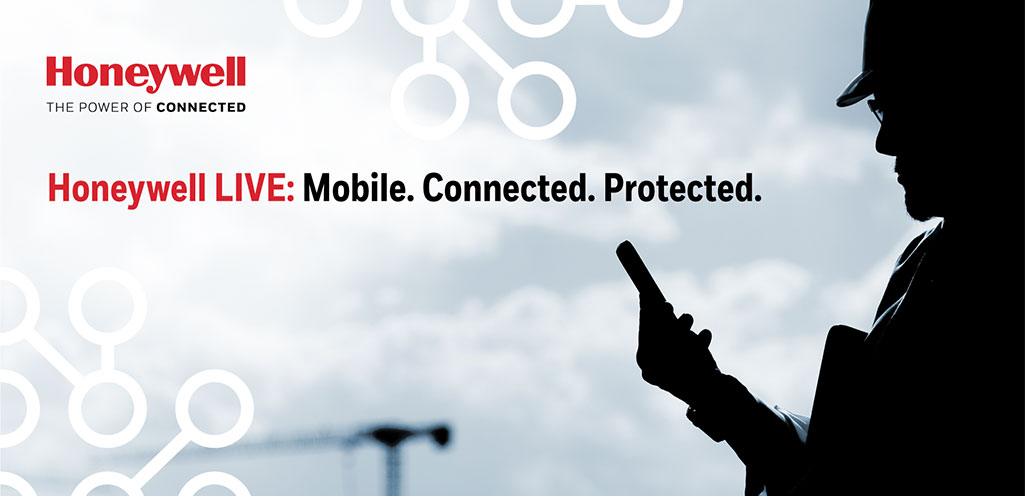
SPONSORED
Improving Safety by Better Connecting Workers
- By Thomas Negre
- Oct 13, 2017
Today, companies across several industries are looking for ways to improve worker safety, prevent or mitigate risks that can lead to business disruption and obtain the real-time data they need to make informed decisions that improve safety and productivity as well as ensure immediate compliance with safety regulations.
Ensuring worker safety is a critical issue as the numbers are staggering. According to the International Labor Organization (ILO), 6,300 people die every day as a result of occupational accidents or work-related diseases, with more than 317 million accidents occurring on the job annually, resulting in extended absences from work. In fact, the economic burden of poor occupational safety and health practices is estimated at 4 percent of global Gross Domestic Product each year, according to ILO.
Worker safety in many parts of the world has improved considerably with better processes and protective equipment, but opportunities to increase safety standards remain. Closing the gaps will require new connected solutions – beyond physical protective equipment – that allow employers to ensure that workers comply with safety standards, stay protected in remote and high-risk situations, and improve productivity through data-driven insights.
Specifically, the future of safety lies in innovative solutions that can connect workers in the field by integrating hardware, software and services to create an ecosystem that delivers business insights to help enhance safety and worker productivity. This can provide industrial operations with better visibility and control over the personal protection, effectiveness and compliance of their workers, by enabling them to monitor the safety of their workers no matter where they are and help optimize their plant and field operations.
Real-time access to better safety data can translate to better visibility on worker compliance. Having a real-time contextual view into safety compliance information can help companies make more informed and safer decisions, so that they can keep everything running smoothly and prevent events that cause costly downtime for workers and equipment, or most importantly loss of life.
Imagine being able to monitor the safety of employees in real-time, providing a second set of eyes to workers, so that they are not only relying on the operator responding correctly to an incident, but also having a supervisor that can monitor the entire workforce and appropriately respond proactively to any alerts or early indicators. This data intelligence coupled with the use of predictive analytics can also help predict where, when and for whom an accident is a risk, so that companies can take the necessary steps to prevent it.
In addition, leveraging technology can also help optimize safety operations and track personal protective equipment (PPE) for compliance. Protective equipment, such as fall harnesses, self-contained breathing apparatuses, gas detectors and thousands of other products at work in a facility, need to be tested daily, weekly, monthly or yearly. By creating a system that alerts operators when equipment inspections are required to more efficiently manage this process, companies can quickly identify out-of-certification gear, as well as plan and schedule those service periods ahead of time, instead of doing it reactively when something happens.
To increase safety and worker productivity, industrial companies need a unified hardware and software platform that can help them monitor and analyze safety data from a centralized location to protect workers in the field. Today, there is technology available that can seamlessly integrate with a company’s operational processes to provide a comprehensive view of the safety environment and everyone working within it—in real time. By leveraging the cloud, such platforms can connect workers, their safety equipment and devices with actionable data collected from a variety of sensors to help industrial companies provide workers with critical safety information on the field, monitor their well-being, immediately identify hazardous situations and coordinate emergency response efforts, and automatically record activities and reporting events to improve safety and ensure compliance.
At the same time, having visibility into critical information about the worker in real time provides companies with the ability to immediately respond to incidents and better knowledge of the location-based. For example, when an incident happens, emergency teams can respond faster, address the issue more quickly and seamlessly, monitor remediation, bring in experts remotely, and alert the rest of the organization as well as local community about any issues.
When you improve safety in the workplace, you not only protect your workers but also protect your company by reducing costs, improving productivity and managing risk – all leading to the ultimate benefit of positively affecting the bottom line and saving lives. But most of all, it helps create an increased culture of safe productivity for future generations.