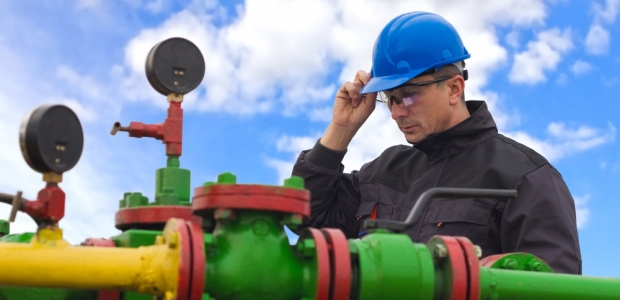
The Significance of API RP 2219 Recommendations in the BLSR Accident, Part II
Employers and workers need to pay special attention to minimum recommended safety requirements of approved standards and safe working procedures.
- By Hamed Khoshniat
- Jun 01, 2017
CSB Recommendations Linked to the API Standard:
For Nobel Energy:
1. Provide documentation of the potential flammability hazard of exploration and production (E&P) waste liquids—such as a material safety data sheet (MSDS)—to all employees, contract personnel, and haulers handling waste liquids generated at well sites. Emphasize that mixing condensate with basic sediment and water (BS&W) during the removal process can significantly increase the flammability hazard. The mixture in the transport container should be treated as a flammable liquid absent positive identification to the contrary.
2. Review and revise company gauging and waste liquid removal protocols as necessary to minimize the inadvertent removal and subsequent disposal of hydrocarbon product when removing BS&W from product storage tanks.
For T&L:
1. Ensure that the written procedures for hazard identification require that all customers requesting loading and transportation of exploration and production (E&P) waste liquids provide written notification, such as a material safety data sheet (MSDS), listing the potential flammability hazard.
2. Ensure that the written procedures for safe operation of vacuum trucks incorporate applicable good practices, including techniques to minimize the possibility of exposing the diesel engine to flammable vapor, as provided in API RP-2219, Guidelines for Commercial Exploration and Production Waste Management Facilities.
3. Develop written operating procedures that incorporate best practices for unloading storage tank waste liquids; such that drivers accurately measure the quantity of liquid removed from the storage tank and minimize removal of product, such as flammable condensate.
4. Ensure that written emergency procedures address the safe response to abnormal diesel engine operation due to a flammable vapor atmosphere. Explain that the normal engine shutoff method will not function as long as flammable vapor continues to enter the intake system.
5. Conduct and document training for all personnel who handle waste liquids, using languages or formats that are clearly understood by all affected personnel.
- Address the potential flammability hazard associated with E&P waste liquids, emphasizing how the withdrawal procedure is likely to increase the flammability of the vacuum truck contents through unavoidable mixing of product and basic sediment and water (BS&W).
- Describe operating and emergency response to diesel engine over speed caused by a flammable vapor atmosphere.
For BLSR:
1. Develop a written Waste Acceptance Plan as recommended by API Order No. G00004, Guidelines for Commercial Exploration and Production Waste Management Facilities.
- Require the shipper or carrier to properly classify the flammability hazard of exploration and production (E&P) waste liquids.
- Require the hauler to provide information that identifies the flammability hazard of the material before accepting the load, such as a material safety data sheet (MSDS).
2. Develop and implement written procedures and provide training to employees on the safe handling of all waste liquids delivered to the facility in accordance with API Order No. G00004, Guidelines for Commercial Exploration and Production Waste Management Facilities; and API RP-2219, Safe Operation of Vacuum Trucks in Petroleum Service.
- Include requirements for proper grounding of trucks and eliminating other sources of ignition (e.g., facility electrical equipment and smoking in unloading areas).
- Ensure that the material is presented in languages or formats that are clearly understood by all affected personnel.
3. Develop written procedures and provide training to employees on unloading all flammable or potentially flammable E&P waste liquids.
- Avoid unloading flammable liquids onto an open work area, such as the mud disposal and washout pad.
- Include alternative unloading method(s), such as using a closed piping system to minimize vapor generation.
- Ensure that the material is presented in languages or formats that are clearly understood by all affected personnel.
4. Develop written emergency procedures and provide training to employees on response to abnormal or emergency situations, including uncontrolled flammable vapor releases that can result in a fire or explosion hazard. Ensure that the material is presented in languages or formats that are clearly understood by all affected personnel.
The Minimum Safety Requirements of API RP 2219 - 2005
According to the API RP 2219 standard, “safe operation of vacuum truck tanks in petroleum service,” the following paragraphs contain the minimum safety requirements that are essential and associated with the BLSR accident.
1) Vacuum truck operators shall be aware that although BS&W may consist primarily of free water, sediment and/or emulsion, it may also entrain flammable or combustible hydrocarbons. Care should be exercised to understand the potential ignition and fire hazards associated with the material being handled. If condensate has been mixed with BS&W during the removal process, this can significantly increase the fire hazard. From a precautionary standpoint the mixture in the transport container should be treated as a flammable liquid absent positive identification to the contrary (section 4.1.4)
2) Unloading materials containing flammable components to open pads or pits can release vapors resulting in a fire, explosion or substance exposure hazard.(section 5.1.1.4)
3) The method chosen for off-loading should include a review of the potential hazards of the material (flammability, corrosivity, and/ or toxicity) and ensure that where necessary, the procedures properly control vapors. Where flammable materials are involved, closed systems or appropriate ventilation may be necessary. Elimination of potential ignition sources can be achieved by proper grounding, bonding, use of intrinsically safe equipment and shutting down equipment not in use (such as truck engines when gravity draining). (section 5.7.2)
4) Smoking, or any other sources of ignition, shall not be permitted within at least 100 feet (depending on local procedures and atmospheric conditions) of the truck, the discharge of the vacuum pump, or any other vapor source (section 5.12.5)
5) Sources of ignition include vacuum truck engine and exhaust heat, pump overheating, faulty or improper electrical devices, static electricity discharges, outside ignition sources such as smoking, motor vehicles, stationary engines, etc.(section 5.1.1.1)
6) Vacuum truck owners shall assure that vacuum truck operators are aware of the physical and chemical characteristics of flammable, combustible, toxic and corrosive materials in accordance with applicable regulations. These regulations include, but are not limited to:
- OSHA 29 CFR 1910.120 (Hazardous Waste Operations and Emergency Response);
- OSHA 29 CFR 1910.1200 (Hazard Communication);
- DOT 49 CFR Parts 106-7, 171 through 180 and 397 407 & DOT 412 (Hazardous Materials Regulations). (section 4.1.1)
7) Vacuum truck owners shall assure that vacuum truck operators are trained, knowledgeable of and comply with applicable federal, state and local regulations including, but not limited to, the following:
- 29 CFR 1910.1000 - 1096, Subpart Z Toxic and Hazardous Substances (including Benzene at 1910.1028)
- 29 CFR 1910.120, Hazardous Waste Operations and Emergency Response
- 29 CFR 1910. 1200, Hazard Communications
- 40 CFR 263, Protection of Environment
- 40 CFR 311.1, Worker Protection Standards for Hazardous Waste Operations
- 49 CFR, Parts 172, 173, 178-179, 382, 383 and 390-397, Motor Carrier Safety (section 4.4)
8) Vacuum truck owners shall prepare an emergency response plan conforming to OSHA requirements at 29 CFR 1910.38 (Employee Emergency Plans and Fire Prevention Plans), and shall train all operators in the use of that plan (4.5.2)
9) Operators can prevent diesel engine acceleration, or "runaway," by locating the vacuum truck upwind of vapor sources and by extending the vacuum pump discharge away from the diesel engine air intake. (section 5.6.1)
10) Vacuum truck operators shall be aware of the hazards involved in petroleum product and associated materials transfer operations. They shall be trained in safe product transfer practices and follow company and facility safety procedures when loading and offloading vacuum trucks. (section 5.7)
11) MSDSs for the products being transferred shall be available to vacuum truck operators. Safe air contaminant levels (PELs and STELs) shall be identified, and a qualified person shall assess the potential for exposure. (section 5.12.1)
12) Vacuum truck owners shall train vacuum truck operators in safe procedures for gauging and sampling flammable and combustible liquids and toxic materials in and around vacuum truck cargo tanks, source containers and receipt containers (section 5.9)
13) The areas in which vacuum trucks are to operate must be free of hydrocarbon vapors in the flammable range, so testing shall be conducted when appropriate (testing shall be conducted before any operation is started, and if necessary, during operations, when off-loading a waste container where pockets or layers of hydrocarbon, hydrogen sulfide, water and other hazardous materials may exist). Where required by facility procedures, permits shall be issued prior to the start of any vacuum truck operations. (section 5.2)
14) Potential hazards include spills, flammable atmosphere within and around the vacuum truck, cargo tank or source container, hose failures and discharges of flammable vapors to the atmosphere from the vacuum truck or the source or receiving container and worker exposures to toxic vapors, liquids or solids. (section 5.1.1.2)
15) Vacuum truck owners and operators, as well as facility personnel, should be aware of the numerous potential hazards associated with vacuum truck operations in petroleum facilities. (section 5.1.1)
16) Whenever liquids or materials are transferred into or from a tank, vessel or container (other than a surface spill), a bonding cable shall be connected from the vacuum truck to the source or receiving container. (section 5.4.1.1)
17) Vacuum truck operators shall be aware that waste products from petroleum operations may contain trace amounts of flammable or combustible liquids and gases or other hazardous materials which may cause serious injury, illness or death, if not properly handled. In addition, vacuum truck operators shall be aware that when under vacuum, even trace amount of hydrocarbons and hydrogen sulfide gas can be easily separated and create flammable and/or toxic atmospheres.(section 4.1.3)
18) Place an appropriate portable fire extinguisher (minimum 20 lb. BC), ready for use, within close proximity of the operation. (section D.4.1.7)
19) When transferring flammable liquids or hazardous materials, vacuum truck operators shall remain positioned between the vacuum truck and the source or receiving tank, vessel or container and within 25 feet of the vacuum truck throughout the operation. Vacuum truck operators shall monitor the transfer operation and be ready to quickly close the product valve and stop the pump in the event of a blocked line or release of material through a broken hose or connection. (section 5.12.4)
20) All personnel shall leave the vacuum truck cab during loading and off-loading operations (section 5.12.3)
21) Vacuum truck operators shall be trained in the use of portable fire extinguishers. Portable fire extinguishers should be provided with the vacuum truck and also be available at the work site. (section 4.5.1)
22) Vacuum truck operators shall know which type of personal protective equipment to use under various conditions of potential exposure or known exposure. Personal protective equipment may be required to provide body, eye and respiratory system protection.(section 4.3.1)
23) In emergency situations such as spill response and cleanup, product safety information may be obtained from sources other than the manufacturer or shipper, including, but not limited to: Chemtrec, Department of Transportation, state and local emergency response agencies, U.S. Coast Guard, fire departments, etc.(section 4.2)
24) Appropriate personal protective equipment, including respirators, shall be worn when a hazard assessment indicates they may be needed to prevent exposures to toxic materials or air contaminants at or above PELs, STELs or relevant TLVs (section 5.12.3)
25) Vacuum truck cargo tanks shall be depressurized, and vapors vented to a safe area, away from personnel and sources of ignition (or to an approved vapor recovery system), before vacuum trucks are driven onto public highways. (section 5.11.2)
26) Vacuum truck operators may provide vertical exhaust stacks, extending approximately 12 feet above the vacuum truck (or higher if necessary), to dissipate the vapors before they reach ignition sources, personnel or other potential hazards. (section 5.6.1)
27) Vacuum truck operators may attach a length of exhaust hose to the vacuum exhaust that is sufficiently long enough to reach an area that is free from potential hazards, sources of ignition and personnel. The hose should be preferably extended 50 feet downwind of the truck and away from the source of the liquids. (section 5.6.1)
28) The vacuum truck owner shall establish a schedule for inspecting and testing the electrical continuity of grounding and bonding cables provided with the vacuum truck (depending on the use and condition of the cables) (section 5.4 – C)
29) Vacuum hoses constructed of conductive material or thick walled hoses with imbedded conductive wiring shall be used when transferring flammable and combustible liquids when the potential for a flammable atmosphere exists in the area of operations.(section 5.3.1)
30) Before beginning operations, vacuum truck operators shall obtain any required permits and inspect vacuum trucks, equipment and loading/off-loading sites to assure safe operations. See Appendices C and D for inspection, maintenance and operating requirements (section 5.1.2)
31) Before starting transfer operations, vacuum trucks should be grounded directly to the earth or bonded to another object that is inherently grounded (due to proper contact with the earth) such as a large storage tank or underground piping. (section 5.4.2)
32) Appropriate personal protective equipment, including respirators, shall be worn when a hazard assessment indicates they may be needed to prevent exposures to toxic materials or air contaminants at or above PELs, STELs, or relevant TLVs
33) Position the vacuum truck in a safe, authorized position, upwind or crosswind from the receiving container. When transferring flammable liquids into a container located within a diked area, place the vacuum truck at least 50 ft upwind from the tank, preferably on top of or outside of the dike (section D.4.1.4)
34) Set the vacuum truck brakes and chock the wheels (section D.4.1.5)
Conclusion
As a result of comparing the investigator's findings and CSB advice with API RP 2219 standard recommendations, we find "what went wrong" that brought about the BLSR accident. If we search industrial accidents to find the main causes, in most of the findings there would be at least one common important issue.
This hidden reality is that employers and their employees need to pay special attention to:
a) Minimum recommended safety requirements of approved standards
b) Providing appropriate training
c) Preparing a safe working procedure.
References
1. CSB investigation report number 2003-06-I-TX September 2003, BLSR Operating , Ltd. Vapor cloud deflagration and fire accident
2. API RP 2219 – 2005 "safe operation of vacuum truck in petroleum service"
3. NFPA 69 – 2002, Standard on explosion prevention system
4. CCPS guideline for consequence analysis of chemical releases - 1999
This article originally appeared in the June 2017 issue of Occupational Health & Safety.