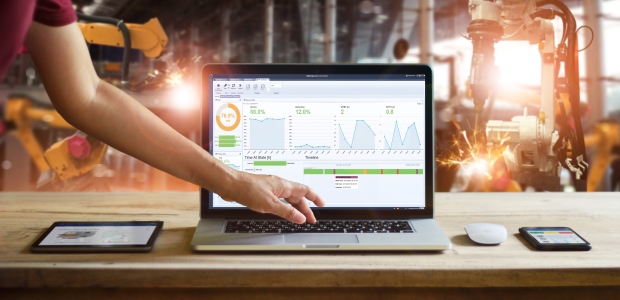
Page 3 of 3
Improving Electrical Safety in Industrial Environments Through Enhanced Technology Capabilities
Electrical safety is a key component in any environment, and as technology advances, so does the ability to effectively manage and prevent electrical hazards. The advancement of the Industrial Internet of Things (IIoT) gives end users within harsh industrial environments additional options and resources to ensure electrical components are operating efficiently and, most importantly, safely.
The IIoT uses smart sensors and devices on connected machinery to gather real-time data and analyze it to enhance manufacturing and other industrial operations. This extensive visibility into operations and machine health and information can contribute to business decisions that increase productivity and safety. Predictive analytics allow end users to better prevent and warn of future incidents and potential hazards before they come to fruition and can serve as a troubleshooting tool when a power issue arises with connected equipment.
The traditional electrical safety methods of yesterday, combined with today's enhanced technologies and processes, are working in tandem to optimize and enhance the safety and performance of large-scale industrial operations. Combining the use of advanced data analytics with connected equipment allows for gleaning new insights from the massive data streams being produced during normal operation.
Remote Monitoring and Real-Time Insights
With the ability to address equipment and wiring needs remotely to better monitor and manage industrial operations, the need for workers to maintain faulty equipment on site is significantly reduced. The cloud technology allows for functions such as real-time ground continuity monitoring, which ensures that shock hazards and the effects of electromagnetic interference are diminished.
One of the simplest examples of the benefits of IIoT integration into plant operations is increased visibility inside of electrical equipment. Most high-voltage electrical equipment includes protective covers or is contained in enclosures to prevent exposure to live parts. However, for troubleshooting activities, these protective covers historically had to be removed in order to be accessed by meters and other diagnostic tools. Now, advanced analytics can warn of conditions within external displays or remote terminals without physically removing any protective enclosures by hand, so much of the diagnostic work can be completed without opening the enclosures on the equipment. This type of technology may end up saving workers from being exposed to potential electrical hazards.
Technologies Enhancing Automation
Increasing automation within industrial facilities by incorporating technology can help to reduce electrical safety risks that a facility worker or engineer may have previously encountered on their own. With access to technologies that connect to third-party applications, industrial workers not only can review additional information, but also make safer, more informed decisions when servicing and troubleshooting IIoT-connected devices and equipment. Even smart, digital labels (including QR codes and bar codes) enhance automation technologies by simply providing a more streamlined approach to collecting information on operations and instructions of use, which in turn improves safety. These technologies aid in prescribing mitigation solutions for machinery issues and suggest how to better run equipment to extend and optimize the time between maintenance cycles.
Automation in the workplace also contributes to compliance, an integral part of operations within industrial facilities and manufacturing plants. From making it easier to follow prescribed safety protocols to modifying safety programs based on data collected about machine performance and operator behavior, leveraging the latest technologies to automate compliance and regulatory processes is a significant benefit to facility workers.
Predictive and Prescriptive Maintenance Plans
Many manufacturers are turning their approaches to maintenance to predictive and prescriptive plans—both of which are proactive solutions. The premise of these programs is to use data analytics to predict potential issues before they become hazards, which contributes to a safer operating environment for workers. Long-term reactive maintenance plans can contribute to a less-safe operating environment, not only due to the inherent danger from an unplanned failure, but also from the pressure to get things back up and running as quickly as possible, which tends to create an environment where workers may take shortcuts to make the repair.
Predictive maintenance involves the use of sensors to monitor actual device health in real time and makes maintenance decisions based on the actual performance data. It uses average data as a baseline against the historical maintenance of the device to best understand when maintenance should be performed. On the other hand, prescriptive maintenance plans leverage all of these features, but then go one step further to incorporate machine learning and artificial intelligence that can prescribe specific mitigation solutions for optimal results.
IIoT-connected solutions contribute to both predictive and prescriptive industrial maintenance programs in order to reduce operational downtime and get devices up and running quickly, resulting in a favorable impact on safety. With a deeper level of knowledge available through seamless connectivity, increased efficiencies are created regarding maintenance schedules for industrial devices.
For both predictive and prescriptive maintenance plans in industrial and manufacturing environments, IIoT technology is an important advancement. Leveraging the latest in technology to put a combination of the two maintenance plans in action increases safety, enhances productivity and reduces downtime for connected equipment. These advances also allow the end user to have a bird’s-eye view of maintenance activity via a third-party device without being exposed to the electrical hazards that may be associated with in-person maintenance.
Increased Visibility into Processes and Equipment Operating Conditions
The IIoT provides access to crucial data that was once inaccessible. Additional visibility into the status of various processes can, for example, help to prevent a crew based in the facility from interacting with hazardous materials or inserting themselves into potentially dangerous conditions.
Poor power quality can also be a safety hazard because it can cause unpredictable operation of electrically powered equipment and failures that can put operators or bystanders at risk. Even the devices that connect machinery to power can be impacted. IIoT functionality allows for real-time indication of power present in wiring devices, the amount of power flowing through them, and the quality of that power through detailed reporting. The trend reports make it easier to spot anomalies that can lead to potentially dangerous situations.
Creating Safe, Productive Industrial Manufacturing Facilities
As industrial manufacturing facilities become more modernized and better integrated with the latest technologies, factory and plant workers can not only receive better, more holistic insights, but also are able to diminish electrical safety risks throughout their facilities. With real-time data readily available to notify of any potential hazards and a more streamlined process for handling electrical-related issues, end users are moving toward safer and more productive industrial environments.
This article originally appeared in the June 2019 issue of Occupational Health & Safety.
About the Author
Genevieve Pasculli is the Marketing Manager of Leviton's Commercial and Industrial Business Unit. The Leviton INFORM Intelligent Platform enables conventional Leviton products to provide real-time information that is used to improve operational safety, efficiency and productivity, which can be received locally at the device, in real time via Leviton apps or integrated with third-party systems. The information is used to improve safety, enhance maintenance programs, and improve the response to unplanned downtime.