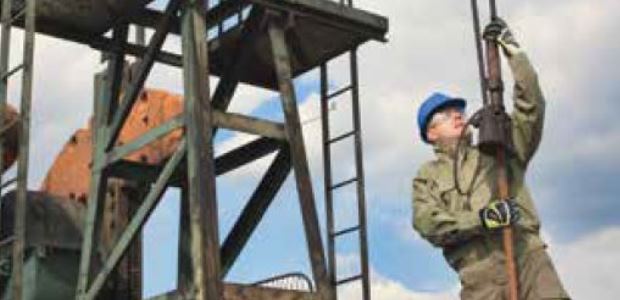
Seven Ways to Go Back to Basics With Your Safety Program
Using effective control factors to streamline PPE selection and simplify conformity across sites has the full attention of today’s safety managers.
- By Jennifer Choi
- Jun 01, 2016
"We are cutting back, but we are not cutting back on safety." I will never forget my first meeting with the global HSE director who said this. I had met him when reports of layoffs and barrel prices plummeting had just begun, and I was hesitant to bring up the proverbial elephant in the room—the decline of a golden industry. But his first statement changed how I perceived the oil industry. Despite everything, the safety professionals in the oil and gas industry are devoted to improving their safety programs for their teams. That was a little over a year ago, when times were sunnier.
With less than 45 percent of rigs operating from a year ago (Baker Hughes, 2016), the oil industry has seen noticeable reductions in its workforce ranging from 10 to 40 percent. In a recent study by Citadel Advisory Group, 92 percent of responding companies have reduced their workforce, with 41 percent of these reducing their staff by more than 30 percent (Addison, 2016). While the contributing factors for the staff cuts are up for debate, the reality of fewer employees to watch over has affected the way safety managers operate.
Staff cuts can influence unsafe behaviors when individuals are expected to perform the task load that was once completed by multiple workers. The natural tendency to cut corners on processes to speed efficiency can lead to exposures that were not factors with larger workforces. Because of the new duties and expectations on the workforce, safety leaders are under pressure to perform magic, often with budget cutbacks to boot.
I often visualize safety managers as the sheepdogs of the industry that fight the battles on behalf of their team, whether known hazards or bureaucracy. These recent staff cuts have led many in the safety industry to focus on their remaining flock with a back to basics approach to safety. The basis of this article was derived from six interviews with HSE directors from large and small oil companies. When interviewed, many safety directors stated that they are looking for improvements that are slam dunks and that uncovering these cost savings often begins at the bottom. With more time to devote to analysis while production is down, safety managers are taking a second look at their programs and shifting their focus to what they can control.
Going Back to Basics
- Refining job hazard assessments: re-evaluating risks and ways to mitigate them through safer engineering, training revivals, and PPE matrix revamps. Safety managers are taking advantage of extra office time by taking a second look at their job hazards. By uncovering new potential hazards or assessing avoidable hazards and enacting preventative steps to minimize likelihood and severity, safety professionals are maximizing their teams’ efficiency with a focus on small details. These are often uncovered through an in-depth review of incident and near-miss reports. Evaluating the PPE matrixes has been another priority that is coming off the back burner. Using effective control factors to streamline PPE selection and simplify conformity across sites has the full attention of today’s safety managers.
- Bridging the generation gap with mentoring programs: Developing the human capital that will be the next generation of the industry can be a challenge. Overcoming the gaps between the sandwich generation and millennials can seem insurmountable. Each group has a unique perspective on work and seemingly opposing values. The aging workforce has altered some perceptions of the industry's best, and the mashup of employees on a site is more diverse today than it has ever been. Developing mentor relationships on sites has helped to reinforce the best characteristics from both factions.
- Focusing on training: Safety professionals view this as the perfect time to add credentials and reinforce basics with their teams. Some companies are cross-training their safety leaders on security, environmental issues, and industrial hygiene platforms. Others are developing their critical/emergency response team training. New toolbox talks on job-specific tasks and risk mitigation, on things such as hand placement, help keep teams alert and engaged.
- Invoking a hands-on/eyes-on approach: The safety manager's job is more than statistics and stickers. Today's safety managers are in the field more than ever and have placed a priority on "putting eyes on the situation" at hand. This mentality has also rolled over to the workforce with new observational safety metrics being trialed. Developing a culture where everyone is in charge of their personal safety and the safety of their peers has helped to boost morale and employee engagement.
- Boosting morale with smaller teams: Many managers relay that it is impossible to 100 percent alleviate their employees' stress over declining industry news. For the people who work in oil and gas, many are waiting for the other shoe to drop. Today, the industry has the luxury of selective hiring that it hasn't had in a while. While it can be stressful to be in the middle of an unsettled industry, safety professionals are encouraging their teams by reminding them that those still working represent the best of the industry. Getting them involved with the safety walk-throughs and offering town hall opportunities for them to input relevant changes is helping to keep morale at manageable levels.
- Researching new technologies and efficiencies: Even with travel cutbacks and budget restraints, top safety managers are still researching new safety technology and products. "We have more time to devote to details, and that is going to help us set the benchmark higher when production resumes," one interviewee stated. Safety professionals continue to explore new frontiers that can make their processes safer and more efficient. Some of these topics include PPE with new safety technology or PPE recycling options that can extend workwear lifetimes and reduce overall costs and waste, as well as cross-industry research that evaluates how seemingly unrelated industries develop universal behavioral safety and human factors issues. Even in a downturn, the introduction of new technology can save companies money, both immediately and over the long run. "Sometimes the decisions that look wrong are the ones that create the wins for the budget and for safety."
- Fine-tuning a safety culture: Those who have experienced previous industry cycles are aware that this is the perfect time to develop their safety culture to one that can grow when the industry rebounds. Planning for the training and development of the next influx of employees is best handled when other distractions are at a minimum. A lack of planning, despite current conditions, can spell disaster if plans are not in place to handle the development of leaders at every level of employment.
Safety professionals in the industry have plenty of tasks on their table despite reductions in workforce numbers. Their ability to wear multiple hats and structure their safety programs to accommodate present and future needs is challenging within the recent constraints of budget and time. Luckily, the overall personality of the safety leaders is positive. The industry is in good hands, and safety professionals are actively working to craft a safety culture that is ready for future growth.
References
1. Addison, Velda. (2016). Survey Shows Downturn’s Impact On Oil, Gas Workforce, Revenues. Retrieved from http://www.epmag.com/survey-shows-downturns-impact-oil-gas-workforce-revenues-844261#p=full
2. Baker Hughes. (2016). Rig Count Overview & Summary Count. Retrieved from http://phx.corporate-ir.net/phoenix.zhtml?c=79687&p=irol-rigcountsoverview
This article originally appeared in the June 2016 issue of Occupational Health & Safety.
About the Author
Jennifer Choi is Vice President of Business Development at Cestus Armored Gloves of Vancouver, Wash. Her role in strategic account management includes hazard assessment, root cause and incident trend analysis, product evolution projects, and change management.