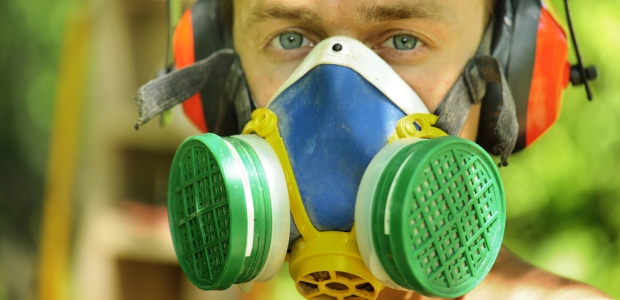
Righting Respirator Wrongs: Correcting Misconceptions for Greater Respiratory Protection
The final step is testing whether the selected respirator suits the workers themselves.
- By Matthew Cromer
- Nov 01, 2015
Increasingly, safety solutions are less separated in terms of quality and performance than ever before—challenging oil and gas companies to equip their workers with the best respirator for their unique working environment. According to the Centers for Disease Control and Prevention, an estimated 20 million workers use personal protective equipment on a regular basis to protect themselves from job hazards1, creating the potential for millions of unique situations that warrant solutions to safeguard each worker against the known and unknown.
Despite supervisors' best efforts to minimize risk, respiratory protection still fell within OSHA's 2014 Top Ten Most Frequently Cited Violations2. And while safety solution providers continue to work toward developing innovative devices with a goal of "zero accidents," it is through continuous education and training that the end users will remain ahead of the curve on best practices and be provided with correct information regarding respiratory protection.
'One size fits all'…
is a dangerous, and potentially fatal, mentality when it comes to respiratory protective devices. Selecting a respirator is like selecting a work boot—its design should offer the greatest protection for the type of environment and level of stress it will undergo, while conforming to one’s physical features to provide the utmost protection and comfort. To have total confidence that a respirator will protect workers against life-threatening conditions, all parties involved in the selection process must be well educated and have a firm understanding of the cautions, limitations, and restrictions of use accompanying all respirator models under consideration.
When choosing a respirator, workers must not only be made aware of the potential of different gases impacting the areas they occupy, but also they must understand the specific hazards their respirator can protect against. While simply donning the device in a hazardous event will provide workers with basic protection, in order to truly maximize safety, a number of considerations must be made before determining the best respirator for the work at hand. Awareness and education of potential respiratory risks are foundational to fostering a thriving work environment where worker safety is a priority.
Performing the Risk Assessment
Prior to identifying the respirator, however, the vital first step in the selection process is to perform a risk assessment. This helps establish all of the potential areas of work site risk and should be conducted initially and upon each introduction of new processes and equipment. It is up to company leadership to be aware and educated regarding new and changing regulations for their specific industry, as these may that require new risk assessments be performed.
To aid in the risk assessment process, the following predefined checklist of criteria can be referenced, such as the NIOSH Respirator Selection Logic3:
- General use conditions, including determination of contaminant(s);
- Physical, chemical, and toxicological properties of the contaminant(s);
- NIOSH recommended exposure limit (REL), OSHA permissible exposure limit (PEL), American Conference of Governmental Industrial Hygienists (ACGIH) Threshold Limit Value (TLV), or other applicable occupational exposure limit;
- Expected concentration of each respiratory hazard;
- Immediately dangerous to life or health (IDLH) concentration;
- Oxygen concentration or expected oxygen concentration;
- Eye irritation potential; and
- Environmental factors, such as presence of oil aerosols.
To further supplement this investigation, managers would be wise to consider hiring an industrial hygienist to conduct the risk assessment to recognize and evaluate workplace conditions. The hygienist should not only be a specialist in the industry, but also hold a valid certificate and meet all licensing mandates. Managers can also conduct their own risk assessment in tandem with the industrial hygienist to ensure all priority areas are mapped and accounted.
Determining the Appropriate Respirator Type
Should the risk assessment reveal workers are in the presence of hazardous contaminants in concentrations that exceed recommended limits, OSHA requires that employers "provide the respirators which are applicable and suitable for the purpose intended4." The danger to a worker's health directly corresponds to the concentration of exposure in parts per million (ppm) and the duration of exposure. Once these have been identified, the proper respirator protection level can be determined by referring to the NIOSH Pocket Guide to Chemical Hazards.
For example, the suggested respirator types for the corresponding hydrogen sulfide (H2S) exposure concentrations are shown below:
- 0-10 ppm: No respirator is needed, below REL.
- 10-100 ppm: Powered Air-Purifying Respirator (PAPR), Full Face Mask Cartridge Respirator, or Self-Contained Breathing Apparatuses (SCBA).
- 100-100,000 ppm: SCBA or Supplied Air in positive pressure mode.
While the above are specific to H2S concentrations, similar regulation charts for gas/dust particles are available for each work environment.
Ensuring the Proper Fit
While it is imperative that the aforementioned steps be taken to determine which respirator will provide the ultimate protection, it is important to acknowledge that every user will use and wear the device differently. Like the research that goes into the perfect work boot, risk assessment and respirator type analysis lay a strong foundation for directing managers and supervisors toward the solution that meets all of the work site's demands, but the final step is testing whether the selected respirator suits the workers themselves.
Before frontline workers step into potentially hazardous environments, companies would be wise to adhere to OSHA’s standards on respiratory protection on fit testing, section 1910.134(f), which states, "the employee must be fit tested with the same make, model, style, and size of respirator that will be used." Each tight-fitting facepiece respirator must pass an appropriate qualitative fit test (QLFT) or quantitative fit test (QNFT)—see the sidebar for appropriate protocols. Once the respirator has passed either of these tests, it must be returned to its NIOSH-approved configuration, removing any modifications made to the device during fit testing, before it can be used out in the field. Additionally, loose-fitting respirators must be inspected to confirm that the air flow to the hood is not inhibited in any way and the positive pressure is maintained within the hood.
Without ensuring the proper fit of the respirator, the groundwork laid by the risk assessment and respirator type analysis isn't as impactful in guiding the respirator selection for maximum safety.
A Respirator Is Good Until Its Expiration Date
Yes and no. While these safety solutions are designed and crafted to meet, if not surpass, their designated occupational exposure limits, additional legwork is required to maintain optimal performance levels. Like a car, a respirator requires maintenance to ensure it remains operable while delivering effective protection. Smart respirator maintenance not only extends the life cycle of the product, but also it leads to cost savings. For example, replacing the filter in certain respirators after eight years can double the life cycle, greatly reducing cost of ownership and long-term maintenance costs. To simplify this process, some safety companies offer filter replacement services and training for safety equipment users.
Several factors play a role in a respirator's lifespan, including its use, storage, inspection, cleaning, disinfection, and necessary repair. The durability of a respirator used in higher exposures of toxins is worn away more quickly, requiring more frequent maintenance and testing in order to ensure continued worker safety. This strengthens the importance of performing a test that ensures proper fit.
If prolonged use or improper storage leads to cracks in the material or leaks along the tight seal against a worker’s face, he or she is in danger of breathing contaminated air permeating through these openings. To ensure a respirator performs to the best of its capabilities and lasts, a proper maintenance program includes:
- Cleaning and disinfecting: Contaminant removal and product sanitization protects the wearer, and future wearers, from coming into contact with hazardous materials and maintains that the equipment’s functionality has not been compromised by particulate residue.
- Storage: While safeguarding against damage, respirators must be kept so they retain their natural position and aren’t subject to deformation.
- Inspection: Regular examination helps ensure the continued reliability of the respirator. The frequency and procedures depend on the respirator type (non-emergency, emergency, or escape use only, which are outlined in OSHA's Technical Manual, Section VIII, Chapter 2. Respirator Protection5).
- Repair: Repairs or modifications must adhere to the manufacturer's guidelines and should be performed only by trained personnel. If a device fails inspection or is damaged in some way, it must be removed from service immediately until proper service is completed.
Companies that place a premium on safety and want to fully safeguard their workers should seek out a respirator that meets the highest safety criteria, designed with workers' respiratory protection as top priority. Knowledge is the best defense against the unexpected, and it is the key to helping companies position themselves and their workers for a safe future.
References
1. http://www.cdc.gov/niosh/ppe/
2. https://www.osha.gov/Top_Ten_Standards.html
3. http://www.cdc.gov/niosh/docs/2005-100/pdfs/2005-100.pdf
4. https://www.osha.gov/pls/oshaweb/owadisp.show_document?p_table=STANDARDS&p_id=12716
5. https://www.osha.gov/dts/osta/otm/otm_viii/otm_viii_2.html
Sidebar: Fit Testing for Tight-Fitting Respirators
1910.134(f)(8)(i)
Qualitative fit testing of these respirators shall be accomplished by temporarily converting the respirator user's actual facepiece into a negative pressure respirator with appropriate filters, or by using an identical negative pressure air-purifying respirator facepiece with the same sealing surfaces as a surrogate for the atmosphere-supplying or powered air-purifying respirator facepiece.
1910.134(f)(8)(ii)
Quantitative fit testing of these respirators shall be accomplished by modifying the facepiece to allow sampling inside the facepiece in the breathing zone of the user, midway between the nose and mouth. This requirement shall be accomplished by installing a permanent sampling probe onto a surrogate facepiece, or by using a sampling adapter designed to temporarily provide a means of sampling air from inside the facepiece.
This article originally appeared in the November 2015 issue of Occupational Health & Safety.