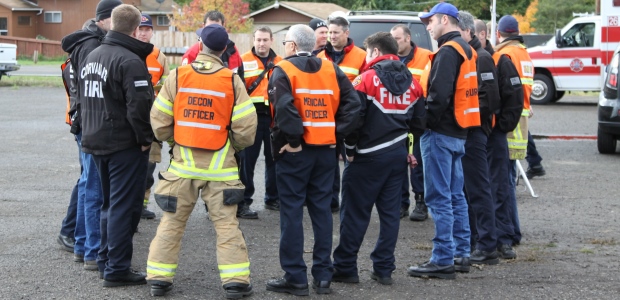
Everyone is an Emergency Responder
If employees take the wrong response actions, don’t know what to do, or try to perform jobs they are not capable of, the resulting mistakes, confusion, and disarray will stand in the way of a safe response.
- By Roger Marks
- May 01, 2018
The first moments of a hazardous substance release can be chaotic, disorienting, and scary. Safety professionals know all too well that in moments like these, human nature alone is not a reliable safety system.
If your facility uses and stores hazardous chemicals, you may be aware that under OSHA's Hazardous Waste Operations and Emergency Response (HAZWOPER) Standard, the terms "emergency" and "responder" hold more nuanced and complex meaning than a basic dictionary might suggest.
Everyone responds during a hazardous substance release. When a chemical release happens—whether it happens on the production floor, in the warehouse, in the lab, in the shipping dock, or elsewhere—employees of varying experience levels and physical abilities may be nearby. If an employee does not respond in some way, he or she could become ill, be injured, or lose his or her life.
It is critical that employers understand the various "levels" of HAZWOPER training that OSHA requires for different employees. By seeing how one level builds on the next, we can get a clear view of each employee's responsibilities and how much emergency response training each employee needs.
"In moments like these, human nature alone is not a reliable safety system."
Level 1 'Awareness'
Every employee who may witness or discover a hazardous substance release and who is responsible for alerting others or evacuating must complete first responder HAZWOPER awareness training. OSHA sets no time requirement for awareness level HAZWOPER training. Because awareness level first responders' responsibilities only include notifying others and evacuating, Level 1 is purely competency based. Employees must demonstrate competency in:
1) Hazardous substance awareness, identification, and recognition
2) Understanding of the potential outcomes and risks
3) His or her role in the facility's emergency response plan (e.g., site security, control, and the Emergency Response Guidebook, or ERG).
[29 CFR 1910.120(q)(6)(i)]
Of course, not every spill is an emergency incident. Knowing the difference between an incidental cleanup and an emergency response situation is part of the awareness that Level 1 training builds.
Employees who work with hazardous chemicals that do not pose a significant safety or health hazard should be trained according to OSHA's Hazard Communication Standard, or HCS. U.S. DOT requires safety training, too, for employees involved in shipping hazardous materials.
Level 2 'Operations'
First responders at the operations level are individuals who respond to releases, or potential releases, of hazardous substances to protect nearby people, property, or the environment.
Like awareness employees, operations level HAZWOPER responders keep a safe distance from the release and do not try to stop it. That said, these employees also perform critical defensive response actions when a release occurs, such as remote shutdown of equipment, covering floor drains, or placing absorbent barriers to contain the release.
Employees with Level 2 responsibilities must complete eight hours of HAZWOPER training, unless the employee has sufficient experience to demonstrate both awareness level and operations level competencies.
Operations first responder training must cover all elements of Level 1 training and several additional aspects of emergency response, such as:
1) Hazardous substance terminology and risk assessment
2) Selecting and using proper personal protective equipment (PPE)
3) Basic control, containment, and confinement of releases
4) How to follow relevant facility emergency response procedures
[29 CFR 1910.120(q)(6)(ii)]
Level 3 'Hazardous Materials Technician'
Hazardous materials technicians, also called emergency response technicians or simply "hazmat techs," are individuals who actively respond to stop a hazardous substance release. Level 3 personnel are trained to approach the point of release and plug, patch, or otherwise stop the emergency.
Because this responsibility may involve putting themselves in harm's way, hazardous materials technicians must complete 24 hours of HAZWOPER training before starting the job. Level 3 training must cover the elements described in Levels 1 and 2 above. In addition, each Level 3 employee must be trained to:
1) Understand hazard and risk assessment techniques
2) Understand basic hazardous substance terminology and behavior
3) Implement the facility’s emergency response plan and relevant procedures
4) Select and use the proper PPE for the job
5) Perform his or her role within the Incident Command System (ICS)
6) Classify, identify, or verify materials involved using field survey instruments and equipment
7) Perform advanced control, containment, and/or confinement operations
[29 CFR 1910.120(q)(6)(iii)]
Level 4 'Hazardous Materials Specialist'
Hazmat Specialists also play a critical role in the active response to stop a hazardous substance release.
Specialists respond with and provide support for hazardous material technicians. Specialist have more specific knowledge about chemical substances, their properties, and their hazards. They also act as liaisons with any local authorities that may be involved with the response.
Specialists must be trained to the technician level and demonstrate additional competencies for aspects of emergency response, such as:
1) How to develop or implement all emergency plans and procedures
2) How to use advanced field survey instruments and equipment
3) How to perform specialized control, containment, and/or confinement of a release
4) Knowledge of hazardous substances and emergency response
Level 5 'On-scene Incident Commander (IC)'
During a chemical release, the on-scene incident commander manages the facility response. He or she establishes objectives, plans response strategies, and ensures the plan is followed.
Like all responders Level 3 and above, incident commanders must complete 24 hours of initial HAZWOPER training, be competent at least to the operations level, and demonstrate additional competencies generally related to big picture emergency response planning, such as:
1) Know and understand the hazards and risks of emergency response
2) Have knowledge of the Federal Regional Response Team
3) Know, understand, and be able to implement the Incident Command System and all company, local, and state emergency response plans and procedures
Once Is Not Enough
Once employees have been trained to the proper level based on their responsibilities, training must be repeated annually. Annual refresher training is required for every HAZWOPER first responder, from the awareness level to the Incident Commander. [29 CFR 1910.120(q)(8)]
When a release occurs, your employee may not have time to "remember" his or her training. HAZWOPER training needs to be repeated to ensure employees can play their roles at a moment's notice. Whether the employees' responsibilities involve active measures to stop a release or simply pulling the fire alarm and evacuating the building, each and every worker must know what to do in the event of a chemical release.
If employees take the wrong response actions, don't know what to do, or try to perform jobs they are not capable of, the resulting mistakes, confusion, and disarray will stand in the way of a safe, efficient response—and could cost a worker his or her life.
This article originally appeared in the May 2018 issue of Occupational Health & Safety.