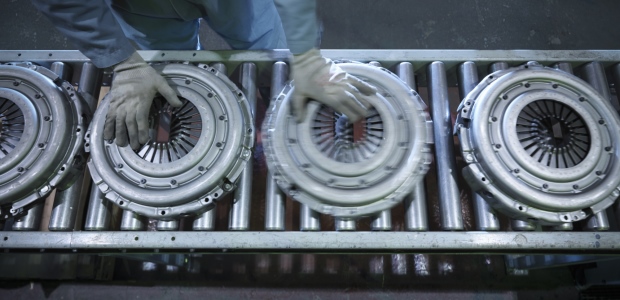
Gloves That Fit the Worker and the Job
Match the level of cut protection to that of the immediate hazard level at hand.
- By Shelly Baize
- Feb 01, 2015
It's a powerful fact, reinforced by Bureau of Labor Statistics data: Hand injuries trail only back problems in terms of frequency in the workplace. Further, OSHA records show that 70 percent of hand injuries were suffered by workers who were not wearing gloves, while the hand protection worn by the remaining 30 percent was inadequate.
Accordingly, the two main goals of workplace hand protection are ensuring that the cut resistance of work gloves matches the level of the cut hazards present and then, even more importantly, assuring that workers do in fact wear the gloves on the job.
Standards of Resistance
To enable worthwhile comparisons of glove performance, safety and health organizations have established standards for hand wear cut resistance. The ANSI/ISEA standard generally used in the United States sets cut levels from 1 to 5, representing how resistant a certain material is to a cutting edge applied under specific loads. Higher levels provide more protection.
For example, gloves with a cut resistance level of 5 might be used in high-risk applications, such as food processing and plate glass handling; gloves with level 2 resistance may be appropriate for less hazardous work in construction and packaging. However, the practical application of the standards is not that simple. The true level of risk is influenced by variables in the work environment and the actual hazards involved, such as differences between slicing, abrasive, and impact cuts or puncture resistance as opposed to linear cuts.
Safety audits, internal safety directors, or industry personal protective equipment experts can help determine the level of risk in a specific situation and determine which level of protection is most appropriate and cost effective. On-site testing and worker input is essential, as well.
Those responsible for glove selection should be aware that the standard EN388, used in Europe, Asia, South America, Mexico, and parts of Canada and the United States, is not interchangeable with the ANSI system and can muddle the selection process. If differences in the standards appear to play a role in the choice of gloves, buyers should familiarize themselves with the properties the standards represent and determine how to apply them to their specific situations.
Material Performance
A glove’s basic cut resistance depends on the material(s) from which it is made and the material thickness or weight per square inch. Heavier thickness and advanced materials improve cut protection, while lighter-weight gloves can offer more flexibility and be less tiring to wear, resulting in less hand fatigue. Additional features such as coatings can improve grip but may not be appropriate for applications such as food processing.
Regarding the relative performance of glove materials, a simplified ranking of cut resistance capability from least to most begins with leather, cotton, and synthetics such as nylon and polyester, and it progresses through high-performance materials to engineered composite yarns made with varying combinations of synthetic materials, fiberglass, and stainless steel.
Manufacturers offer a wide and growing selection of high-performance cut-resistant glove materials with differing performance characteristics. They include para-aramid synthetic polymer (plastic) fibers, ultra-high molecular weight polyethylene (UHMW PE) material, and advanced technology aramid (ATA) fibers. Advanced technology aramid (ATA) yarn is a high-performance fiber with a softer feel, greater breathability, and higher cut resistance compared to other materials.
To handle specific cut hazards, glove makers combine different glove material properties, such as hardness, lubricity, and the ability to roll away from sharp cutting edges. Blended yarns, such as those incorporating high-strength fibers and steel, allow manufacturers to produce gloves with higher levels of cut resistance than achievable with one kind of high-strength fiber alone.
The cut-resistant materials are utilized in various glove constructions, including metal mesh, cut and sewn, and seamless knitted gloves. Metal mesh gloves are made of rings of stainless steel and are typically used in more hazardous applications. Their interlocked construction is extremely resistant to abrasion, cut, corrosion, and puncture. Cut and sewn gloves can consist entirely of a high-performance cut-resistant material or be assembled from less costly materials with cut-resistant material comprising a full or palm lining.
Beyond cut resistance, the selection of gloves can depend on other issues, such as the ability to clean them.
If the Glove Fits
Considering that 70 percent of hand injuries are sustained by gloveless workers, it’s obvious that getting workers to wear protective gloves is a key issue. Gaining end user acceptance is at least equal to and in many cases may be more critical than cost issues. No matter how low a glove’s cost, if the worker won’t wear it, the investment is 100 percent wasted. On the other hand, a slightly higher-priced glove that the end user does wear multiplies the added investment when it prevents a single time-lost accident.
In any case, even the best-performing glove is of little worth if the end user puts it aside because it is uncomfortable or it makes his or her work more difficult. Unfortunately, it’s not uncommon for a buyer to choose a certain style of cut-protection glove based largely on price and then find that function, fit, or other considerations force a re-evaluation and another purchase of a style that is more expensive but works better. It is essential to acquire end user testing input on fit, comfort, and flexibility, as well as issues such as cuff style and even color. Comfort and ease of use as well as a sense of ownership can motivate workers to use the gloves faithfully.
As in many other circumstances, advanced technology provides great benefits in terms of increased performance while it simultaneously complicates the selection process. When decades ago the choice might have been limited to either rubber or leather, today the wide variety of glove materials, performance properties, and styles enables the end user to essentially custom-tailor glove construction to maximize safety, comfort, and cost-effectiveness for a particular application. Careful research of glove suppliers’ comprehensive offerings, understanding of cut-resistance standards, and full use of safety-related resources will enable end users to choose gloves that maximize the return on this important investment in worker safety.
Please consult your safety professional to determine the right glove for your particular application. Always ensure your selected glove complies with the mandated safety standard recommended for your particular application.
This article originally appeared in the February 2015 issue of Occupational Health & Safety.