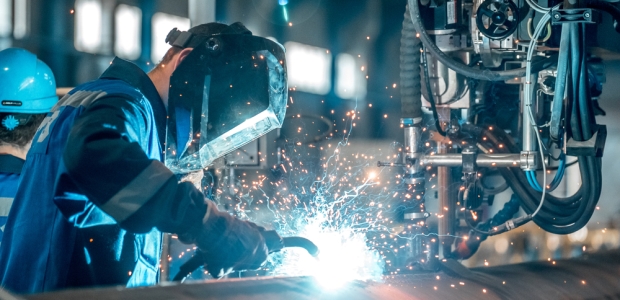
The Industrial Hygienist's Guide to Anticipate, Evaluate, and Manage Occupational Health & Safety Risks with Industrial Hygiene Software
Effective industrial hygiene management requires recording and maintaining consistent and complete work site data. Using outdated methods is in itself a serious risk.
- By Ma Joelle Lingat
- May 01, 2018
Industrial hygienists are veritably occupational health and safety superheroes, standing alert to anticipate, recognize, and prevent risks and controlling environmental factors or stressors arising in or from the workplace to help prevent sickness, impaired health and well-being, or significant discomfort among workers or citizens of the community.
The chief goal of an occupational health and safety program in a facility is to prevent occupational injury and illness by anticipating, recognizing, evaluating, and controlling occupational health and safety hazards. Industrial hygiene software equips users with the tools and resources needed to help occupational health and safety professionals carry out their job to the best of their abilities—to continue to protect workers and reduce impact to the environment.
Let's walk through how to identify and evaluate workplace hazards, address and anticipate future threats, and manage your occupational health and safety program efficiently and effectively by establishing a plan with the right industrial hygiene software tools.
Getting Started
Before diving into the many activities that comprise your industrial hygiene program, it's important to establish your program expectations and a strategy for action. Begin by asking yourself the following: What are you trying to accomplish? Set program goals. Who will be affected by your program? Identify your key stakeholders. What regulations you must comply with? Find out what your legal obligations are. Will your program be specific to a certain location? Establish your boundaries.
Our experts identify the following key health and safety expectations:
- Identify tasks
- Assess risks
- Prioritize actions
- Identify controls
- Implement controls and train employees
- Assess performance
- Investigate issues (including potential)
- Maintain data and reports
Next, you will need to identify what your potential hazards are applicable in your case. There are many different stressors that could affect your workers and your community, such as:
- Air contaminants
- Biological exposures
- Chemicals
- Confined spaces
- Dusts
- Ergonomics
- Fumes
- Particles that affect respiratory health
- Radiation exposure
- Work in extreme heat and cold environments
- Work in high- or low-pressure environments
And that's just to name a few. Once you understand the stressors that affect your workplace environment, it's time to develop a plan for action.
Anticipating and Recognizing Hazards
The first step to anticipating and recognizing hazards is to conduct a work site analysis. This will help you and your team determine what activities and areas are susceptible to hazard. You will need to measure and identify exposures and risks, which includes inspecting, researching, and analyzing chemicals and physical hazards that put your work site or workers' health in jeopardy. It's important to regularly monitor your workplace environment to identify current and potential risks proactively—you don't want a reactive strategy.
Begin by establishing a standardized process for industrial hygiene assessments across all site operations. Be sure to include all jobs, operations, and worker activities. Once you pinpoint risk points, assign corrective and preventative actions and track accordingly to closure. At this point, it is also important to communicate any exceedances and notify your employees of identified hazards.
Evaluating and Controlling Your Environment
According to the Occupational Safety and Health Administration (OSHA), an effective industrial hygiene management program relies on recognizing that engineering, work practice, and administrative controls are the primary means of reducing employee exposure to occupational hazards. Here are OSHA's recommendations for evaluating and controlling your environment according to their industrial hygiene training materials:
- Engineering controls minimize employee exposure by either reducing or removing the hazard at the source or isolating the worker from the hazard. Engineering controls include eliminating toxic chemicals and substituting non-toxic chemicals, enclosing work processes or confining work operations, and the installation of general and local ventilation systems.
- Work practice controls alter the manner in which a task is performed. Some fundamental and easily implemented work practice controls include (1) changing existing work practices to follow proper procedures that minimize exposures while operating production and control equipment; (2) inspecting and maintaining process and control equipment on a regular basis; (3) implementing good housekeeping procedures; (4) providing good supervision; and (5) mandating that eating, drinking, smoking, chewing tobacco or gum, and applying cosmetics in regulated areas be prohibited.
- Administrative controls include controlling employees’ exposure by scheduling production and tasks, or both, in ways that minimize exposure levels. For example, the employer might schedule operations with the highest exposure potential during periods when the fewest employees are present.
- When effective work practices or engineering controls are not feasible or while such controls are being instituted, appropriate personal protective equipment must be used. Examples of personal protective equipment are gloves, safety goggles, helmets, safety shoes, protective clothing, and respirators. To be effective, personal protective equipment must be individually selected; properly fitted and periodically refitted; conscientiously and properly worn; regularly maintained; and replaced, as necessary.
Implementing these controls in combination with proper employee training will largely help to prevent incidents from occurring, putting into effect proactive industrial hygiene management.
Managing Your Occupational Health and Safety Program
When it comes to managing your occupational health and safety program, your job can be made easier if equipped with the right tools. This is where investing in industrial hygiene software comes into play.
Effective industrial hygiene management requires recording and maintaining consistent and complete work site data. Using outdated methods, such as Excel spreadsheets or, worse, pen and paper methods, is in itself a serious risk. While these management systems do work, it requires more time and effort on your end and is prone inaccuracy and miscommunication.
One case where ineffective industrial hygiene management proved devastating was a series of explosions that resulted in 173 fatalities and hundreds of injuries at the Port of Tianjin on Aug. 12, 2015. Sadly, the explosions could have easily been prevented had industrial hygiene management been in place. Through investigation, it was discovered that many of the hazardous materials stored at Port of Tianjin were incompatible with one another and were improperly stored. The chemicals on site were not properly documented and were not approved by the Chinese government. There was no buffer zone established between the site and the community, putting innocent lives at risk. All were activities that should have been monitored and managed to prevent this incident from happening.
Industrial hygiene software helps you identify and communicate when something is not safe, to keep your workers and the community sound. It provides the right capabilities to manage work site safety with ease and gives you the confidence you are protecting your employees. By using industrial hygiene management software, you have access to a platform that manages and maintains all necessary industrial hygiene activities, including establishing a standardized assessment process, documenting qualitative demographic surveys and exposure/control information, easily logging monitoring data, managing employee training, and assigning and tracking corrective actions. Choosing to digitize your industrial hygiene solution can also include integrated analytics to evaluate and enable continuous improvement over time, characterize new hazards related to change, and provide exclusive features, such as multilingual and offline mobile capabilities to be used anywhere and at any time.
When it comes to industrial hygiene, the risk of ineffective management is too great. You can't afford to use a system that doesn't do its job. Deploying industrial hygiene software is the best way to anticipate, evaluate, and manage occupational health and safety risks, enabling you to prioritize the health and safety of your employees and the community.
References
1. https://www.osha.gov/dte/library/industrial_hygiene/industrial_hygiene.pdf
2. https://www.aiha.org/government-affairs/PositionStatements/whitepaper01_SweatshopsGlobalEconomy.pdf
3. http://www.ehstoday.com/industrial_hygiene/ehs_imp_38050
This article originally appeared in the May 2018 issue of Occupational Health & Safety.