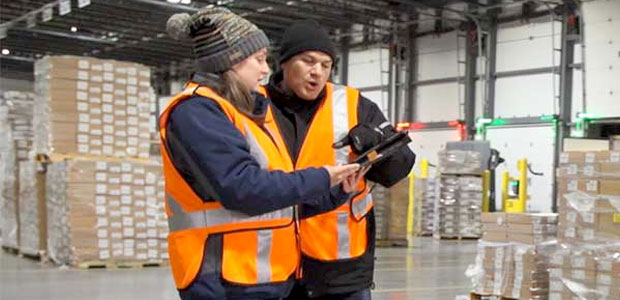
Page 3 of 4
Using the Industrial Internet of Things to Create a Safer Workplace
In an industrial and commercial world that keeps speeding up to match the soaring expectations of consumers, it is critical that safety is not left behind as operational efficiencies increase. Studies have recently linked the increasing speeds of fulfillment with working injuries—particularly in high-tech warehouses and distribution centers. Despite widespread efforts from senior management and facility managers, there is still room for improvement when it comes to industrial safety and injury prevention.
Facility managers are increasingly looking for ways to proactively address potential safety issues, instead of merely reacting to accidents that might cause harm to employees. The National Safety Council (NSC) estimates more than 4.6 million workplace injuries occur in the United States each year, which equates to one injury every seven seconds.1 The NSC projects that more than $161 billion in annual costs are associated with these injuries in the U.S.2 Therefore, investing in technologies allows companies to reduce risk and allow employees to return home safely to their families, which is top priority for any organization.
Advanced equipment and controls are now capable of collecting data, which is the first step toward network connectivity. For example, to improve safety at the loading dock, include interlocking dock controls that can be programmed to only work in a safe sequence of operation; motion sensor-activated audio and visual communication systems and intersection systems; and doors that automatically reverse when their photo eye is tripped.
The industrial workplace is utilizing the Internet of Things (IoT) technology to improve safety. The Industrial Internet of Things (IIoT) applies various sets of hardware working together to enhance the manufacturing industrial process. This focus allows companies to increase energy efficiency, streamline communication, enhance productivity and monitor events. Realtime and historical safety events can be communicated to safety managers though text and/or email alerts. These analytics allow companies to identify trends, find training opportunities and improve the behavior of employees through data-driven decisions.
Let’s examine how IIoT is taking safety to a new level in workplaces across the globe.
The First Wave: Wearable Devices and Moveable Sensors
In the industrial world, common wearable smart devices have been altered to provide metrics on additional health parameters. For example, smart watches can monitor workers’ exertion levels and body temperatures, then alert them (and their supervisors) when either become dangerously high. In another, more advanced example, Ford has introduced exoskeleton vests made of e-textiles with embedded nano-sensors that can analyze heart rate, temperature, blood-oxygen levels and fatigue.
On job sites, construction workers are now wearing hard hats with sensors that monitor heat rates, oxygen levels, fatigue and other dangerous stresses. These “smart hats” also gather data on working conditions such as equipment temperatures, dust, toxic conditions and more. What’s more, the sensors in the hat are interconnected to a communication network that transmits this data to analytical software able to predict unsafe conditions.
IIoT also is being used to connect fork trucks and place them on an automated governor. For example, pedestrian and forklift technology can slow the speed of the fork truck when it comes within a certain distance of pedestrians and actually stop the fork truck if it gets within certain distance parameters.
Wearable PPE technology and moveable smart equipment are helping shape the way industrial workers and managers think about safety. Real-time information provided by these devices can help inform immediate decisions that improve the health of—and mitigate safety risks to—individual workers.
IIoT and Building Infrastructure
As IIoT grows, data can be applied across entire operations to go much farther than heat stress and overexertion of one worker at a time or dangers specific to one location. After all, dangerous interactions with heavy equipment such as tractor trailers, machinery, AGVs and forklifts take place across the length and breadth of most industrial facilities. Akin to smart home systems that control temperature, lights, appliances and doors, IIoT systems in industrial workplaces can connect plant exteriors and loading docks to plant interiors and freezer/cooler areas—thereby collecting and dissecting safety data on a facility-wide scale rather than individual workers or locations.
Forklift interactions are particularly dangerous. Consider that, according to Optimum Safety Management,3 in the U.S. alone:
- Nearly 100,000 workers are injured per year due to forklifts;
- Approximately 85 workers die due to forklift accidents each year; and
- More than one in 10 forklifts will be in an accident every year (855,900 forklifts in U.S. and 97,000 annual forklift injuries).
Connecting IIoT systems with various pieces of smart equipment can pinpoint areas of risk at a plant like isolating potentially dangerous work areas to noting the highest traffic times of day. Capturing and centralizing this information is the first step in understanding the picture in any facility
Not All Data is Useful
One common challenge facing facilities bringing IIoT systems on line is the sheer volume of data they collect. Simply put, it can be overwhelming, making it difficult to distinguish what information is useful and identify trends or opportunities for improvement.
The best practice is an IIoT system that not only harvests raw data, but also allows the customer to drill into the details and provide users actionable insights so they can make data-driven decisions. The users of this IIoT data can identify specific trends, like what’s causing increased energy loss, why productivity is decreasing or areas that are creating the potential for unsafe events. It allows facility managers to “see” what they’re missing.
Improving Facility Safety through the IIoT
Smart equipment is the first step. Through advanced controls and sensors, simple machinery like high-speed doors and vehicle restraints can now capture events that can be reviewed through a centralized dashboard if connected through IoT. At their most basic, IIoT systems can send real-time safety alerts when something is wrong. The next level of advancement would include trending alerts that can warn facility managers if broader urgent actions are necessary.
The top-tier IIoT systems do even more. By examining the data, they can help facility managers gather insights they might not have drawn otherwise. By correlating current data points with historical trends, these systems can help identify corrective actions to improve specific safety points and safety behaviors—a much more enlightened approach than simply making changes after an accident or relying on employees to report a “near-miss.”
Leading IIoT systems allow safety personnel and plant managers to identify potentially unsafe events. As an added benefit, they may also discover new equipment or maintenance needs, potential training opportunities and process improvements.
Specific Areas for Implementation
Let’s take a look at some specific operational areas that can be enhanced by IIoT-informed management.
Loading dock equipment that is interlocked and allows proper sequence of operation is enhanced when controls are smart and connected to an IIoT platform. Here are a few control examples:
- Vehicle restraints: An employee may attempt to operate the leveler without engaging the restraint. The event will be logged, and the safety contact can receive an alert.
- Dock door barrier: Identify a potentially unsafe event when the dock door is left open with no trailer present and the barrier is not engaged.
- Motion sensors and light communication: When there is activity in the trailer, a blue light emits and prevents the vehicle restraint from erroneously unlocking the trailer when activity inside is detected.
Safety managers can use this data to see near misses that might have otherwise gone unnoticed or not been reported. An electronic tool like IIoT can document these instances without the human element of turning in a co-worker. They will stay up to date on changing employee behavior that might be dangerous, as well.
Inside the plant, workflow can be monitored to understand higher risk areas and even when an increased risk is likelier to occur. This can provide vital information to facility managers to not only improve safety but also increase productivity, as workers can be more certain of their own movements. Here are a few areas where technology can tap into the power of the IIoT:
- Dangerous intersections: Intersection warning systems can increase safety through intuitive communication. Data can be provided to determine directional interaction and assist with next steps.
- High-speed door openings: Communicate when a door has been left open, which can cause moisture buildup and lead to an unsafe condition.
Combining multiple data points and reviewing diagnostic analytics with IIoT technology allows companies to improve safety.
The IIoT Future is Already Here
A safety revolution is coming by the way of interconnected devices. Whether it’s at the loading dock or inside the plant, facilities that have already invested in IIoT are seeing the safety benefits. According to a PwC survey published in Industry Week, 93 percent of manufacturers believe IoT benefits exceed any4 the survey revealed that approximately 70 percent of industrial manufacturers plan to increase their investment into IoT within the next two years. Companies that aren’t using IoT to improve the safety in their manufacturing plants in the very near future are at risk of falling behind the competition.
Now is the time to begin investing in IIoT technology that can protect your organization’s most precious asset: your workers.
REFERNCES
1 https://www.nsc.org/Portals/0/Documents/JSEWorkplaceDocuments/ Infographic-injuries-bythe-Numbers.pdf?ver=2019-04-17-182214-630
2 https://injuryfacts.nsc.org/work/costs/work-injury-costs/
3 https://www.optimumsafetymanagement.com/blog/forklift-safetyinfographic/
4 https://www.industryweek.com/technology-and-iiot/ article/22028667/2020-future-of-manufacturing-technology
This article originally appeared in the April 2020 issue of Occupational Health & Safety.