments across a variety of industries, including chemical manufacturing, oil and gas, metal production and more. Some of the most commonly encountered hazardous substances are benzene, arsenic, carbon dioxide, chlorine, sulfuric acid and a wide range of hydrocarbons. When workers come into contact with these hazards, whether it’s part of their daily routine or in response to an emergency, understanding the risks, knowing how to respond and being equipped with the correct PPE is imperative for safeguarding their individual wellbeing and maintaining plant operations and productivity.
To protect workers’ health, prevent accidents and minimize downtime, industrial worksites typically institute strict safety protocols and require constant monitoring of hazardous materials. Such measures include leak detection monitoring, careful cleaning procedures, confined space entry protocols and methods for safely handling and disposing of chemicals, toxins and waste bi-products. Despite this, OSHA’s Top 10 Cited Violations in 2019 still included various hazmat-related infractions, including:
*Hazard Communication (1910.1200) with 3,671 citations
*Control of Hazardous Energy – Lockout/Tagout (1910.147) with 2,606 citations
*Respiratory Protection (1910.134) with 2,450 citations
*PPE – Lifesaving Equipment and Eye and Face Protection (1926.102) with 1,411 citations
Of course, preventing worksite citations is important, but a company’s top priority should always be the health and safety of its workers. To safeguard employees, companies should provide their crews appropriate PPE as well as thorough safety training to ensure they have a sound understanding of workplace hazards and when they might encounter them.
Below are just a few examples of scenarios in which workers might be exposed to hazardous substances:
*When workers need to check device displays in hazardous areas, they can be exposed to increased levels of toxic substances.
*Toxic gases trapped in confined spaces put workers at great risk.
*Handling hazardous substances in labs can lead to short-term, but excessive exposure.
*When handling hazardous materials, opening pressurized valves and connecting hoses becomes especially dangerous.
Selecting the Right PPE for the Appropriate Situation
Because exposure to hazardous materials poses serious health risks, industrial workers must maintain a great deal of knowledge, training and responsibility. However, that alone is not enough—workers also need appropriate and reliable PPE to keep them as safe as possible. It becomes especially imperative, that plant managers thoroughly understand the on-site dangers associated with their facilities and select and stock PPE and detection devices accordingly.
OSHA offers guidelines for selecting PPE, divided into four levels (A, B, C and D), based on operations being performed and risk of exposure. It’s important to note that the guidelines do not fully address the performance of the specific PPE material in relation to the specific hazards at the job site, and that PPE selection, evaluation and re-selection is an ongoing process until sufficient information about the hazards and PPE performance is obtained.
Level A PPE should be selected when the greatest level of skin, respiratory and eye protection is required. This could involve environments where toxic chemicals, noxious gases or airborne particles are present and some degree of exposure is difficult to avoid.
1. Positive pressure, full face-piece self-contained breathing apparatus (SCBA) or positive pressure supplied air respirator with escape SCBA, approved by the National Institute for Occupational Safety and Health (NIOSH).
2. Totally-encapsulating chemical-protective suit.
3. Coveralls.
4. Long underwear.
5. Gloves, outer, chemical-resistant.
6. Gloves, inner, chemical-resistant.
7. Boots, chemical-resistant, steel toe and shank.
8. Hard hat (under suit).
9. Disposable protective suit, gloves and boots (depending on suit construction, may be worn over totally-encapsulating suit).
Level B PPE is called for when the highest level of respiratory protection is necessary, but a lesser level of skin protection is needed. Examples might include workspaces where paint is being sprayed or where toxic vapors could irritate the eyes or nose, but would not cause serious injury to skin.
1. Positive pressure, full-face piece self-contained breathing apparatus (SCBA), or positive pressure supplied air respirator with escape SCBA (NIOSH approved).
2. Hooded chemical-resistant clothing (overalls and long-sleeved jacket, coveralls, one or two-piece chemical-splash suit, disposable chemical-resistant overalls).
3. Coveralls.
4. Gloves, outer, chemical-resistant.
5. Gloves, inner, chemical-resistant.
6. Boots, outer, chemical-resistant steel toe and shank.
7. Boot-covers, outer, chemical-resistant (disposable).
8. Hard hat.
9. Face shield.
Level C protective equipment is appropriate in environments where concentrations and types of airborne substances is known and the criteria for using air purifying respirators are met. Respirators, as their name suggests, protect the respiratory system along with the sensitive membranes of the nose, mouth and throat. Respirators are often beneficial, and even necessary, during Confined Space Entry (CSE).
1. Full-face or half-mask, air purifying respirators (NIOSH approved).
2. Hooded chemical-resistant clothing (overalls, two-piece chemical-splash suit, disposable chemical-resistant overalls).
3. Coveralls.
4. Gloves, outer, chemical-resistant.
5. Gloves, inner, chemical-resistant.
6. Boots (outer), chemical-resistant steel toe and shank.
7. Boot-covers, outer, chemical-resistant (disposable).
8. Hard hat.
9. Escape mask.
10. Face shield.
Level D PPE affords minimal protection and is used for nuisance contaminants only.
1. Coveralls.
2. Gloves.
3. Boots/shoes, chemical-resistant steel toe and shank.
4. Boots, outer, chemical-resistant (disposable).
5. Safety glasses or chemical splash goggles.
6. Hard hat.
7. Escape mask.
8. Face shield.
PPE Products for Hazmat Protection
Protective clothing: Hazmat suits provide body protection from head to toe. Suits are ideal when protecting personnel from industrial chemicals, biological agents and other hazardous substances. Hazmat suits are made to be reusable or disposable and can also be worn with other PPE equipment such as face masks and cooling vests.
Self-Contained Breathing Apparatus (SCBA): When the risk of exposure to hazardous materials or lack of oxygen is present on-site, workers should use a SCBA. SCBA provide personnel with breathable air from a compressed air cylinder or through a pneumatic system connected with hoses. When selecting SCBA, it’s important to consider that workers need as much protection as necessary with as little weight as possible so they can get the job done without impediment.
For special operations teams—like hazmat, technical rescue, rapid intervention teams, etc.—systems that allow automatic verbal interaction while leaving both hands free to focus on the task are ideal. For industrial fire brigades and firefighters, the NFPA 2018 approval is required.
Masks and filters: When working in an environment where hazardous materials may be present, wearing the correct respiratory protection is critical. After having performed an atmospheric hazard analysis in SCBA gear, if it is determined that the environment is safe for long-term work and meets OSHA’s hazardous substance Time Weighted Average (TWA) requirements, then workers can enter the area using other forms of respiratory protection, such as twin filter masks. A mask that has a double sealing frame with threefold sealing edges can offer a superior seal and a secure fit for almost all face shapes.
Because masks are often worn for extended periods of time, comfort and fit are key. It’s important for workers to make sure they are wearing the correct size, which can be achieved through a fit test.
Respiratory Protective Equipment: Concentrations of hazardous toxins and vapors can build up in confined spaces and in areas with inadequate ventilation. Where toxic substances can’t be completely controlled, respiratory protective equipment should be used. Respiratory protective equipment products include respiratory masks, respiratory filters, powered air purifying respirators (PAPR), SCBAs, airline and compressed air systems and more.
Safety eyewear: Protecting the body’s most important sensory organ, the eyes, is crucial when working in an industrial environment. When safety glasses or goggles are not worn, the eyes can be exposed to dangerous chemical splashes or debris that can damage the retina and a person’s vision.
Resource Tools: With access to reliable information and resources, supervisors and crew members can quickly find data to help identify hazardous substances and better insure their safe handling. One such resource tool is a hazardous substance database. It houses up-to-date information on more than 1,700 hazardous substances and their physiochemical characteristics. Personnel can search a substance’s name and quickly retrieve helpful information including workplace exposure limits, recommended respiratory and chemical protection equipment, and appropriate gas detection devices.
Handling hazardous materials poses numerous risks for industrial workers, but hazmat-related accidents and OSHA violations are preventable. This is why it’s critical to equip crew members with the correct PPE, knowledge and training. Planning and preparation are the most effective way to protect industrial workers from whatever may come their way.
This article originally appeared in the April 1, 2021 issue of Occupational Health & Safety.