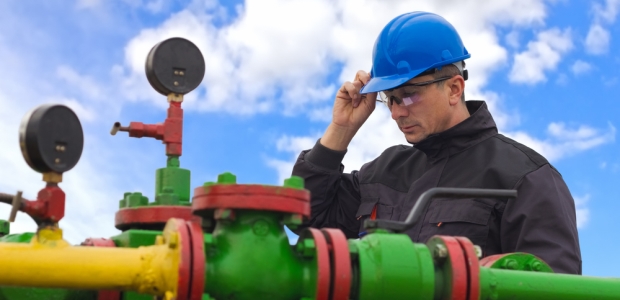
Keeping Oil and Gas Workers Safe and Avoiding Costly Penalties
Exposures to hazards present in the oil and gas well drilling, servicing, and storage industry are addressed in specific standards for general industry.
- By Sally J. Smart
- Jun 01, 2015
The oil and gas industry is vital to our nation and to our nation's economy. The rapid expansion of U.S. unconventional oil and natural gas production has presented tremendous growth opportunities in recent years, and production is projected to continue to expand, with vast amounts of technically recoverable reserves for both oil and gas.
Safety and health awareness is a vital constituent of oil and gas activities because most of the operational conditions, chemicals, and end products are known to pose serious threats. All employers, employees, and contractors within all three segments of the oil and gas industry (upstream, midstream, and downstream) are responsible for ensuring safe and healthful work sites.
Oil and gas workers are generally susceptible to the following safety and injury hazards:
- Motor vehicle accidents
- Contact injuries
- Fires and explosions
- Slips, trips, and falls
- Confined spaces
These workers also may be exposed to chemical hazards (toxics, corrosives, carcinogens, asphyxiates, irritants, and sensitizers); physical hazards (noise, vibration, radiation, and extreme temperatures); biological hazards (viruses, parasites, and bacteria); ergonomic hazards; and psychosocial hazards (odd working hours, isolated sites, and overwork). These exposures may lead to an array of possible health effects.
The top 10 Occupational Safety and Health Administration standards that were cited by federal OSHA for the North American Industrial Classification System (NAICS) Code 211 (Oil and Gas Extraction) during fiscal year 2014 (Oct. 1, 2013 through Sept. 30, 2014) were: 1910.119, Process safety management of highly hazardous chemicals; 1910.37, Maintenance, safeguards, and operational features for exit routes; 1910.1200, Hazard Communication; 5A0001, OSH Act General Duty paragraph; 1910.132, Personal Protective Equipment general requirements; 1910.215, Abrasive wheel machinery; 1910.303, Electrical general requirements; 1910.305, Wiring methods, components, and equipment for general use; 1910.23, Guarding floor and wall openings and holes; and 1910.134, Respiratory protection.
This article will examine some of the most common violations for each standard listed and offer key steps that can be taken to not only keep workers safe, but also to avoid costly penalties.
29 CFR 1910.119: Process Safety Management
Under OSHA's process safety management standard, employers are required to develop, implement, and update process safety management programs for hazardous chemicals at their facilities. The majority of violations relate to the failure to develop and implement written procedures for mechanical integrity and operating procedures; failure to complete thorough process hazard analyses; and failure to annually certify that operating procedures are current and accurate.
29 CFR 1910.37: Maintenance, Safeguards, and Operational Features for Exit Routes
OSHA defines an exit route as "a continuous, unobstructed path from anywhere in a work area to the exit." Workplaces must have two or more exit routes, depending upon the number of people involved (check your local fire codes) and the layout and size of the area. These routes must be permanent, unobstructed, and have adequate lighting. They also must be free of highly flammable furnishings, decorations, and other materials and must not pass through or into dead ends or lockable rooms. These routes must be at least 6 feet, 8 inches high at all points and 28 inches wide at all points between handrails.
29 CFR 1910.1200: Hazard Communication
OSHA notes that most Hazard Communication violations involve basis mistakes--not having a written Hazard Communication program, incorrect shipped to and workplace labeling, lack of employee training, and failure to make safety data sheets (SDSs) available.
5A0001: OSH Act General Duty Clause
The General Duty Clause of the OSH Act requires employers to provide workers with a safe workplace that does not have any recognized hazards that cause or are likely to cause death or serious injury. Exposures to hazards present in the oil and gas well drilling, servicing, and storage industry are addressed in specific standards for general industry.
Site preparation is the only aspect of oil and gas well drilling and servicing operations covered by 29 CFR 1926. Site preparation includes activities such as leveling the site, trenching, and excavation. All other aspects of oil and gas well drilling and servicing operations are covered by 29 CFR 1910. When a serious hazard exists in the workplace that is not addressed by a specific OSHA standard, Section 5(a)(l) of the OSH Act (the General Duty Clause) applies.
29 CFR 1910.132: Personal Protective Equipment – General Requirements
Employers are required to provide, at no cost to employees, flame-resistant clothing for applications such as, but not limited to, the handling of flammable chemicals. OSHA has cited 1910.132(a), for failure to provide and ensure the use of flame-resistant clothing necessary to protect employees from burns due to flash fires; 1910.132(b), for failure to ensure that employee-owned flame-resistant clothing is properly maintained and sanitary; and 1910.132(c), for failure to provide flame-resistant clothing that is of safe design and construction for the work being performed.
OSHA has referred to consensus standards such as NFPA 2112, Standard on Flame-Resistant Garments for Protection of Industrial Personnel against Flash Fire, and NFPA 2113, Standard on Selection, Care, Use, and Maintenance of Flame-Resistant Garments for Protection of Industrial Personnel Against Short-Duration Thermal Exposures.
29 CFR 1910.215: Abrasive Wheel Machinery
One of the most common pieces of machinery in use in all maintenance shops is the abrasive wheel grinder. Violations related to abrasive wheel exposure adjustments always rank high.
Side guards must cover the spindle, nut, and flange and 75 percent of the wheel diameter. The work rest must be kept adjusted to within 1/8 inch of the wheel. The adjustable tongue guard on the top side of the grinder must be kept to within 1/4 inch of the wheel. The maximum revolutions per minute (RPM) of each abrasive wheel must be compatible with the RPM rating of the grinder motor. Before new abrasive wheels are mounted, they must be visually inspected and ring tested.
29 CFR 1910.303: Electrical – General Requirements
Exposure to electric shock led the pack for these violations. Follow manufacturers' instructions when designing, installing, and using electrical equipment to maintain compliance and avoid workplace incidents. Protecting workers also requires an effective training program that looks to ensure that all workers know how to avoid electric shock.
29 CFR 1910.305: Electrical – Wiring Methods
Commonly identified hazards include the use of flexible cords instead of fixed wiring, inadequate protection for workers entering boxes, and exposures to live contacts. Inspect wiring and insulation, plus take steps to ensure proper grounding of electrical equipment to help avoid potential violations.
29 CFR 1910.23: Guarding Floor and Wall Openings and Holes
Floor holes and open-sided floors led the way for these violations. Every floor hole into which a person can accidently walk must be guarded by either a standard railing with a standard toeboard on all exposed sides or with a floor hole cover. Every open-sided floor or platform 4 feet or more above adjacent floor or ground level must be guarded by a standard railing on all open sides, except where there is an entrance to a ramp, stairway, or fixed ladder.
29 CFR 1910.134: Respiratory Protection
There is a huge margin of error when it comes to outfitting workers with the correct respiratory protection. Lack of proper respirator selection protocols and lack of or poor fit-testing were among the top citations. Other common violations include not having a written program for respiratory protection or procedures for voluntary use.
Three Lines of Defense
By using OSHA's recognized three lines of defense philosophy, potential exposures to identified hazards can be reduced or eliminated via:
1) Engineering controls
2) Work practice controls/administrative controls
3) Personal protective equipment
Engineering controls are the preferred methods of minimizing exposure (first line of defense) and may include substitution, isolation, or ventilation. If feasible, the equipment or process should be designed to remove the hazard or substitute something that is not hazardous. If removal is not feasible, then the hazard should be isolated/enclosed to prevent exposure in normal operations. Where complete enclosure is not feasible, then local ventilation to reduce exposure to the hazard in normal operations may be suggested.
OSHA has found that appropriate work practices can be vital in lowering worker exposures, especially to airborne hazardous substances. Fundamental work practices include good housekeeping, personal hygiene practices, periodic inspection and maintenance of process and control equipment, and use of proper procedures to perform a task.
Administrative controls influence the way a task is performed, and these generally involve the scheduling of the work or the worker and training.
PPE, the last line of defense, is equipment worn to minimize exposure to potential workplace injuries and illnesses. When engineering and administrative controls are not feasible, while such controls are being implemented, or in emergencies, employers must provide PPE to their workers and ensure its proper use.
Companies in all three segments of the oil and gas industry can achieve their goals of managing and mitigating risks via standardization. Focused standardization leads to optimum product selection and processing efficiencies that are not only easier to initiate, but also easier to maintain at multiple work sites.
This article originally appeared in the June 2015 issue of Occupational Health & Safety.