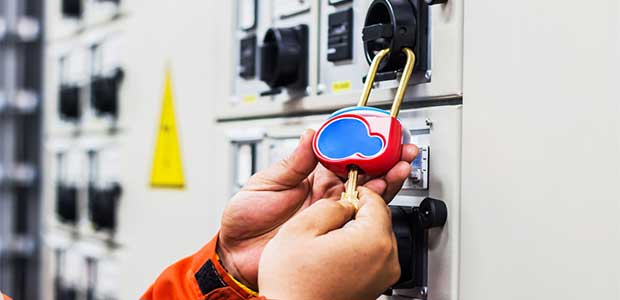
The Divergence of Mechanical and Electrical Lockout—A Best Practice Approach
There is an important relationship that exists between lockout and electrical safety.
- By Bill Belongea
- Sep 04, 2019
To ensure compliance under 1910.147, hazardous energy sources, such as electrical, pneumatic, hydraulic, chemical and thermal energy, need to be properly isolated to a zero-energy state through a series of shutdown steps documented by a lockout procedure.
The above-mentioned hazardous energies have dangers that need to be controlled to prevent mechanical motion through power generation or residual pressures during service and maintenance activities. However, electrical hazards have an additional piece of the puzzle that needs to be taken into consideration for isolation—the electricity itself.
Not only do electrical hazards exist as power generation to provide mechanical motion, it is the electricity itself that needs to be controlled and isolated within individual power installations such as disconnect panels, knife switches, MCC breaker panels, and circuit breaker panels.
There is an important relationship that exists between lockout and electrical safety. Lockout is required and used as a control measure to keep a worker safe, and electrical safe work practices need to be respected and followed prior to servicing or maintenance on electrical panels. The relationship between qualified electrical workers and Authorized lockout personnel follows the same path but diverge in different directions when an electrical installation is open to perform work. That’s where the Authorized Person’s job ends, and the qualified electrical workers begins.
Qualified vs. Authorized Personnel
Lockout is the practice of isolating hazardous energy to a piece of machinery to prevent the mechanical motion of critical components and the flow of dangerous energy such as air, chemicals, water. Isolating hazardous energy such as gravity, compressed springs, and thermal energy also play a significant role as they are identified as hazardous energy on a piece of equipment. To ensure these hazardous energy sources are isolated, an equipment specific lockout procedure is required to be followed. The identification and lockout of these hazardous energy sources can be done by personnel who have been trained by organizations as Authorized Personnel.
The limitations of Authorized Personnel start once activities go beyond shutting off isolating devices, such as gate valves ball valves, disconnects, circuit breakers, or blocking the motion of components and bleeding off residual air or hydraulic pressure. They are solely trained to conduct servicing and maintenance activities on a piece of machinery to isolate the mechanical motion and not those activities within electrical installations that contain live electricity. Those workers who have been trained, or have the skill, experience, training, and authorization by their organization to perform tasks within electrical installations containing live power are designated a Qualified Electrical Worker.
A Qualified Electrical Worker is permitted by their organization based on education, skill, experience, and knowledge not only to lockout machinery for servicing and maintenance tasks, but in addition to this ability, can enter electrical installations and perform electrical-related tasks with a panel.
When it comes to electrical maintenance and servicing activities such as troubleshooting, replacing fuses, or wiring, a lockout procedure typically doesn’t exist and isn’t required. However, that does not mean that lockout of these critical components of a piece of equipment or electrical installations does not need to occur. Working on live electrical installations has become a thing of the past with companies and standards organizations often mandate all electrical work to be done without the presence of power and require electrical work permits to be documented prior to servicing and maintenance on such electrical installations. Electrical work permits are designed to account for all electrical hazards in the event it is determined through a hazard assessment that live power must be present to conduct the servicing or maintenance task.
Applicable Lockout and Electrical Safety Standards
There are several standards, regulations, and best practices that influence organizational policy towards lockout and electrical safety. A combination of all must be taken into consideration to ensure a safe working environment for workers of all levels. Associating a task, a worker would engage in with a specific standard(s) is a good way to determine how far a worker can go in relation to servicing and maintenance tasks. An Authorized Person is not a Qualified Electrical worker, but a Qualified Electrical Worker must be an Authorized Person.
29CFR 1910.147. The lockout standard applies to all workers engaged in servicing and maintenance of all disciplines. Machine operators must shut down and lockout equipment to perform tasks such as unjamming, repositioning of parts, and other minor to moderate servicing and maintenance tasks. They are primarily identifying and locking out the isolation points on a piece of machinery to prohibit mechanical motion of the critical components.
Electrical power most often is one of the isolation points represented by a disconnect, knife switch, or circuit breaker. Machine operators and maintenance personnel that have been trained to the Authorized Personnel Level under this standard can go no further than shut down of these isolation points and affixing a lock and tag to ensure power is off and safe servicing and maintenance can begin.
Once a task has been identified that requires the breach of the electrical installation powering the machinery, the Authorized Person’s role is handed off to the Qualified Electrical Worker.
NFPA 70E. Once it is determined that work must be performed within electrical installations, it is critical that proper safe work practices are implemented prior to work commencing. NFPA 70E outlines in detail a risk mitigation process and hierarchy of controls with the goal of performing the electrical work without power. The risk mitigation and controls are centered around the identification of the current measured in amps and the potential difference of power measured in volts.
However, after a risk assessment is done and it’s determined that power must be off during a specific electrical task, lockout and electrical safety play important roles together. Once the electrical installation that needs servicing has been identified, determining the circuit breaker panel, transformer, or MCC panel that feeds this installation, lockout of this isolation point is required. Under this locked out condition, the precautions the Qualified Electrical Worker must take are not over. Based on NFPA 70E, Personal Protective Equipment (PPE) requirements are outlined to protect Qualified Electrical Workers from the hazards that electricity not only from an isolated electrical panel, but also once live work has been determined as the only option to service or maintain electrical installations.
Verification of Isolation is an important step in lockout as it relates to electrical work. Before work can begin in a locked out electrical panel, the PPE requirements outlined by NFPA 70E are required to determine that the power is off, and it has been verified that the electrical panel is in a zero-energy state. This is similar to mechanical lockout where 1910.147 states that verification of isolation to a piece of machinery must take place prior to conducting service and maintenance tasks.
In addition to the requirements of 1910.147 and NFPA 70E; OSHA 1910.333 of Subpart S covers the electrical safety and lockout requirements for these situations. It states that while employees are exposed to such hazards, live parts must first be de-energized and proper lockout must be followed. The requirements stated above work in concert with each other to provide strict guidance on protecting all workers from the dangers of electrical power.
Lockout Device Options for Electrical Installations
There are many options available to isolate this power with the development of innovative lockout devices. These devices have evolved based on input from those that conduct electrical work and developed with an understanding of locations, structure, and layout of electrical panels, installations, and circuit breaker panels. Examples of these lockout devices include circuit breaker devices, retractable cable devices, and dielectric safety padlocks.
- Circuit Breaker Lockout Devices – A main point of electrical isolation, these devices come in multiple shapes, sizes, and voltage capacities depending on organizational needs. Identifying the proper locks to accompany these devices along with the voltage of the panel is critical in making sure this is the right fit for the circuit breaker panel capacity.
- Retractable Cable Locks – This device allows workers to address challenging lockout situations that may require multiple energy isolating devices to be locked out at the same time. They can cover multiple electrical applications and be used on non-electrical isolating devices such as gate valves. In addition to having the capability of isolating multiple locations, they come in materials such as nylon that are non-conductive and offer peace of mind while working with electrical installations.
- Dielectric Safety Padlocks – Safety padlock selection is important based on the isolating device being locked out. When it comes to electrical installation lockout, components should be non-sparking, non-magnetic, and non-conductive. Customizations such as color-coding and engraving allow organizations to designate padlocks to specific workers and departments.
Best Practices for Electrical Safety and Lockout
Lockout and electrical safety have an important relationship with each other. Organizational policies must take into consideration the safety of their workers, not only by determination of tasks and skill, but providing the right equipment to do the job safely. Equipment from PPE to Dielectric Locks are integral to implementation of a Hazardous Energy Program that should include training and re-training, hazard assessments, specific policies for electrical work and lockout, and outlining specific roles and responsibilities for all workers within your organization.