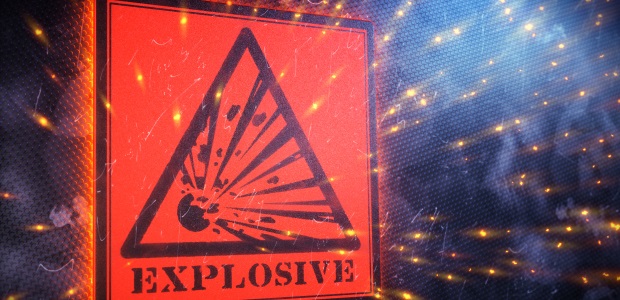
Combustible Dust Explosions: Are You at Risk?
Awareness training, good housekeeping, reference to safety data sheets, and adopting best practice should, in combination, minimize the potential for an explosion.
- By Steve Ochs
- Sep 01, 2018
Think about combustible dust explosions and coal dust, grain storage, and flour mills immediately spring to mind because they make primetime news, but essentially any workplace that generates dust is potentially at risk, including:
- Agriculture
- Chemicals
- Food (e.g., candy, sugar, spice, starch, flour, feed)
- Grain elevators, bins, and silos
- Fertilizer
- Tobacco
- Plastics
- Woodworking facilities
- Furniture
- Paper
- Tire and rubber manufacturing
- Textiles
- Pharmaceuticals
- Metal powder processing or storage (especially magnesium and aluminum)
Dusts are created when materials are transported, handled, processed, polished, ground and shaped. Dusts are also created by abrasive blasting, cutting, crushing, mixing, sifting, or screening dry materials. The buildup of dried residue from the processing of wet materials also can generate dusts.
In a 2014 New York Times article,1 the chairman of the U.S. Chemical Safety Board (CSB) stated that, "From 2008 to 2012, our board documented 50 combustible dust accidents [that] led to 29 fatalities and 161 injuries." This documentation was published in the aftermath of a horrific metal dust explosion in Jiangsu Province, China, that killed 75 people and injured another 185. It also followed an earlier 2006 CSB report that cited "281 combustible dust incidents between 1980 and 2005 that killed 119 workers, injured 718, and extensively damaged industrial facilities." Figure 1 shows global dust explosion statistics and specifically for the United States and China over an 80-year period; it is interesting that the same report2 shows that the issue in China is consistent with increased industrial output.
Specific OSHA regulations exists for grain dusts,3 but awareness training, good housekeeping (also subject to regulations4), reference to safety data sheets (SDS), and adopting best practice (see figure 2), such as that proffered by the National Fire Protection Agency (NFPA), should, in combination, minimize the potential for an explosion.5
So, what are the conditions that give rise to an explosion? A dust explosion can only occur when the following five factors are present (see figure 3):
- Fuel, in the form of dust particles
- Dispersion of the fuel in the form of a dust cloud
- Oxygen in the form of air
- Confinement of the dust cloud in the form of a container (e.g., a dust collector)
- A source of ignition
Figure 3: Explosion Pentangle (courtesy of AAF International)Dispersion could, for example, be as a result of a dry filter being pulse cleaned or, according to OSHA,
6from an initial (primary) explosion in processing equipment causing a blast wave that disturbs accumulated dust that, if ignited, causes a secondary explosion. The latter is often far more destructive than a primary explosion due to the increased quantity of dispersed dust (figure 4).
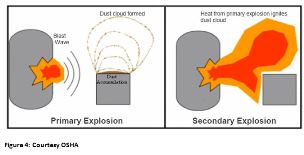
Should monitoring dust concentration also be part of the mitigation?
Undertaking a walk-through survey using a hand-held, real-time sampler would give instantaneous indication of concentration. It also could be used to check the effectiveness of control measures, such as local exhaust ventilation (e.g., pre and post filter).
Industrial hygienists may already be undertaking personal monitoring for toxic or sensitizing dusts, and the same air sampling pump could be used in combination with a real-time sampler when housed in a robust, portable case, on an unattended, short-term basis. Such a system can provide concentration using a gravimetric filter but also a time history profile, which could help identify the source of the problem.
Fixed, AC-powered solutions also could be used on a continuous basis for high-risk areas. These have the advantage that the data can be made available remotely using a web-based interface. These systems provide real-time alerts via text message or an email, should limits be exceeded. Reports can easily be automated and sent to multiple users, which allows for an early intervention to avoid a potential problem.
Great care should be taken in hazardous atmospheres that may require instrumentation to be intrinsically safe or require a hot-work permit, and action thresholds should always be set at a fraction of the lower explosion limit (LEL) for the dust in question. But if there is any doubt whatsoever, ensure that you speak to the relevant site manager or supervisor who has responsibility for risk assessment and permitting and who can advise accordingly.
Summary
Dust explosions continue to be a persistent problem for many industries resulting in loss of life, injuries, and destruction of property. Even those individuals most highly trained, including government enforcement officials, insurance underwriters, and company safety professionals, often lack awareness of combustible dust hazards. Safety Data Sheets are also ineffective in communicating to employers and workers the hazards of combustible dust explosions and ways to prevent them. This is all the more reason for all employees to have a basic awareness of the hazards of dust explosions and the best way to mitigate those risks.
References1.
New York Times, The Danger of Combustible Dust, Aug. 22, 2014
2. Dust Explosions: A threat to the process industries; Z. Yuan, N. Khakza, F. Khan, P. Amyotte, published online June 26, 2016, Institution of Chemical Engineers.
3. OSHA Grain Handling Facilities Standard 29 CFR 1910.272
4. 29 CFR 1910.22 (housekeeping) and 29 CFR 1910.176(c) (housekeeping in storage areas)
5.
https://cdn2.hubspot.net/hubfs/2368196/Workflows/2018/Combustible%20Dust%20/ePoster/ePoster%20-%20Combustible%20Dust%20Standards.pdf?t=1527790558769&utm_campaign=Combustible%20Dust%2FNFPA&utm_source=hs_automation&utm_medium=email&utm_content=63236873&_hsenc=p2ANqtz-_VSl8iu6aI-_8_NMMSv13SOCbntG3gTJ5IXy01SMM_TaSWFavjpZ4A-wiwPcFa0WFa0HKdiRfga7i9IOXWsJKewFW8MQ&_hsmi=632368736. Combustible Dust in Industry: Preventing and Mitigating the Effects of Fire and Explosions. Safety and Health Information Bulletin SHIB 07-31-2005; updated Nov. 12, 2014
This article originally appeared in the September 2018 issue of Occupational Health & Safety.