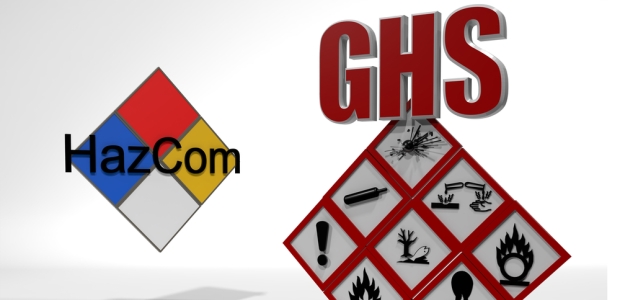
Page 2 of 4
Best Practices for Safety Data Sheets
The one-year anniversary of the final phase-in date for the Occupational Safety and Health Administration’s (OSHA’s) revised Hazard Communication standard (HCS), Title 29 Code of Federal Regulations (CFR) 1910.1200, has come and gone. By June 1, 2016, employers were required to update alternative workplace labeling and hazard communication programs as necessary and provide additional employee training for newly identified physical or health hazards.
A key component of a company's written hazard communication program are Safety Data Sheets (SDSs), which are written or printed materials around hazardous chemicals prepared in accordance with the requirements in paragraph (g) of the HCS.
The HCS habitually finds itself on OSHA's Top Ten Most Frequently Cited Violations, and it made the list again in Fiscal Year 2016. Of the top five sections cited under the HCS, SDSs were referenced—either directly or indirectly—in all five, which validates the crucial role SDSs play. The top five cited sections during FY 2016 were:
- 29 CFR1910.1200 (e)(1): Execution of the written hazard communication program which describes in detail the employer’s labeling, SDSs, and training components.
- 29 CFR1910.1200 (h)(1): Employee training requirements, including chemical-specific information that must always be available through labels and SDSs.
- 29 CFR1910.1200 (g)(8): Maintaining SDSs.
- 29 CFR1910.1200 (g)(1): Developing SDSs.
- 29 CFR1910.1200 (h)(3) (iv): Details in the hazard communication employee training program, including an explanation of labels and the SDSs, including how employees can obtain and use the information.
With a flurry of OSHA regulatory activity at the end of President Obama’s administration that continued into President Trump’s first months in office, it's easy to have lost sight of the state of your hazard communication program. That said, complacency has been the ruin of many good hazard communication programs, and some re-focused attention on your organization's SDSs may help you stay compliant.
Employers are required to have an SDS available for each hazardous chemical they have on site, and the information contained on them is the basis for training their employees on the hazards of the chemicals to which they are exposed, according to 29 CFR 1910.1200 (h)(3)(iv).
The SDS plays a unique role in assisting employers in situations where the chemicals at their facilities have no OSHA permissible exposure limit (PEL). Currently, there are about 500 chemicals that have an established PEL, and the SDS affords the safety decision maker facts to make informed decisions on their potential hazards while conducting a hazard assessment for new chemicals introduced into the workplace.
Hazard Communication Compliance Directive
The best resource for guidance on how an OSHA Compliance Safety and Health Officer (CSHO) will interpret SDS scenarios is OSHA’s compliance directive number CPL 02-02-079, entitled "Inspection Procedures for the Hazard Communication Standard (HCS 2012)." There, you will find detailed instructions designed to provide uniform enforcement of OSHA’s HCS policies and procedures by federal OSHA CSHOs.
There isn't a better way to evaluate a safety and health program for compliance than knowing, in advance, what inspectors will be looking for if—and when—they arrive at a facility. Be aware, this is a federal OSHA document, and state plans are expected to have standards in place that are, at a minimum, as stringent as the federal requirements.
Here are some industry best practices to help keep your SDS library up to date and compliant based on the top five cited sections of the HCS:
1. Execution of the written hazard communication program, which describes the employer's SDS components in detail. Written program SDS requirements are low-hanging fruit for CSHOs because of the complexity and ever-changing nature of organizations. Key SDS components that are sometimes overlooked in the written program include:
- Not identifying employee(s) responsible for obtaining/maintaining the SDSs
- Not describing how the SDSs are maintained
- Not providing procedures to retrieve the SDSs electronically, identifying backup systems in the event of a power failure, or instructing employees how to obtain access to the SDSs
- Not providing procedures in cases where the SDS is not received with the initial shipment of a chemical
- Not providing procedures to follow if the SDS is missing information (blank spaces)
- Not providing instructions on how to identify whether the SDS is the most current version
The old adage of "document, document, and document" comes into play, because if it's not documented, it didn't happen. If an organization has employees who are potentially exposed to hazardous chemicals and there is no written program, but the provisions of labeling, SDSs and training are met, it would not be cited under 1910.1200(e)(1)—it would be viewed as a de minimis violation. However, if the converse is true, and it has a written program but has not applied one or more required elements, it would be cited under the specific section of the deficiency such as labeling, SDS, and/or training.
2. Employee training requirements including chemical-specific information must always be available through SDSs:
CSHOs will evaluate the effectiveness of your organization's hazard communication training by reviewing the program materials and interviewing employees and management. The employees interviewed are not expected to recite verbatim all the information covered in the training. However, they should be aware of the hazards to which they are exposed, understand how to use information on the SDSs, and know and follow job safety practices and protective measures. Conducting random observations and employee interviews to verify hazard communication training retention is a best practice.
3. Maintaining SDSs:
- Employers do not need to maintain SDSs for non-hazardous chemicals.
- The method (i.e., paper or electronic) of maintaining SDSs is left up to the employer as long as the employees have immediate access to the SDS in their work area.
- Older versions of SDSs or Material Safety Data Sheets (MSDSs) may still need to be maintained as an employee exposure record (29 CFR 1910.1020).
- An Internet search is not considered an acceptable method to obtain an SDS.
- Employees must have uninhibited access to SDSs on all shifts. The SDSs cannot be locked in file cabinets or offices or in a location where employees are required to ask for them.
It's a good practice to conduct periodic verification of chemical inventory by randomly reviewing the master inventory list to see whether it matches with the label and SDS identifiers. A CSHO will review a representative sample of chemicals on the shop floor to verify whether the chemical matches the information found on the master list, SDSs, and labels.
Another pain point associated with maintaining SDSs is samples. A best practice to follow is to have documented policies and procedures, along with training of supply chain employees and supervisors to not accept samples without first receiving the appropriate SDS and recording the receipt of the sample. This will help eliminate the undocumented small containers that everybody seems to find on the back bottom shelf of storage cabinets.
4. Developing SDSs:
It is the responsibility of the chemical manufacturer and importer to develop or obtain an SDS for each hazardous chemical they manufacture or import. The information provided on the SDS must conform to the required 16-section format, and the SDS must be sent downstream with the next shipment of the chemical or upon request. Additionally:
- Chemical manufacturers must update their SDS within three months of becoming aware of significant new information.
- SDS requirements apply to no-charge samples provided by chemical manufacturers and importers.
- The SDS must be provided in English but can be translated into other languages to facilitate training and improve retention by workers for which English is a second language.
During the inspection process, a CSHO will review samples of SDSs to determine whether they meet the standard. A CSHO also may need to determine whether a manufacturer or importer exercised "reasonable diligence and made good faith efforts" to obtain updated chemical hazard information. Again, you will need to produce your documentation trail regarding the process to obtain necessary SDSs with upstream suppliers. They will look for attempts by the manufacturer to find hazard information from alternative sources or efforts to classify the data themselves. Also, a CSHO will take steps to verify the SDS transmission program is being followed to downstream recipients.
5. Employee SDS Training Details:
A hazard communication SDS training program should include:
- An overview and explanation of the 16-section SDS format
- Information on where SDSs are located and how to access them
- Information on who to talk to should there be questions about the SDS
- Differences between MSDSs and SDSs
When CSHOs conduct employee interviews, they will focus on specific issues, such as where to locate the SDS and whether or not employees have the necessary computer skills to access SDSs if they are in an electronic format.
Conclusion
OSHA will continue to evaluate whether to align the HCS with the United Nations' Globally Harmonized System of Classification and Labeling of Chemicals (GHS). The United Nations updates the GHS on a bi-annual frequency and currently is on GHS Revision 7, 2017. This implies we could see additional changes down the road from OSHA, since it currently enforces GHS Revision 3, 2009.
SDSs are the backbone of every employer's hazard communication program. Ensuring your organization is compliant and all employees have access to the most current hazard information in the event of an accidental exposure or uncontrolled release is crucial.
Familiarizing yourself with the information contained in OSHA’s compliance directive regarding the HCS is the best place to start your compliance self-assessment. By conducting periodic evaluations of on-site chemical inventories to ensure current SDSs are maintained and developing training for internal partners who request, purchase, or use hazardous chemicals, you can ensure your organization won't become complacent in fulfilling its obligations under OSHA's HCS.
This article originally appeared in the July 2017 issue of Occupational Health & Safety.