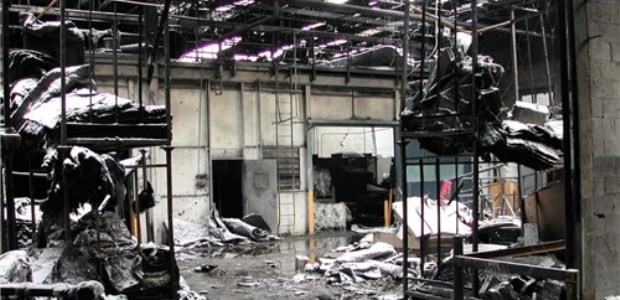
Think You Don't Have Combustible Dust in Your Facility? Think Again!
The bottom line is this: If your facility contains dust, you should have it tested for combustibility.
- By Stephen Watkins
- May 01, 2018
"Combustible dust isn't a concern in our industry."
"Our facility has never had a combustible dust problem."
"We have dust, but the particles are too big to be combustible."
Have you heard (or thought) any of these things? We hear them all of the time from people in many industries as reasons they don't need to worry about combustible dust hazards.
But ideas like these are exactly the reason combustible dust incidents continue to happen. The false belief that hazards don’t exist prevents companies from taking steps to mitigate them. The unfortunate result is explosions like the 2008 incident at the Imperial Sugar factory1 that claimed 14 lives, injured 38 people, and led to OSHA fines of nearly $9 million.
The Imperial Sugar explosion brought combustible dust into the spotlight . . . at least for the sugar industry. But the fact is that if you work in any sort of manufacturing or industrial processing facility, you likely have combustible dust in your facility. And where there's dust, there's risk.
Let's take a closer look at the misconceptions above.
'Combustible Dust Isn't a Concern in Our Industry.'
This is almost certainly untrue. While the "usual suspects"—e.g., grain milling, sawmilling, sugar—get most of the attention, combustible dust and the hazards associated with it exist in almost every industry.2
Here are some examples of combustible dust hazards in industries you might think are immune to the problem.
3D printing
Most materials used in 3D printing are combustible, and the printing process itself generates very fine dust particles. In some cases, these particles can be very reactive and burn very fast. In 2013, combustible metal powders including titanium and aluminum alloys led to an explosion at 3D printing company Powderpart, causing third-degree burns on an employee. Powderpart was fined $64,400.3
Ink manufacturing
During the ink manufacturing process, fine particulate solids are mixed with liquid oils. These solids can be highly combustible. In 2012, seven workers were injured at U.S. Ink when powder containing Gilsonite (a hydrocarbon) and carbon black that had accumulated in ductwork above a tank ignited. In its investigation, the U.S. Chemical Safety Board found that the dust had taken only one day to accumulate to a dangerous level and that the company hadn't even performed a hazard analysis to ensure that their newly installed dust collection system would work.4
Food manufacturing
It's not just sugar. Nearly every ingredient used in making food can potentially become combustible. That includes starches, milk powders, and powdered forms of everything from beet root to tomatoes.5 Recent high-profile incidents include a 2014 grain dust explosion at a Nestle Purina PetCare processing facility6 and a dust explosion in a malfunctioning hopper at food texturizer and stabilizer manufacturer T.I.C. Gums.7
Power generation
Even the power generation industry has seen its share of serious combustible dust incidents. The most well-known is the 1999 explosion at Ford's River Rouge manufacturing plant, which killed six workers and injured 36. Michigan OSHA concluded the company's housekeeping procedures were insufficient to control the accumulation of coal dust, which is what led to the explosion.8
With the rise of hydraulic fracturing (fracking), the oil and gas industry also faces a combustible dust threat—from the plastic composites used to manufacture fracking balls.9
These are just some examples of industries with combustible dust risks. They can also be found in aerospace, automotive manufacturing, metal recycling, composites manufacturing, and more. The bottom line is this: If your facility contains dust, you should have it tested for combustibility.
'Our Facility Has Never Had a Combustible Dust Problem.'
This idea is understandably pervasive—it's easy to grow complacent when you've never had a problem. However, it's an idea that can get you into trouble in more ways than one.
First, although some companies are repeat offenders when it to comes combustible dust incidents,10 the vast majority of these explosions take place in facilities that have never had a problem before.
In fact, if you have combustible dust, the longer you go without an incident, the worse the problem is likely to be. This is because dust accumulates over time, and this accumulation is what puts your facility at risk. That's why OSHA recommends not letting dust accumulate more than 1/32" over more than 5 percent of the facility floor.11
Another thing to consider is whether your processes have changed. Even if you've been in business for 30 years, you've probably introduced new equipment and processes during that time. If so, your risk profile may have changed. This was the root of the problem in the ink manufacturing incident described above. The company didn't do the proper checks because they assumed that the new dust collection system was similar enough to the old one—a false assumption that led to a tragic result.
Finally, this idea can also get you into hot water with OSHA and other inspectors that follow National Fire Protection Association standards. NFPA 652 requires all facilities that process, handle, convey, or manufacture potentially combustible dust to have their dust tested, even if you've never had a problem before and even if your type of dust has not caused problems in the past.12 In other words, in the eyes of regulatory agencies, past performance is not an acceptable indicator of future performance.
'We Have Dust, But the Particles Are Too Big for It to Be Combustible.'
This last idea is a particularly dangerous one because it can be the result of inadequate dust testing.
When determining whether or not dust is combustible, size matters. In general, any particles smaller than 500 microns should automatically be considered combustible, though larger dusts may be combustible, as well.
As Fauske & Associates' Dr. Ashok Ghose Dastidar explained in a recent interview with Nilfisk,13 the trick is that many dusts (for example, the dust in a wood processing plant) aren't uniform: They contain coarser materials (i.e., sawdust) as well as finer materials (wood flour). When these materials segregate (such as the wood flour accumulating on elevated surfaces), the finer materials can create a combustible dust hazard.
Dr. Dastidar went on to differentiate between two types of dust testing: "as received" and after sizing and drying. Companies frequently want to have their dust samples tested "as received," meaning as if segregation doesn't occur. This is useful for determining certain dust characteristics, such as ignition sensitivity,14 but it underestimates the true risk because it ignores the fact that segregation does often occur.
Testing your dust after sizing and drying provides more conservative, and more realistic, results. This is especially important in facilities that handle large quantities of dust. Dr. Dastidar noted in his interview: "[Companies] don't realize that even if just 5% of that material is less than 500 microns, if they're handling large quantities (e.g., 1 or 2 tons of material), then 5% can represent hundreds of pounds of dust, which is big enough to pose a risk."
So, do you have combustible dust in your facility? The answer is probably yes—even if your industry and your company have never had a problem before. The only way to know for sure is to have your dust tested in accordance with NFPA standards.
If it does turn out that your dust is combustible, there is some good news. Combustible dust is controllable and dust-related incidents are 100 percent preventable through engineering controls and proper housekeeping. By taking these steps today, you can protect your plant and your personnel into the future.
References
1. "Imperial Sugar Company Dust Explosion and Fire." U.S. Chemical Safety Board. http://www.csb.gov/imperial-sugar-company-dust-explosion-and-fire/
2. "Combustible Dust Incidents from 15 Industries." Nilfisk. http://news.nilfiskcfm.com/2018/01/combustible-dust-incidents-15-industries/
3. "After explosion, US Department of Labor's OSHA cites 3-D printing firm for exposing workers to combustible metal powder, electrical hazards. Powderpart Inc. faces $64,400 in penalties." OSHA. https://www.osha.gov/news/newsreleases/region1/05202014
4. "CSB Names Poor Design and Failure to Test Dust Collection System Among Causes of U.S. Ink New Jersey Flash Fire that Burned Seven Workers in 2012; OSHA Again Urged to Issue New Combustible Dust Regulations." U.S. Chemical Safety Board. http://www.csb.gov/csb-names-poor-design-and-failure-to-test-dust-collection-system-among-causes-of-us-ink-new-jersey-flash-fire-that-burned-seven-workers-in-2012-osha-again-urged-to-issue-new-combustible-dust-regulations-/
5. "Combustible dust: Does your company or firm process any of these products or materials in powdered form?" OSHA. https://www.osha.gov/Publications/combustibledustposter.pdf
6. "State fines Nestle Purina for September explosion." Arizona Daily Sun. http://azdailysun.com/news/local/state-fines-nestle-purina-for-september-explosion/article_30037549-d219-51b4-bcd8-18cef0d5aaa6.html
7. "Dust Explosion Causes Fire at T.I.C. Gums Warehouse." Powder and Bulk Solids. http://www.powderbulksolids.com/news/Dust-Explosion-Causes-Fire-at-TIC-Gums-Warehouse-06-29-2017
8. "Ford Settlement." Michigan OSHA. https://www.michigan.gov/documents/CIS_WSH_minwsf99_27783_7.pdf
9. "A New Industry Brings New OSHA Combustible Dust Fines." Hughes Environmental. https://hughesenv.com/fracking-osha-combustible-dust-fines/
10. "Final Report on AL Solutions Metal Dust Explosion and Fire that Killed Three in West Virginia Leads CSB to Reemphasize Call for OSHA Combustible Dust Standard." U.S. Chemical Safety Board. http://www.csb.gov/final-report-on-al-solutions-metal-dust-explosion-and-fire-that-killed-three-in-west-virginia-leads-csb-to-reemphasize-call-for-osha-combustible-dust-standard-/
11. "Combustible Dust National Emphasis Program." OSHA. https://www.osha.gov/OshDoc/Directive_pdf/CPL_03-00-008.pdf
12. "What You Don't Know About Combustible Dust, But Should." Occupational Health & Safety. https://ohsonline.com/blogs/the-ohs-wire/2017/03/what-you-dont-know-about-combustible-dust-but-should.aspx
13. "Is Your Combustible Dust Risk Greater Than You Think? What You Need to Know About Particle Size." Nilfisk. http://news.nilfiskcfm.com/2017/11/combustible-dust-risk-greater-think-need-know-particle-size/
14. "7 Basics of Combustible Dust Sampling and Testing." Fauske & Associates. https://www.fauske.com/blog/7-basics-of-combustible-dust-sampling-and-testing
This article originally appeared in the May 2018 issue of Occupational Health & Safety.