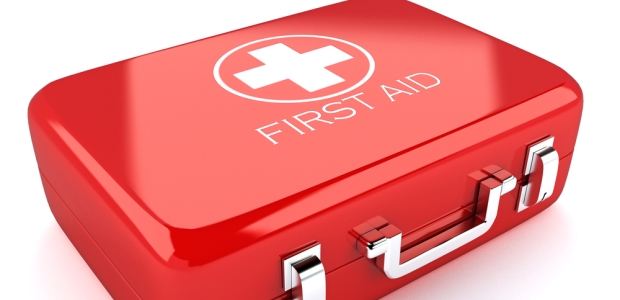
Page 2 of 4
Meeting OSHA's First Aid Requirements
An OSHA enforcement case announced in September 2011 is a good example of the importance of complying with the agency's first aid standards. The agency proposed a total of $221,200 in penalties in citing a Texas boat and barge repair company for one willful and 39 serious violations after the deaths of two workers from a fire. Among the violations cited was a serious violation of OSHA 29 CFR 1915.98(a), the medical services and first aid standard for shipyard employment; at the barge OSHA personnel investigated, the only first aid kits were located in the office approximately 300 yards away, far from "readily accessible" as OSHA's standard mandates.
OSHA lays out general industry employer responsibilities for medical services and first aid for injured or sick workers in 29 CFR 1910.151. The standard is familiar: Employers must ensure that medical personnel are readily available for advice and consultation, a person or persons on site are trained in first aid, and first aid supplies are readily available. In addition, facilities for emergency drenching or flushing of the eyes and body must be present within work areas where a worker’s eyes or body may be exposed to harmful corrosive materials.
First Aid Kit Contents
According to OSHA's 1904.7(b)(5)(ii), first aid can encompass a variety of actions, including using wound coverings such as bandages, removing foreign bodies from the eye using irrigation or a cotton swab, and even administering tetanus immunizations.
With such a wide variety of treatments falling under the umbrella of first aid, OSHA does not have strict requirements for the materials a first aid kit should contain. Instead, the agency advises in its Best Practices Guide: Fundamentals of a Workplace First-Aid Program, that each employer designate one person the responsibility of choosing the types and amounts of first aid supplies, as well as maintaining them and the kit. As a starting point, OSHA directs employers to American National Standard ANSI/ISEA Z308.1-2015, "Minimum Requirements for Workplace First-aid Kits," which recommends the following contents:
- Adhesive bandage
- Adhesive tape
- Antibiotic application
- Antiseptic
- Breathing barrier
- Burn dressing (gel soaked)
- Burn treatment
- Cold pack
- Eye covering (with means of attachment)
- Eye/skin wash
- First aid guide
- Hand sanitizer
- Medical exam gloves
- Roller bandage (2 inch)
- Roller bandage (4 inch)
- Scissors
- Splint
- Sterile pad
- Tourniquet
- Trauma pad
- Triangular bandage
First Aid Training
OSHA's language around first aid training is also broad. The 1910.151 standard does not name any particular training program or level of expertise for first aid compliance; instead, more specific training requirements are named in several standards that address permit-required confined spaces, commercial diving operations, logging operations, electric power, shipyard employment, and construction. These industries require more specific standards because of their specialized nature.
The standard for permit-required confined spaces, 1910.146: Permit-required Confined Spaces, requires employers to train affected employees in basic first aid and cardiopulmonary resuscitation (CPR), as well as ensure that at least one member of the rescue team or service holding a current certification in both is available. As for commercial diving operations, 1910.410, Qualifications of Dive Team, requires all dive team members to be trained in CPR and first aid, specifying the American Red Cross standard course or its equivalent. The standards for logging operations, electric power, and construction are more detailed.
Logging Operations
Appendix B of 1910.266, Logging Operations, states that, at minimum, employees must be trained in first aid and CPR by conventional methods such as lecture, demonstration, practical exercise, and written and practical exam, for long enough that trainees can demonstrate their ability to perform the following outlined procedures:
- Patient assessment and first aid for the following:
- Respiratory arrest
- Cardiac arrest
- Hemorrhage
- Lacerations/abrasions
- Amputations
- Musculoskeletal injuries
- Shock
- Eye injuries
- Burns
- Loss of consciousness
- Extreme temperature exposure (hypothermia/hyperthermia)
- Paralysis
- Poisoning
- Loss of mental functioning (psychosis/hallucinations, etc.)
- Drug overdose
- CPR
- Application of dressings and slings
- Treatment of strains, sprains, and fractures
- Immobilization of injured persons
- Handling and transporting injured persons
- Treatment of bites, stings, or contact with poisonous plants or animals
Electric Power Generation, Transmission, and Distribution
OSHA standard 1910.269: Electric Power Generation, Transmission, and Distribution has clearer instructions on how many first aid-trained people should be available, depending on when and where the work is taking place. When employees are performing work on or associated with exposed lines or equipment energized at 50 volts or more, the requirements for compliance are as follows:
- For field work involving two or more employees at a work location, at least two trained people shall be available.
- For line-clearance tree trimming performed by line-clearance tree trimmers who are not qualified employees, only one trained person need be available if all new employees are trained in first aid within three months of their hiring dates.
- For fixed work locations such as substations, the number of trained persons available shall be sufficient to ensure that a trained person can reach each employee exposed to electric shock within four minutes. If the existing number of employees is insufficient to meet this requirement, each employee at the work location shall be a trained employee.
Shipyard Employment
OSHA addresses the first aid standards for shipyard employment in OSHA standard 1915.87. Shipyard employers must ensure that emergency medical services, first aid, and health care professionals are readily accessible. An adequate number of employees trained as first aid providers must be present at each work site during each workshift unless there is an on-site clinic or infirmary with first aid providers during each workshift or outside first aid providers can reach the work site within five minutes of a report of injury or illness. First aid providers should be trained in first aid and CPR and maintain current first aid and CPR certifications issued by organizations such as the Red Cross, American Heart Association, or their equivalent.
The number and location of first aid-trained employees should be determined based on factors that include the size and location of each work site, the number of employees and the hazards present at each work site, and the distance of each site from medical services. The same factors should apply to the placement, content, and amount of first aid supplies, which should be placed in a weatherproof container. Shipyard employers must also provide an adequate number of basket stretchers readily accessible to where work is being performed on a vessel or vessel section.
Construction
The first aid requirements for construction are found in OSHA's 1926 standards: If there is no infirmary, clinic, hospital, or physician "reasonably accessible in terms of time and distance" to the site, there must be someone with a valid certificate in first aid training from the American Red Cross or equivalent training that can be verified by documentary evidence available to render first aid. OSHA explained as recently as January 2007 that "reasonably accessible" should be interpreted to mean that emergency care must be available within three to four minutes.
The standards also address the contents of first aid kits for construction work sites, stating that each type of item should be in individually sealed packages and placed in a waterproof container. Additionally, the kits should be checked by employers before being sent out to each job and checked at least weekly as well, to ensure that any used items have been replaced.
For industries other than these, employers must evaluate their own first aid response and preparedness programs based not only on OSHA compliance, but the needs of their workplace and employees.
This article originally appeared in the April 2018 issue of Occupational Health & Safety.