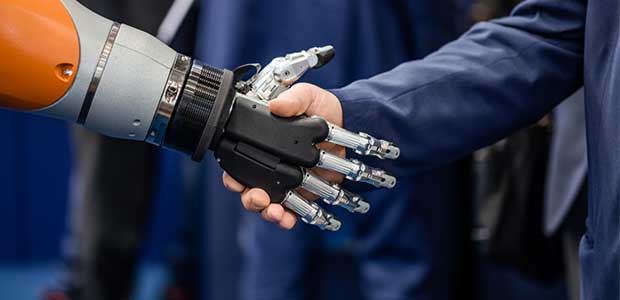
Robotics in the Workplace Initially Increase Safety but Pose New Hazards
The introduction of robots in the workplace has brought safety in certain situations, but potential hazards have also started to emerge. The documentation of these hazards will hopefully aid workers in avoiding future injuries.
As robots begin to become more commonly used in workplace settings, potential hazards also are beginning to emerge.
While the use of robots increases safety in certain areas of the workplace by allowing workers to steer clear of potentially hazardous situations, without the proper guidelines in place to ensure robotics safety, these injuries could resurface from the robots.
For instance, in 2015, a worker at a water bottling company was killed after attempting to remove a piece of plastic from the forks of a driverless forklift, known as a laser guided vehicle. The manufacturer’s manual required workers to initiate an emergency stop before removing an obstacle detected by the LGV, but the worker did not do this, which resulted in the LGV resuming its task as soon as the piece of the plastic was removed.
To prevent injuries and potential fatalities such as this one, the Washington State FACE Program issued the following recommendations for employers.
-
Incorporate manufacturer safety requirements into written company safety procedures for automated guided industrial vehicles.
-
Train workers about the specific hazards and safety requirements associated with automated guided industrial vehicles, such as LGVs.
-
Emphasize that workers are expected to follow required safety procedures every time, and ensure compliance through periodic refresher training and spot checks.
In two different cases, workers were injured while using demolition robots. In the first case, an operator was crushed between the robot and a wall after bumping the remote control against the machine. In the second case, a robot machine crushed a worker’s foot while attempting to apply more pressure on the tip of the breaker, which was being used to chip concrete. The machine shifted forward and the outrigger came down on his foot.
Following these injuries, the Washington State FACE Program issued the following recommendations for preventing injuries while working with demolition robots.
-
Prepare a job hazard analysis with operators for each new job to identify and control hazards. Use the manufacturer’s safety instructions to establish the risk zone for the specific machine, attachment, and task.
-
Always stay outside the risk zone when the machine is in operation, and do not enter until the machine is put into emergency stop mode or de-energized.
-
Consider using a proximity warning system, such as those based on radio frequency identification (RFID), to maintain a safe worker-to-machine distance.
-
Train operators to manage power cables and to continually monitor the process for hazards and redefine the risk zone.
-
Ensure operators always read and follow manufacturer’s provided safety instructions.
-
Consider using a spotter to assist the operator.
The National Institute for Occupational Safety and Health said since the use of robots in the workplace is so new, it’s difficult to know what regulations need to be made in order ot ensure safety. Therefore, the documentation of these accidents is vital to the continuation of robotics safety efforts.
“Currently, there is a lack of standard classification codes for robot-related injuries, which makes it hard to identify the frequency of incidents,” NIOSH said. “Additionally, worker injury data systems do not include detailed information on how a robot-related fatality or injury incident occurred.”
To begin to solve this, NIOSH established the Center for Occupational Robotic Research to increase worker safety while using robots.
“The center is building a research portfolio that includes efforts to document risk to workers through surveillance and fatality investigations,” NIOSH said.